Imec’s Nanomesh Electrodes in Pole Position for High-throughput Electrochemical Applications
December 28, 2022 | ImecEstimated reading time: 2 minutes
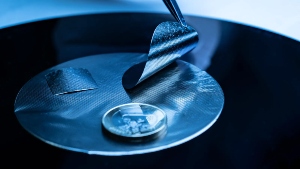
Imec, together with its partner KU Leuven in EnergyVille, announces an important proof point towards implementation of nanomesh structures in high-throughput industrial processes for energy-related applications such as electrolysers, fuel cells and batteries. The researchers have developed a 3D structure made of interconnected nanowires, which can now be used as a freestanding electrode in electrochemical flow cells. The results, published in Materials Today Energy, confirm that the use of these structures can yield a 100-fold increase in current density compared to conventional planar nickel electrodes.
Large-scale production of green hydrogen and green hydrocarbons becomes essential to decarbonize industries. Today, two commercially available options exist for megawatt-scale hydrogen production: classical alkaline water electrolysis (AWE) and proton exchange membrane electrolysis (PEM). However, both technologies face challenges that need to be overcome to further improve the competitiveness of large-scale production of green hydrogen.
Researchers from imec and KU Leuven developed a 3D structure of interconnected nanowires. These nanomesh structures combine high porosity with an extremely high surface area, providing plenty of reaction sites. Due to its unique material properties, nanomesh structures are attractive for numerous electrochemical applications, including electrolysis. They can be created via electroplating, an up-scalable fabrication flow, which makes them cheaper than currently used metal foams.
Until now, non-porous support substrates were needed to provide sufficient mechanical robustness to the highly porous nanomesh. However, to exploit these compelling nano-architectures as freestanding electrodes in electrochemical flow cells, it is essential that the gaseous reagents and products can freely flow in and out. Therefore, the nanowire networks must be supported by a porous structure that is accessible from all sides.
Researchers from imec now published their results on a monolithically integrated nickel nanomesh with an open support grid. This improved nanomesh structure allows gaseous reagents and products to be introduced and removed efficiently from the reaction sites. In an experimental setup they demonstrated that the theoretically available surface area of the nanomesh is almost completely available; resulting in a 100-fold current density increase compared to using conventional planar nickel electrodes. The results confirm that the 3.5 micrometer thin nanomesh electrode has incredible potential in throughput and conversion rates.
"To achieve large-scale production of green hydrogen at offshore wind farms, where space is limited, we need to develop compact electrolysers with high efficiency," said Bart Onsia, business development manager at imec. "These results are a promising step towards the development of new electrolysers components, and we are committed to continuing our research in this area to drive the transition to a more sustainable future."
Philippe Vereecken, imec fellow and part-time professor at KU Leuven: “I am excited that we have been able to further enhance our nanomesh materials and demonstrate their potential in an industry-relevant setup. We have chosen nickel for the current demonstrations for hydrogen production, an area in which we partner with VITO within Hyve, a Belgian consortium that pursues cost-efficient and sustainable hydrogen production on gigawatt scale."
“And the versatility of the nanomesh allows for a much wider portfolio of materials and applications. For instance, we can use copper or silver for CO2 reduction in gas diffusion electrodes," adds Nina Planckensteiner, Marie-Curie post-doctoral researcher at imec. “We are excited to continue exploring the potential of the nanomesh for a wide range of electrochemical applications.”
Suggested Items
I-Connect007 Editor’s Choice: Five Must-Reads for the Week
07/18/2025 | Nolan Johnson, I-Connect007It may be the middle of the summer, but the news doesn’t quit, and there’s plenty to talk about this week, whether you’re talking technical or on a global scale. When I have to choose six items instead of my regular five, you know it’s good. I start by highlighting my interview with Martyn Gaudion on his latest book, share some concerning tariff news, follow that up with some promising (and not-so-promising) investments, and feature a paper from last January’s inaugural Pan-European Design Conference.
Elephantech Launches World’s Smallest-Class Copper Nanofiller
07/17/2025 | ElephantechJapanese deep-tech startup Elephantech has launched its cutting-edge 15 nm class copper nanofiller – the smallest class available globally. This breakthrough makes Elephantech one of the first companies in the world to provide such advanced material for commercial use.
Copper Price Surge Raises Alarms for Electronics
07/15/2025 | Global Electronics Association Advocacy and Government Relations TeamThe copper market is experiencing major turbulence in the wake of U.S. President Donald Trump’s announcement of a 50% tariff on imported copper effective Aug. 1. Recent news reports, including from the New York Times, sent U.S. copper futures soaring to record highs, climbing nearly 13% in a single day as manufacturers braced for supply shocks and surging costs.
I-Connect007 Editor’s Choice: Five Must-Reads for the Week
07/11/2025 | Andy Shaughnessy, Design007 MagazineThis week, we have quite a variety of news items and articles for you. News continues to stream out of Washington, D.C., with tariffs rearing their controversial head again. Because these tariffs are targeted at overseas copper manufacturers, this news has a direct effect on our industry.I-Connect007 Editor’s Choice: Five Must-Reads for the Week
Digital Twin Concept in Copper Electroplating Process Performance
07/11/2025 | Aga Franczak, Robrecht Belis, Elsyca N.V.PCB manufacturing involves transforming a design into a physical board while meeting specific requirements. Understanding these design specifications is crucial, as they directly impact the PCB's fabrication process, performance, and yield rate. One key design specification is copper thieving—the addition of “dummy” pads across the surface that are plated along with the features designed on the outer layers. The purpose of the process is to provide a uniform distribution of copper across the outer layers to make the plating current density and plating in the holes more uniform.