-
-
News
News Highlights
- Books
Featured Books
- pcb007 Magazine
Latest Issues
Current IssueThe Hole Truth: Via Integrity in an HDI World
From the drilled hole to registration across multiple sequential lamination cycles, to the quality of your copper plating, via reliability in an HDI world is becoming an ever-greater challenge. This month we look at “The Hole Truth,” from creating the “perfect” via to how you can assure via quality and reliability, the first time, every time.
In Pursuit of Perfection: Defect Reduction
For bare PCB board fabrication, defect reduction is a critical aspect of a company's bottom line profitability. In this issue, we examine how imaging, etching, and plating processes can provide information and insight into reducing defects and increasing yields.
Voices of the Industry
We take the pulse of the PCB industry by sharing insights from leading fabricators and suppliers in this month's issue. We've gathered their thoughts on the new U.S. administration, spending, the war in Ukraine, and their most pressing needs. It’s an eye-opening and enlightening look behind the curtain.
- Articles
- Columns
- Links
- Media kit
||| MENU - pcb007 Magazine
EIPC Technical Snapshot: Supply Chain and Material Price Pressures
April 26, 2021 | Pete Starkey, I-Connect007Estimated reading time: 11 minutes
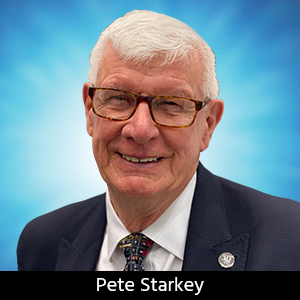
Correction: An earlier headline for this article misstated the name of the organization that presented this webinar. The name of the organization is EIPC, not IPC.
EIPC’s seventh Technical Snapshot webinar on April 14 was timely and appropriate. In the context of current supply chain issues and material price pressures facing the PCB industry, particularly in Europe, the EIPC team brought together an outstanding group of experts—each a leading authority in his field—to analyse and comment upon the areas of concern and to respond to questions raised by a capacity audience.
EIPC president Alun Morgan moderated the session and set the scene with an introductory presentation that examined structural change in the European PCB industry supply base.
His graph of trends in total expenditure on manufactured goods since 1970 indicated that, even in 2019, European and U.S. demand continued to substantially exceed that of China, whereas Chinese manufacturing output had overtaken the U.S. and Europe in the early 2010s. There was now a huge gap between European consumption and European manufacturing output; consequently, the supply chain had become longer and longer.
Looking specifically at world PCB production, it had grown in value from $33.1 billion to $60.8 billion between 2000 and 2019, but the trends in the geographic distribution of manufacturing showed reductions of around two-thirds in North America, Europe, and Japan; and an eight-fold increase in Asia. European PCB industry revenues had fallen from nearly 5 billion euros in 2000 to 1.5 billion in 2020, and the number of manufacturers was currently less than 200.
The numbers of European glass weavers and copper foil suppliers had shown an even more dramatic decline between 2000, when there were four manufacturers of glass fabric and four of copper foil, to a solitary foil manufacturer in 2020 and no-one weaving glass for PCBs. There had been a similar pattern in North America.
Morgan’s list of supply chain risks included travel distance, poor logistics management, too many partners, too much administration, poor understanding of supplier networks, poor communication, tariffs, and political interference. In his opinion, one of the most serious problems was a lack of real demand data and meaningful forecasts, and he implored PCB manufacturers to share their data with suppliers:
- To give them the best opportunity to plan production capacity
- To build resilience into their supply chains
- To ensure that their customers’ needs were communicated effectively and fulfilled at the right time
He acknowledged that manufacturers of substrate materials had to address the fundamental issue of managing complex globalized supply chains.
Having identified poor logistics management as a major supply chain risk, Morgan stressed the crucial importance of recognising logistics as a key part of a commoditised business. It was significant that last year’s EIPC Winter Conference in Rotterdam had included a visit to one of the largest and most advanced container terminals in Europe, Hutchison Ports ECT Delta at the Maasvlakte, handling almost 20 million 20-foot equivalent container units every year, an exceptional example of automated logistics. And it was container logistics expert Dr. Bart Kuipers, senior researcher of port economics, from the Erasmus Centre for Urban Port and Transport Economics at Erasmus University Rotterdam, who gave the second presentation: An overview of the disruption, resilience, and future view of global container shipment resulting from the COVID-19 pandemic.
Kuipers began with the topical example of the unprecedented disruption of the global supply chain caused when the giant container ship EverGiven blocked the Suez Canal—“Very bad timing at a very bad location!” The resulting bottleneck was still causing significant delays to ports, shipping, cargo, and containers.
His real-time illustrations showed the enormous current levels of activity at the ports of Rotterdam and Antwerp where some very big problems were emerging, resulting in serious lengthening of supply chains, not the least due to a shortage of empty containers and a remarkable under-performance of the global container system. Global schedule reliability had been as low as 35% in January 2020. The average length of delays was approaching seven days and this under-performing system had become very expensive—the cost of shipping a 40-foot container from Shanghai to Rotterdam had quadrupled during the last year. This had serious consequences for retailers sourcing lower-price commodities in China, although the carriers were doing very well and making huge profits!
Kuipers discussed the reasons behind the current situation:
- A demand boom: Consumers were buying products instead of services; working at home had increased the demand for computers and fitness equipment.
- A “bullwhip effect” in logistics: This was a consequence of customers failing to share real demand data and meaningful forecast information with their suppliers, causing demand distortion as already highlighted by Morgan.
- Disruption at terminals caused by absenteeism of port workers through COVID, and this had also resulted in a shortage of empty containers.
- The diseconomies of the very big container ships, particularly the congestion of and pressures on handling systems on arrival in port for unloading.
What were the prospects for the future? The short-term reaction of some shippers was to try and bypass the container system, avoiding congestion by shipping to smaller ports, or by using all-rail routes, whereas the reaction of the container-shipping industry was to order more big container ships. Kuiper believed that by the time these new ships were in service the effects of COVID would have been reversed, with consumers buying services instead of products. He expected over-capacity, a lowering of tariffs, and possibly an ending of alliance structures.
He defined two possible longer-term scenarios:
- “Slowbalisation” was characterised by re-shoring and near-sourcing, with a low-growth container industry driven by logistical and geopolitical factors and a decoupling of supply. The traditional container system would stay in place with the container as a mass commodity. There would be a moderate level of innovation in the container industry and the current carrier-centric business structure would remain.
- The likely alternative was “SuperGlobalisation,” in which the container system would become disrupted, with dedicated services for important niche markets. Globalisation would be reinforced by e-commerce, Internet-of-Things, and cloud computing. Autonomous shipping would have a decisive impact in the container market, containers would become individualised and intelligent, and global containerised trade would continue.
Back to PCB materials! Having commented that there was a solitary copper foil manufacturer remaining in Europe, Morgan was proud to introduce that supplier with whom he had enjoyed an excellent relationship during many years of his career in laminate manufacturing—Francois Bottazzi, sales director of Circuit Foil in Luxembourg.Page 1 of 2
Suggested Items
The Evolution of Picosecond Laser Drilling
06/19/2025 | Marcy LaRont, PCB007 MagazineIs it hard to imagine a single laser pulse reduced not only from nanoseconds to picoseconds in its pulse duration, but even to femtoseconds? Well, buckle up because it seems we are there. In this interview, Dr. Stefan Rung, technical director of laser machines at Schmoll Maschinen GmbH, traces the technology trajectory of the laser drill from the CO2 laser to cutting-edge picosecond and hybrid laser drilling systems, highlighting the benefits and limitations of each method, and demonstrating how laser innovations are shaping the future of PCB fabrication.
Day 2: More Cutting-edge Insights at the EIPC Summer Conference
06/18/2025 | Pete Starkey, I-Connect007The European Institute for the PCB Community (EIPC) summer conference took place this year in Edinburgh, Scotland, June 3-4. This is the third of three articles on the conference. The other two cover Day 1’s sessions and the opening keynote speech. Below is a recap of the second day’s sessions.
Day 1: Cutting Edge Insights at the EIPC Summer Conference
06/17/2025 | Pete Starkey, I-Connect007The European Institute for the PCB Community (EIPC) Summer Conference took place this year in Edinburgh, Scotland, June 3-4. This is the second of three articles on the conference. The other two cover the keynote speeches and Day 2 of the technical conference. Below is a recap of the first day’s sessions.
Preventing Surface Prep Defects and Ensuring Reliability
06/10/2025 | Marcy LaRont, PCB007 MagazineIn printed circuit board (PCB) fabrication, surface preparation is a critical process that ensures strong adhesion, reliable plating, and long-term product performance. Without proper surface treatment, manufacturers may encounter defects such as delamination, poor solder mask adhesion, and plating failures. This article examines key surface preparation techniques, common defects resulting from improper processes, and real-world case studies that illustrate best practices.
RF PCB Design Tips and Tricks
05/08/2025 | Cherie Litson, EPTAC MIT CID/CID+There are many great books, videos, and information online about designing PCBs for RF circuits. A few of my favorite RF sources are Hans Rosenberg, Stephen Chavez, and Rick Hartley, but there are many more. These PCB design engineers have a very good perspective on what it takes to take an RF design from schematic concept to PCB layout.