IPC-2581 Revision C: Complete Build Intent for Rigid-Flex
April 30, 2021 | Ed Acheson, Cadence Design SystemsEstimated reading time: 1 minute
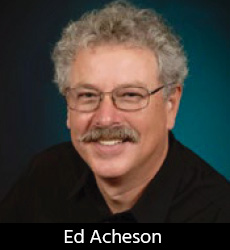
With the current design transfer formats, rigid-flex designers face a hand-off conundrum. You know the situation: My rigid-flex design is done so now it is time to get this built and into the product. Reviewing the documentation reveals that there are tables to define the different stackup definitions used in the design. The cross-references for the different zones to areas of the design are all there, I think. The last time a zone definition was missed, we caused a costly mistake.
Continuing to review the design documents, I verify that the bend locations are defined with information about the radius of the bends with a detail about how the final product looks when all bending is complete, ensuring that the folds are made in the correct order. I hope all information is contained in the documentation, and there will be no calls from the fabricator delaying the product. With all these documents and details left open to interpretation, there must be a way to send this data more intelligently.
Enter IPC-2581 Revision C
There is a way to transfer this data digitally, reducing the need for various forms of drawing details in a document. The new IPC-2581 Revision C format eliminates the need to manually—and painstakingly—create these details in a fabrication drawing. It uses the design data to explicitly define the multiple aspects of a rigid-flex design. How? Let’s look at how some of the details are sent digitally.
First, let’s look at stackup and general board structure. In the design tool, the different stackup details are created, with one or more rigid stackup definitions (8-layer vs. 4-layer, etc.) as well as several flex stackup structures (1 or 2 copper layers, etc.). In my design database a boundary is defined and the stackup data is assigned to those boundaries. This data is then placed into the IPC-2581C format containing the links of each stackup to each boundary association. These are known in IPC-2581 terms as stackup groups assigned to stackup zones. A by-product of these connections is the ability to define the outline profile for each copper and dielectric layer, a key tool for the fabricator.
To read this entire article, which appeared in the March 2021 issue of Design007 Magazine, click here.
Suggested Items
The Evolution of Picosecond Laser Drilling
06/19/2025 | Marcy LaRont, PCB007 MagazineIs it hard to imagine a single laser pulse reduced not only from nanoseconds to picoseconds in its pulse duration, but even to femtoseconds? Well, buckle up because it seems we are there. In this interview, Dr. Stefan Rung, technical director of laser machines at Schmoll Maschinen GmbH, traces the technology trajectory of the laser drill from the CO2 laser to cutting-edge picosecond and hybrid laser drilling systems, highlighting the benefits and limitations of each method, and demonstrating how laser innovations are shaping the future of PCB fabrication.
Day 2: More Cutting-edge Insights at the EIPC Summer Conference
06/18/2025 | Pete Starkey, I-Connect007The European Institute for the PCB Community (EIPC) summer conference took place this year in Edinburgh, Scotland, June 3-4. This is the third of three articles on the conference. The other two cover Day 1’s sessions and the opening keynote speech. Below is a recap of the second day’s sessions.
Day 1: Cutting Edge Insights at the EIPC Summer Conference
06/17/2025 | Pete Starkey, I-Connect007The European Institute for the PCB Community (EIPC) Summer Conference took place this year in Edinburgh, Scotland, June 3-4. This is the second of three articles on the conference. The other two cover the keynote speeches and Day 2 of the technical conference. Below is a recap of the first day’s sessions.
Preventing Surface Prep Defects and Ensuring Reliability
06/10/2025 | Marcy LaRont, PCB007 MagazineIn printed circuit board (PCB) fabrication, surface preparation is a critical process that ensures strong adhesion, reliable plating, and long-term product performance. Without proper surface treatment, manufacturers may encounter defects such as delamination, poor solder mask adhesion, and plating failures. This article examines key surface preparation techniques, common defects resulting from improper processes, and real-world case studies that illustrate best practices.
RF PCB Design Tips and Tricks
05/08/2025 | Cherie Litson, EPTAC MIT CID/CID+There are many great books, videos, and information online about designing PCBs for RF circuits. A few of my favorite RF sources are Hans Rosenberg, Stephen Chavez, and Rick Hartley, but there are many more. These PCB design engineers have a very good perspective on what it takes to take an RF design from schematic concept to PCB layout.