-
- News
- Books
Featured Books
- pcb007 Magazine
Latest Issues
Current IssueSales: From Pitch to PO
From the first cold call to finally receiving that first purchase order, the July PCB007 Magazine breaks down some critical parts of the sales stack. To up your sales game, read on!
The Hole Truth: Via Integrity in an HDI World
From the drilled hole to registration across multiple sequential lamination cycles, to the quality of your copper plating, via reliability in an HDI world is becoming an ever-greater challenge. This month we look at “The Hole Truth,” from creating the “perfect” via to how you can assure via quality and reliability, the first time, every time.
In Pursuit of Perfection: Defect Reduction
For bare PCB board fabrication, defect reduction is a critical aspect of a company's bottom line profitability. In this issue, we examine how imaging, etching, and plating processes can provide information and insight into reducing defects and increasing yields.
- Articles
- Columns
- Links
- Media kit
||| MENU - pcb007 Magazine
EIPC Technical Snapshot: PCB Surface Finishes
December 28, 2020 | Pete Starkey, I-Connect007Estimated reading time: 7 minutes
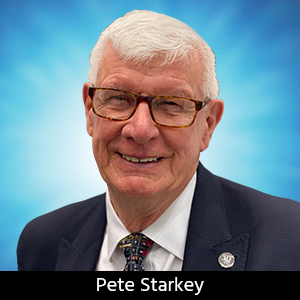
For the third in a series of Technical Snapshot webinars, EIPC chose to focus on PCB surface finishes, comparing specific properties, examining corrosion behaviour and discussing selection criteria for low-loss, high frequency applications.
Dr. Laura Frisk
In a programme hosted and moderated by EIPC Technical Director Tarja Rapala-Virtanen, the opening presentation came from Dr. Laura Frisk, CEO of Trelic, a spin-off company from Tampere University of Technology in Finland that specialises in electronics materials and reliability testing. Referring to several studies of PCB finishes in which her team had participated, Frisk discussed the results of corrosion testing using different techniques.
Corrosion was an important consideration in choosing a suitable finish, especially as electronic devices were expected to work in increasingly demanding environments—one typical example is the mining industry. As features sizes continued to diminish and density increased, corrosion became a key reliability risk, with early failure a probable consequence. Different metallic layers increased the susceptibility to galvanic corrosion and, especially in instances of crevice corrosion, failure could happen very quickly. It was critical to understand corrosion behaviour, how to test it, and how to mitigate it.
High humidity was required to support the majority of corrosion mechanisms. Contaminants contributing to corrosion could originate from many sources, and several different test methods could be employed, using relevant corrosive chemicals such as chlorine, as chlorine gas or sodium chloride, sulphur, as sulphur dioxide or hydrogen sulphide, and nitrogen dioxide.
Frisk described the principles of salt-spray testing, flowers-of-sulphur testing for creep corrosion on PCBs, and mixed-flowing-gas testing of electronic components and assemblies, as well as humidity testing for studying the effect of residual impurities on products.
Her examples of PCB surface finish options were hot air solder levelled (HASL), electroless nickel immersion gold (ENIG), immersion tin, immersion silver, and organic solderability preservative (OSP). She demonstrated how different finishes were vulnerable to different corrosive elements, remarking that the quality of surface finish was critical, and that certain finishes were consumed during the soldering operation.
Summarising test results, she explained how a 1,500-hour salt-spray test revealed significant corrosion on ENIG and OSP, and some corrosion—but no failures on immersion silver. A six-week mixed-flowing-gas test gave significant creep corrosion on ENIG and OSP, and lots of corrosion products on HASL. Immersion silver and immersion tin showed clear evidence of corrosion but the corrosion products spread less than with HASL and ENIG. Flowers-of-sulphur testing for five days at different levels of humidity showed significant corrosion of immersion silver, some corrosion of immersion tin and very little corrosion of ENIG. The effect of humidity was not linear. All of the test results were clearly illustrated with photographs and microsections. She commented that conformal coating could be used to protect surfaces from corrosion, but this was a subject for a separate discussion.
Dr. Britta Schafsteller
Even if judged purely on considerations of corrosion, Frisk’s results had plainly indicated that no single finish covered all expectations. An in-depth comparison of the key properties, benefits and limitations of different surface finishes came from the second speaker, Dr. Britta Schafsteller, global product manager-selective finishing with Atotech in Berlin.
Summarising the task of a surface finish, it was required to protect the copper surface from tarnishing and oxidation, and to maintain an active surface for various interconnect techniques. Schafsteller’s slide illustrating “various interconnect techniques” gave an indication of the breadth of choice of finish, ranging from organic solderability preservatives (OSP) and hot air solder levelled (HASL), through immersion tin, immersion silver, electroless nickel immersion gold (ENIG), electroless nickel electroless palladium immersion gold (ENEPIG), and electroless palladium autocatalytic gold (EPAG), to electroplated nickel electroplated gold (E-Ni/E-Au). And with a range of functional requirements including single soldering, multiple soldering, copper-wire bonding, aluminium-wire bonding, gold-wire bonding, touch-contacts, press-fit and adhesive bonding, together with many permutations and combinations, the selection was extraordinarily complex.
Describing individual finishes, she began with OSPs, a series of chemistries that had evolved through several generations from simple benzotriazole to various substituted benzimidazoles. OSPs were used mainly on consumer products and, to a limited extent, in automotive applications. The application process was simple and the finish was displaced in the soldering operation, enabling a copper-tin intermetallic joint. A nitrogen atmosphere was required for soldering and the finish had a relatively short storage life,
Immersion tin was widely used in automotive applications. Deposition of the finish involved a chemical displacement reaction whereby copper was replaced by tin. Relatively low-cost, it had reasonably good shelf life and corrosion resistance. Soldering produced a copper-tin intermetallic joint, and the finish could also be used in press-fit applications. It was suitable for use in high frequency electronics. Precautions were required to control whisker growth. Because the deposition chemistry was acidic it could attack solder mask, and good rinsing was essential to avoid ionic contamination.
ENIG had a long shelf life and was suitable for multiple lead-free soldering cycles. The gold was dissolved by the solder and a tin-nickel intermetallic joint was formed, with nickel acting as a diffusion barrier between solder and copper. The finish was suitable for aluminium wire-bonding and touch-contact applications. The precious metal cost made it an expensive finish, and, because of the presence of the nickel layer, solder joints tended to be brittle and it were not suitable for high frequency applications.
Compared with ENIG, ENEPIG was suitable for both aluminium and gold wire-bonding and gave a higher level of solder joint reliability, because the palladium layer acted as a barrier against hyper-corrosion during gold deposition and also reduced the formation of brittle tin-nickel intermetallic. But the overall process was relatively complex and required tight control.
EPAG (electroless palladium autocatalytic gold) eliminated the nickel layer and enabled reliable solder joints to be formed through a ductile tin-copper intermetallic. It was suitable for multiple soldering with both tin-lead and lead-free alloys, as well as wire-bonding with pure-copper, copper-palladium and gold wire. And it was appropriate for high frequency applications. However, it was a relatively new finish with higher process costs because of the precious metal content.
The metallurgy of solder-joint intermetallic compounds had been extensively studied across the whole range of finishes, before and after aging, and Schafsteller showed the results of high-speed shear-tests that had been used to compare joint strengths and fracture energies.
She commented that specific applications required specific finishes, and that the choice of finish should represent a balance between cost and application needs. The target of her team’s new developments was to address multiple applications at reduced process cost with competitive performance.
She ended her presentation with a glimpse of a new palladium electrolyte for pure deposits, a new mixed-reaction gold designed to avoid corrosive attack in ENIG and ENEPIG applications, and a fully autocatalytic tin process with no limitation in plating thickness.
Dr. Kunai Shah
It had already been mentioned that PCB finishes could significantly affect the integrity of high-frequency, high-speed electronic signals, and particularly that finishes based on electroless nickel were not ideal candidates for such applications because of insertion-loss effects. Dr. Kunal Shah, president and chief scientist at LiloTree, illustrated this with a graph of loss versus frequency comparing an uncoated copper conductor with one finished in ENIG, showing that at 50GHz the loss for the ENIG example was more than 50% greater than that of bare copper as a consequence of nickel’s inferior conductivity and ferromagnetic properties.
It was clear that a less “lossy” finish was required for 5G applications, and that the elimination of electroless nickel would also overcome possible hyper-corrosion and brittle-solder-joint effects. Shah commented that currently available nickel-free finishes—such as electroless palladium immersion gold (EPIG), electroless palladium autocatalytic gold (EPAG) and direct immersion gold (DIG)—did not meet all of the criteria for high frequency applications, with concerns of higher insertion loss and brittle solder joints as consequences of resorting to greater thicknesses of precious metals which were neither cost-effective nor eco-friendly.
He described an innovative nickel-less approach by depositing a proprietary nano-engineered barrier on copper features as a foundation for 50 nanometre layer of cyanide-free gold. The gold thickness was significantly less than that of DIG or EPIG or EPAG, with corresponding savings in precious metal cost and less risk of solder joint embrittlement. The finish was applied in a simple 8-tank process line of four active stages and four rinses.
Results were impressive. The graph of loss versus frequency showed the insertion loss of the new finish to be almost identical to that of bare Cu over the 0-100GHz frequency range.
The effectiveness of the barrier layer in preventing diffusion of copper into the gold was demonstrated by the absence of any corrosion products on the gold surface after six reflow cycles.
Solderability testing to MIL-STD-883 Method 2003 after eight hours of steam conditioning followed by dry baking at 100°C for one hour in nitrogen showed no evidence of failure, and the characteristics of the copper-tin intermetallic layers were considered superior to those formed with EPIG or EPAG. Neither were any brittle intermetallic solder joint failures observed in pull and shear tests. These results indicated that, in addition to its superior high-frequency performance, the new finish offered better solder-joint reliability as well as significant savings in gold usage compared with ENIG and ENEPIG.
After moderating the question-and-answer session, Tarja Rapala-Virtanen thanked the presenters and attendees, as well as her EIPC colleagues for organising another successful technical snapshot event. Wishing a happy Christmas to all, she announced that the next webinar was scheduled for January 20, although she hoped that 2021 would bring opportunities for returning to EIPC’s renowned live conferences.
Testimonial
"Advertising in PCB007 Magazine has been a great way to showcase our bare board testers to the right audience. The I-Connect007 team makes the process smooth and professional. We’re proud to be featured in such a trusted publication."
Klaus Koziol - atgSuggested Items
Indium Corporation Promotes Two Leaders in EMEA (Europe, Middle East, and Africa) Markets
08/05/2025 | Indium CorporationWith its commitment to innovation and growth through employee development, Indium Corporation today announced the promotions of Andy Seager to Associate Director, Continental Sales (EMEA), and Karthik Vijay to Senior Technical Manager (EMEA). These advancements reflect their contributions to the company’s continued innovative efforts with customers across Europe, the Middle East, and Africa (EMEA).
MacDermid Alpha Electronics Solutions Unveils Unified Global Website to Deepen Customer, Talent, and Stakeholder Engagement
07/31/2025 | MacDermid Alpha Electronics SolutionsMacDermid Alpha Electronics Solutions, the electronics business of Elements Solutions Inc, today launched macdermidalpha.com - a unified global website built to deepen digital engagement. The launch marks a significant milestone in the business’ ongoing commitment to delivering more meaningful, interactive, and impactful experiences for its customers, talent, and stakeholders worldwide.
KOKI to Showcase Analytical Services and New HF1200 Solder Paste at SMTA Guadalajara 2025
07/31/2025 | KOKIKOKI, a global leader in advanced soldering materials and process optimization services, will exhibit at the SMTA Guadalajara Expo & Tech Forum, taking place September 17 & 18, 2025 at Expo Guadalajara, Salón Jalisco Halls D & E in Guadalajara, Mexico.
Weller Tools Supports Future Talent with Exclusive Donation to SMTA Michigan Student Soldering Competition
07/23/2025 | Weller ToolsWeller Tools, the industry leader in hand soldering solutions, is proud to announce its support of the upcoming SMTA Michigan Expo & Tech Forum by donating a limited-edition 80th Anniversary Black Soldering Set to the event’s student soldering competition.
Koh Young Appoints Tom Hattori as President of Koh Young Japan
07/21/2025 | Koh YoungKoh Young Technology, the global leader in True 3D measurement-based inspection solutions, announced the appointment of Tom Hattori as President of Koh Young Japan (JKY).