NASA Awards Advance 3D Printing, Quantum Tech for Climate Research
March 17, 2023 | NASAEstimated reading time: 3 minutes
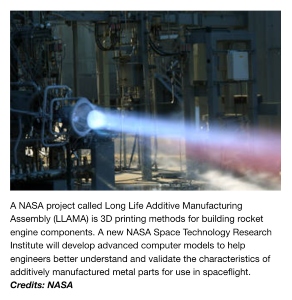
New technology is a key to helping NASA advance its long-term exploration goals for the benefit of all. To support its effort, the agency announced Thursday it will create two new institutes to develop technology in critical areas for engineering and climate research.
Two new Space Technology Research Institutes (STRIs) will leverage teams led by U.S. universities to create multidisciplinary research and technology development programs critical to NASA's future. By bringing together science, engineering, and other disciplines from universities, industry, and non-profits, the institutes aim to impact future aerospace capabilities through investments in early-stage technology.
One of the research institutes will focus on quantum sensing technology in support of climate research. The other will work to improve understanding and help enable rapid certification of metal parts created using advanced manufacturing techniques.
"We're thrilled to draw on the expertise of these multi-university teams to create technology for some of our most pressing needs," said Jim Reuter, associate administrator for the agency’s Space Technology Mission Directorate at NASA Headquarters in Washington. "Their work will enable next-generation science for studying our home planet and broaden the use of 3D-printed metal parts for spaceflight with state-of-the-art modeling."
Each institute will receive up to $15 million over five years.
Quantum Pathways Institute
The University of Texas at Austin will lead the Quantum Pathways Institute, focused on advancing quantum sensing technology for next-generation Earth science applications. Such technology would enable new understanding of our planet and the effects of climate change.
Quantum sensors use quantum physics principles to potentially collect more precise data and enable unprecedented science measurements. These sensors could be particularly useful for satellites in orbit around Earth to collect mass change data – a type of measurement that can tell scientists about how ice, oceans, and land water are moving and changing. Though the basic physics and technology for quantum sensors have been proven in concept, work is required to develop quantum sensors at the precisions necessary for next-generation science needs during spaceflight missions.
"Quantum sensing methods have shown a great deal of promise in computing, communications, and now for Earth science remote sensing applications," said Dr. Srinivas Bettadpur, principal investigator for the institute and professor of aerospace engineering and engineering mechanics at the University of Texas at Austin. "Our intent is to advance this technology and get it ready for space as soon as we can."
The institute will work to further advance the physics underlying quantum sensors, design how these sensors could be built for space missions and understand how mission design and systems engineering would need to adapt to accommodate this new technology.
Partners on the institute include University of Colorado Boulder; University of California, Santa Barbara; California Institute of Technology; and the National Institute of Standards and Technology.
Institute for Model-Based Qualification & Certification of Additive Manufacturing (IMQCAM)
Carnegie Mellon University in Pittsburgh will lead Institute for Model-based Qualification & Certification of Additive Manufacturing (IMQCAM) aiming to improve computer models of 3D-printed – also called additively manufactured – metal parts and expand their utility in spaceflight applications. The institute will be co-led by Johns Hopkins University in Baltimore.
Metal parts 3D-printed are made from powdered metals, which are melted in specific ways and shaped into useful parts. Such parts could be useful for things like rocket engines – giving more flexibility to create new parts when designs change – or as part of a human outpost on the Moon, where bringing pre-fabricated parts would be expensive and limiting. However, efficient certification and use of such parts requires high-accuracy predictions of their characteristics.
"The internal structure of this type of part is much different than what's produced by any other method," said Tony Rollett, principal investigator for the institute and US Steel professor of metallurgical engineering and materials science at Carnegie Mellon University. "The institute will focus on creating the models NASA and others in industry would need to use these parts on a daily basis."
Detailed computer models, known as digital twins, will allow engineers to understand the parts' capabilities and limitations – such as how much stress the parts can take before breaking. Such models will provide the predictability of part properties based on their processing that is key for certifying the parts for use. The institute will develop digital twins for 3D-printed parts made from spaceflight materials that are commonly used for 3D printing, as well as evaluating and modeling new materials.
Somnath Ghosh, the Michael G. Callas professor in civil and systems engineering at Johns Hopkins University’s Whiting School of Engineering, will serve as the co-principal investigator and will co-direct the institute, along with Rollett. Additional partners on the institute include Vanderbilt University, University of Texas at San Antonio, University of Virginia, Case Western Reserve University, Johns Hopkins University Applied Physics Laboratory, Southwest Research Institute, and Pratt & Whitney.
Suggested Items
I-Connect007 Editor’s Choice: Five Must-Reads for the Week
06/27/2025 | Nolan Johnson, I-Connect007While news outside our industry keeps our attention occupied, the big news inside the industry is the rechristening of IPC as the Global Electronics Association. My must-reads begins with Marcy LaRont’s exclusive and informative interview with Dr. John Mitchell, president and CEO of the Global Electronics Association. For designers, have we finally reached the point in time where autorouters will fulfill their potential?
Knocking Down the Bone Pile: Tin Whisker Mitigation in Aerospace Applications, Part 3
06/25/2025 | Nash Bell -- Column: Knocking Down the Bone PileTin whiskers are slender, hair-like metallic growths that can develop on the surface of tin-plated electronic components. Typically measuring a few micrometers in diameter and growing several millimeters in length, they form through an electrochemical process influenced by environmental factors such as temperature variations, mechanical or compressive stress, and the aging of solder alloys.
RTX, the Singapore Economic Development Board Sign MOU Outlining 10-year Growth Roadmap
06/20/2025 | RTXRTX and the Singapore Economic Development Board (EDB) have signed a Memorandum of Understanding (MoU) which outlines a 10-year roadmap to further long-term strategic collaboration in Singapore.
Indra Signs Agreement with AXISCADES to Boost Production of Cutting-Edge Systems in India
06/18/2025 | PRNewswireParis Air Show -- Indra and the Indian technology company AXISCADES have signed an agreement to collaborate on the production of solutions for the aerospace and defense markets.
GKN Aerospace Delivers First High Voltage EWIS System for Clean Aviation’s SWITCH Project
06/16/2025 | GKN AerospaceGKN Aerospace has completed and delivered the first high voltage Electrical Wiring Interconnection System (EWIS) for the Clean Aviation SWITCH project.