-
- News
- Books
Featured Books
- pcb007 Magazine
Latest Issues
Current IssueVoices of the Industry
We take the pulse of the PCB industry by sharing insights from leading fabricators and suppliers in this month's issue. We've gathered their thoughts on the new U.S. administration, spending, the war in Ukraine, and their most pressing needs. It’s an eye-opening and enlightening look behind the curtain.
The Essential Guide to Surface Finishes
We go back to basics this month with a recount of a little history, and look forward to addressing the many challenges that high density, high frequency, adhesion, SI, and corrosion concerns for harsh environments bring to the fore. We compare and contrast surface finishes by type and application, take a hard look at the many iterations of gold plating, and address palladium as a surface finish.
It's Show Time!
In this month’s issue of PCB007 Magazine we reimagine the possibilities featuring stories all about IPC APEX EXPO 2025—covering what to look forward to, and what you don’t want to miss.
- Articles
- Columns
Search Console
- Links
- Media kit
||| MENU - pcb007 Magazine
Designing With the End in Mind—How the Meaning of DFM Will Transform in the Future
August 23, 2021 | Vince Mazur, AltiumEstimated reading time: 3 minutes
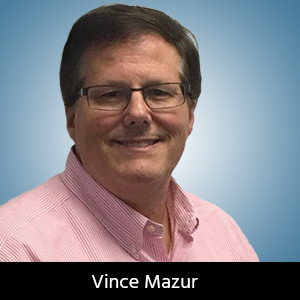
Introduction
The late American educator, author, businessman, and keynote speaker Stephen Covey coined the phrase, "Begin with the end in mind." He said, "To begin with the end in mind means to start with a clear understanding of your destination. It means to know where you’re going so that you better understand where you are now and so that the steps you take are always in the right direction.”
I recall a summer trip when a college buddy and I were on our return trek from the Havasupai campground area near the Grand Canyon. When we were almost to the top, we came across a solo hiker wearing jeans and carrying a camera, tripod, and a small bottle of water; he was about to make the eight-mile trek to Supai, Arizona. We suggested to the ill-prepared hiker to take more water, but the person chose to just continue. My friend and I looked at each other and said, “He’s not going to make it.” I am not sure how things worked out for that hiker, but I think you will agree that he was not prepared and that he certainly did not begin with the end in mind.
Designers of today’s complex printed circuit boards occasionally encounter setbacks due to their lack of early planning. Such consequences for apathy in preparation and awareness will continue to escalate along the growth curve of complexity that the industry continues to experience.
In this article, I will offer a view of how designers can be served by a design for manufacturing (DFM) mindset to help assure first-pass success. I will also provide a glimpse of the potential future of board level design along with a discussion of how the adoption of new and uncharted concepts will assist the journey of electronic product realization that lies ahead.
DFM Fluency is No Longer Optional for PCB Designers
First pass, high yield, cost optimized, and reliable PCB fabrication and assembly is the target objective for PCB designers. Fall short of this outcome, and the consequences can be quite substantial, including derailed new product introduction, sub-par profit margins, unreliable field performance, unnecessary rework, time-consuming redesign, and more. Compound this dynamic with the rapidly escalating complexity of today’s PCBs, and designers find themselves at a crossroads: Either continue the prevailing “wait and see” feedback from manufacturing after committing a project or, with little overhead, proactively and authoritatively evaluate DFM as an inherent part of the designer’s normal incremental PCB design process.
Some Design and Manufacturing Dependencies
As components are placed on a board, the design immediately inherits several design and manufacturing characteristics, such as component spacing and solderability, flying probe access, and more. All these characteristics can influence the fabrication and assembly of the PCB. In addition, the design also inherits characteristics of the parts that are largely outside of the designer’s control. Some of these characteristics include availability, cost, life cycle, performance-to-datasheet, quality, and reliability. All these represent touchpoints of risk that, left unchecked, can derail product realization.
As PCB design progresses, manufacturing characteristics can be inadvertently created, such as acid traps and edge clearances that impact bare board fabrication but may have no impact on assembly. Likewise, without manufacturer-specific DFM checks at design time, boards can be fabricated to specification, yet cannot be assembled due to limitations of the target assembler. Any of these outcomes escalates costs and delays new product introduction. Care must also be taken even when changing existing designs. If not properly revalidated, simply replacing a component can have unintended consequences, and can prevent reliable volume manufacture. This single change can impact an entire assembly run. The resultant cost and time risks can be quite high.
In addition, while not typically associated with traditional DFM, component sourcing is becoming an increasingly significant area designers must pay attention to during the entire design process. If the components cannot be reliably procured, designs cannot be manufactured.
To read this entire article, which appeared in the August 2021 issue of PCB007 Magazine, click here.