Excerpt Chapter 5: 'The Printed Circuit Designer’s Guide to... Thermal Management with Insulated Metal Substrates, Vol. 2'
August 9, 2022 | Didier Mauve and Robert Art, VentecEstimated reading time: 2 minutes
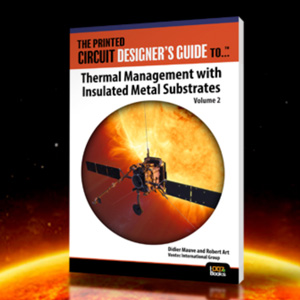
Chapter 5: Boosting Thermal Performance with Multilayer IMS
In The Printed Circuit Designer’s Guide to... Thermal Management with Insulated Metal Substrates (Vol. 1), the authors briefly discussed the issues around combining multiple layers of copper foil, dielectric, and substrate materials and the design opportunities given by the latest generation of thermally conductive thin cores and prepregs.
The latest thermally conductive materials, prepregs, and cores allow designers to reconsider the thermal management approach. They can offer a simple and ready-to-use solution to address thermal issues on existing multilayer boards.
Through necessity, the industry has already come up with many solutions over the years, such as thermal vias, thermal coins, and inserts. All these existing solutions require either the use of thick copper foil and/or the use of heavy copper coins, thus leading to an inevitable inflation in cost and weight. We can now analyze alternative designs made possible by the arrival of multilayered IMS. The following application examples illustrate the concept and the main benefits of multilayered IMS.
Figure 5.1: Single-sided single layer.
The PCB design with insulated metal substrates is by no means limited to single-sided and single-layered circuits (Figure 5.1), although these are predominantly the types of circuits used in LED-lighting and power electronics applications.
There are several versatile ways to take advantage of IMS’s enhanced thermal properties in situations that demand various other attributes such as physical formability or compliance, an intricate shape or small dimensions, or a complex circuit layout that would be fulfilled with a multilayered PCB if it weren’t for the thermal issues.
If a formable grade of laminate (such as, for example, aluminum 5052 with a thin, non-reinforced dielectric) is specified, a single-sided circuit can be post-formed into three-dimensional shapes. This may help to design a circuit board that must fit inside a small or unusually shaped enclosure, or to cram more electronic circuitry within a limited space, or maybe ease assembly of a product if there is only minimal access to install electronic circuit boards. The aluminum layer is machined to reduce its thickness in the bend area.
Figure 5.2: Single-sided double layer.
Also, it is possible to build insulated metal substrates into multilayered IMS structures (Figure 5.2) with thermally conductive laminates and prepregs using plated-through holes for Z-axis interconnection.
In situations where the metal base is not an option, but the component temperature needs to be reduced, an alternative construction may be necessary; the thermal conductive cores and prepreg may be combined to create the entire board or may be used in a hybrid construction combining conventional FR-4 and thermal conductive cores or prepreg.
To continue reading this chapter, download your copy of this book from the I-007eBooks library today!
Suggested Items
The Evolution of Picosecond Laser Drilling
06/19/2025 | Marcy LaRont, PCB007 MagazineIs it hard to imagine a single laser pulse reduced not only from nanoseconds to picoseconds in its pulse duration, but even to femtoseconds? Well, buckle up because it seems we are there. In this interview, Dr. Stefan Rung, technical director of laser machines at Schmoll Maschinen GmbH, traces the technology trajectory of the laser drill from the CO2 laser to cutting-edge picosecond and hybrid laser drilling systems, highlighting the benefits and limitations of each method, and demonstrating how laser innovations are shaping the future of PCB fabrication.
Day 2: More Cutting-edge Insights at the EIPC Summer Conference
06/18/2025 | Pete Starkey, I-Connect007The European Institute for the PCB Community (EIPC) summer conference took place this year in Edinburgh, Scotland, June 3-4. This is the third of three articles on the conference. The other two cover Day 1’s sessions and the opening keynote speech. Below is a recap of the second day’s sessions.
Day 1: Cutting Edge Insights at the EIPC Summer Conference
06/17/2025 | Pete Starkey, I-Connect007The European Institute for the PCB Community (EIPC) Summer Conference took place this year in Edinburgh, Scotland, June 3-4. This is the second of three articles on the conference. The other two cover the keynote speeches and Day 2 of the technical conference. Below is a recap of the first day’s sessions.
Preventing Surface Prep Defects and Ensuring Reliability
06/10/2025 | Marcy LaRont, PCB007 MagazineIn printed circuit board (PCB) fabrication, surface preparation is a critical process that ensures strong adhesion, reliable plating, and long-term product performance. Without proper surface treatment, manufacturers may encounter defects such as delamination, poor solder mask adhesion, and plating failures. This article examines key surface preparation techniques, common defects resulting from improper processes, and real-world case studies that illustrate best practices.
RF PCB Design Tips and Tricks
05/08/2025 | Cherie Litson, EPTAC MIT CID/CID+There are many great books, videos, and information online about designing PCBs for RF circuits. A few of my favorite RF sources are Hans Rosenberg, Stephen Chavez, and Rick Hartley, but there are many more. These PCB design engineers have a very good perspective on what it takes to take an RF design from schematic concept to PCB layout.