Invested in Growth
April 4, 2023 | Barry Matties, I-Connect007Estimated reading time: 3 minutes
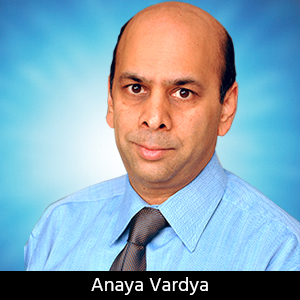
The I-Connect007 team paid a visit to American Standard Circuits in West Chicago, Illinois. While there, we talked at length with CEO Anaya Vardya about the issues on his mind as he pushes technology, expands his floor space, and considers the implications of the CHIPS Act, staffing issues, and what’s happening in China.
Anaya, regarding new technology, is it usually customers who approach you and say, “Can you build this?” Or is your team saying, “Here’s the next technology; we need to be prepared”?
In most cases we are listening to our customers and making our technology investments or driving our technology direction based on that. Our customer base wasn’t big into HDI for many years, but we’ve worked on putting in all the different processes for registration, plating, etc., as opposed to just buying a laser. If you buy the laser, but you don’t have everything else set up, it doesn’t matter. We’ve chosen to subcontract the laser for a long time and we’re ready now to do it ourselves. We found that for some things we’ve been doing, we’ve become noncompetitive, especially from a cycle time standpoint. If we have to go to a laser service three times to build a circuit board, that’s three or four weeks you’ve missed.
When we decided to invest in manufacturing pre-bonded boards on aluminum, we knew that it was a very specialized process to plate those blind vias. We decided to make that investment and purchase sputtering units. We did all that before we had a single customer for it. The Averatek process was the same thing. We made this investment because it makes sense; then we’ll go find the customers.
I would say 80% of our investments from a technology standpoint are driving toward what customers are looking for, or because of quotes we have to no-bid right now.
Are the customers moving to HDI for functionality and/or cost reduction?
It’s functionality for sure. But aerospace defense is always a late adopter. The world has been doing HDI for about 10 years, or even earlier for consumer products. From there, some of it ended up in networking boards, as BGA patterns got very dense. When you have thousand-IO BGAs, you must have a way to fan it out. Then it ended up in microvias. But about five or six years ago, the military started to utilize it also. Now you see more military designs that are acquiring HDI or complex and ultra-complex via structures.
Now, many people say producing HDI costs more money; Happy Holden, who wrote the book on HDI years ago, says it actually saves you money. Where are your thoughts on that?
You must look at it from a value standpoint. It’s like a rigid-flex board. If you look at the flex piece and the rigid piece separately, it’s easy to conclude that the rigid-flex board is obviously more expensive. But you could be saving your money in space and increased reliability because you’re not assembling additional connectors, so you’re gaining real estate on the board. That’s how you save money—by taking advantage of the technology. One has to look at saving money from a total system perspective.
Now you have a regular six-layer panel with microvias. Well, guess what? That six-layer panel with microvias will cost you more money, there’s just no doubt about it. Is it cheaper? It could be, compared to any alternative way to get to the same solution. That’s really the point: HDI is expensive, but what is the cost of the real alternative solution, such as when you must put 40 layers in a board vs. eight? Suddenly, you are saving money. That’s how you answer it. You look at it holistically.
To read this entire article, which appeared in the March 2023 issue of PCB007 Magazine, click here.
Suggested Items
Intervala Hosts Employee Car and Motorcycle Show, Benefit Nonprofits
08/27/2024 | IntervalaIntervala hosted an employee car and motorcycle show, aptly named the Vala-Cruise and it was a roaring success! Employees had the chance to show off their prized wheels, and it was incredible to see the variety and passion on display.
KIC Honored with IPC Recognition for 25 Years of Membership and Contributions to Electronics Manufacturing Industry
06/24/2024 | KICKIC, a renowned pioneer in thermal process and temperature measurement solutions for electronics manufacturing, is proud to announce that it has been recognized by IPC for 25 years of membership and significant contributions to electronics manufacturing.
Boeing Starliner Spacecraft Completes Successful Crewed Docking with International Space Station
06/07/2024 | BoeingNASA astronauts Barry "Butch" Wilmore and Sunita "Suni" Williams successfully docked Boeing's Starliner spacecraft to the International Space Station (ISS), about 26 hours after launching from Cape Canaveral Space Force Station.
KIC’s Miles Moreau to Present Profiling Basics and Best Practices at SMTA Wisconsin Chapter PCBA Profile Workshop
01/25/2024 | KICKIC, a renowned pioneer in thermal process and temperature measurement solutions for electronics manufacturing, announces that Miles Moreau, General Manager, will be a featured speaker at the SMTA Wisconsin Chapter In-Person PCBA Profile Workshop.
The Drive Toward UHDI and Substrates
09/20/2023 | I-Connect007 Editorial TeamPanasonic’s Darren Hitchcock spoke with the I-Connect007 Editorial Team on the complexities of moving toward ultra HDI manufacturing. As we learn in this conversation, the number of shifting constraints relative to traditional PCB fabrication is quite large and can sometimes conflict with each other.