Designing Aerospace PCBs: A Galaxy of Challenges
July 11, 2023 | I-Connect007 Editorial TeamEstimated reading time: 9 minutes
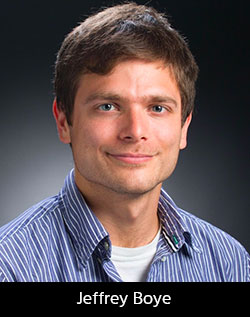
Jeffrey Boye designs aerospace PCBs at the Johns Hopkins University Applied Physics Laboratory. After a decade or so at the APL, some of his boards are currently floating in space. Jeffrey recently took a class with IPC instructor Kris Moyer titled “PCB Design for Military and Aerospace Applications.”
As Jeffrey explains in this interview, this exhaustive class covered everything from high-reliability DFM techniques to Paschen’s curves, which help engineers understand and predict how a high-voltage signal travels in different atmospheres. He also discusses some of the “wacky” projects that he’s worked on at the APL, and the need to communicate with fabricators early on with aerospace applications.
Andy Shaughnessy: Jeffrey, why don’t you start by telling us about your job.
Jeffrey Boye: I’m an engineer at Johns Hopkins University Applied Physics Lab in Laurel, Maryland. I’ve been with the lab for about 10 years, mostly working in civilian aerospace NASA programs. The Parker Solar Probe mission is currently orbiting the sun, and I've got hardware on that. I was the lead hardware designer of the flight computer on the Double Asteroid Redirection Test (DART), the mission that hit the Dimorphos asteroid, and I’m currently working on a vision coprocessor for the Dragonfly mission that's going to autonomously navigate a drone around Saturn's moon Titan later this decade. Not everything I do is milaero; I do some “researchy” stuff too. But those are some of the highlights of my career as a satellite hardware design engineer.
Shaughnessy: How long have you been a PCB designer?
Boye: About a decade. I joke that I never left Johns Hopkins; I went to school here and went straight to work for the APL.
Shaughnessy: That worked out well. So, I understand you took a milaero PCB design class with IPC’s Kris Moyer. Tell us about the class.
Boye: Sure. I design, deliver and test aerospace hardware assemblies. There's a lot of stuff that I knew going in. But coming out of the class, I was surprised that I only knew about half of what I should have known. A couple of things really stick out in my mind. Kris went into great detail over the nitty gritty of base materials selection, which was obscured for me as a designer because it's typically “something the fabricator deals with.”
But Kris helped me get smart on that, because now I feel like I can actually make more intelligent decisions in my stackup by knowing some of the material rules, applicable IPC specs, and how to navigate them, as opposed to just leaning on my fabricator and saying, “What can you do for me?” I can actually engage in those discussions.
Other things that that I found extremely helpful: He had a module or two on coatings, both bonding and conformal coatings. Learning their pros and cons was extremely valuable; in fact, it actually saved me. For a new assembly that I'm helping out with, I knew to ask, “Hey, do you guys need parylene coating?” That triggered a sequence of conversations that resulted in a resounding, “Yes, we actually do need parylene coating. Good catch.” So just knowing the full breadth of options available in that realm is extremely helpful because that was just something that wasn't really rounded out to me.
Below is the last photo of the asteroid Dimorphos, which was rerouted by NASA's DART mission. Jeffrey's electronics were part of the DART mission.
Caption: The last complete image of asteroid moonlet Dimorphos, taken by the DRACO imager on NASA’s DART mission from ~7 miles (12 kilometers) from the asteroid and 2 seconds before impact. The image shows a patch of the asteroid that is 100 feet (31 meters) across. Ecliptic north is toward the bottom of the image. This image is shown as it appears on the DRACO detector and is mirror flipped across the x-axis from reality. Credits: NASA/Johns Hopkins APL
Also, Kris covered high-voltage design, and design considerations for a vacuum and partial pressure. That was extremely useful. I feel very smart now going into meetings and talking about Paschen’s curve, though I may never get the pronunciation correct. This all plays into what I do, especially now that we're talking about the Dragonfly mission to Titan, Saturn’s moon. You know, Titan has an atmosphere thicker than Earth's. It's highly methylated, so you can't use sea level or partial pressure discharge curves and clearance rules like you do here on Earth. You have to go back and basically re-derive them from first principles. But knowing that those design considerations exist, and some of the science behind it, and how to apply it to the engineering set me down the right path.
Shaughnessy: I read over the class syllabus, and it looks like half of the topics relate to DFM in one way or another.
Boye: Yes, especially with high reliability and high volume production. I've learned through the school of hard knocks that it's very easy to design something that can't be built. So, the more you know about DFM rules up front, the better. Kris really opened my eyes to density ratings for different footprints. I'm a digital designer, primarily, and I'm trying to jam as many 0402 components as close as I can to one another, or as close as the library footprint will allow. There are dangers lurking in that, depending on your IPC class and requirements.
Shaughnessy: For those of us who have never heard of Paschen’s curve, tell us about it.
Boye: Paschen’s curve tells you that for a given voltage, what is the distance, at a given pressure, that an arc will start to occur? Usually, on one axis, it’s voltage multiplied by the separation between the two nodes. On the other axis, it's the pressure. So, on the X axis we have the pressure, and the Y axis is the product between the voltage and the distance. They're interesting and fascinating because there's a dip. When you're sitting in a perfect vacuum, or in a full atmosphere like Earth's, you can typically get away with close separation.
However, understanding partial pressure is extremely critical for aerospace applications, because oftentimes you'll have electronics that are switched on as you're transitioning from Earth's atmosphere into space, and the pressure in your vehicle is going to drop slowly. As you transition through those partial pressure points, you can run into arcing concerns, which may or may not be an issue for your given application. But that was extremely eye-opening.
Sometimes you have high-voltage telecommunications equipment that needs to remain on so the spacecraft can communicate with the earth. Well, it's going up into space, and it can't go silent, just because you're going through partial pressures. Knowing about all of this has already made me a better designer.
Shaughnessy: What are some of the takeaways from this course?
Boye: One big takeaway: When you're doing high-rel aerospace stuff, you always want to use the biggest package you can with the most space, because that applied to pretty much everything. So obviously, that runs counter to density requirements and things like that, but to be able to drive a truck through every capacitor would be a perfect milaero board.
Shaughnessy: I noticed that Kris spends some time talking about charge concentration.
Boye: Yes, that goes into the high-voltage stuff. Another eye-opening thing was learning about design rules for rounding out features when you're dealing with high-voltage electronics. I don't think I've learned so much about high-voltage stuff in one course before. That's extremely critical for aerospace, so that was fun.
Shaughnessy: What were some of the most surprising things you learned in Kris’s class?
Boye: I'd say it was everything that we learned about high voltage and coating materials, because that was something I knew so little about and historically, somebody else was dealing with it. What we do on some instruments here at JHUAPL is extremely high voltage and very low current—it’s milliamps, just really low. But for the Dragonfly mission to Titan, we have a very challenging design problem in that we have to power these multi-kilowatt motors to fly us around the surface. We can't do that with a standard 28-volt bus, so we’ve bumped up into a triple-digit bus and now things are getting a little tricky. It's very cool.
Shaughnessy: Are you seeing young people coming into the APL as designers or design engineers?
Boye: The trend of young people going into PCB design seems to have just dropped off a cliff. The youngest PCB designer we have at the lab is, I believe, in his late 40s. Every new crop seems to be electrical engineers doing the design and the layout. Even that is starting to dwindle, so it seems like a lot of people are not really getting in hardware anymore.
Shaughnessy: Does the APL get a good chunk of that Johns Hopkins funding?
Boye: I haven't looked at the numbers recently, but I believe we receive almost half of all the funding Hopkins receives. I know the hospital gets a bunch, and the schools get a bunch, but I think we’re close to $2 billion in contracts and grants now.
Shaughnessy: Have you worked on any crazy designs lately—just “out of this world,” so to speak?
Boye: Oh, yeah. I just reviewed a crazy design that someone else in the lab is doing—a flex design. The flex is 36"long, and they're wrapping it around itself and doing a clock spring kind of thing, because they didn't want to use a slip ring for a gimbal. Now, instead, they've got this giant flex board, and the gimbal is just going to expand and contract with the clock spring flex. That's a really cool prototype design. Most of the boards that we design for space are pretty boring, but occasionally, there's just some really wacky stuff coming through.
Shaughnessy: It sounds like you really love your job. What advice would you give PCB designers about aerospace design?
Boye: Nail down your design rules thoroughly. Have pre-meetings with your fabricators and assemblers early and identify those people early on. If you can identify at least two fabricators, talk to both of them early. I'm going through this hell right now in another design, a heritage design, where we inherited a bunch of design rules. If you don’t do the pre-planning, I think that will almost always set you up for failure. Because once you get down that path, and you make some bad assumptions about design rules, materials, and clearances, and you start making the board, you could effectively have to trash the whole thing, or you're getting into serious waiver territory, which is going to make your customer unhappy.
Shaughnessy: Some of these boards are a tad expensive, right? Don’t want any respins with these boards.
Boye: Oh, yeah, they’re incredibly expensive, so you want to get it right the first time. You know, Altium’s Zach Peterson has all these design videos, and he always ends with, “Talk to your fabricator.” Because not doing so is the one thing historically that will screw you the most.
Shaughnessy: This has been really good. Thanks for speaking with me today, Jeffrey. I’ll be following the Dragonfly mission.
Boye: Thank you, Andy.
Suggested Items
FTG Announces Q2 2025 Financial Results
07/09/2025 | Globe NewswireFiran Technology Group Corporation announced financial results for the second quarter 2025. Revenue: Recorded at $48.7 million, a 25.6% increase over Q2 2024.
Moog Announces Acquisition of COTSWORKS
07/07/2025 | BUSINESS WIREMoog Inc., a worldwide designer, manufacturer and systems integrator of high-performance precision motion and fluid controls and control systems, announced the acquisition of COTSWORKS Inc., an aerospace and defense fiber optics transceiver component manufacturer, for a purchase price of $63 million.
S&K Aerospace Awarded Major Contract Under DLA Maritime Acquisition Advancement Program
07/02/2025 | BUSINESS WIRES&K Aerospace, LLC has been awarded a significant contract under the Defense Logistics Agency’s (DLA) Maritime Acquisition Advancement Program, managed by the U.S. Naval Supply Command - Weapon Systems Support (NAVSUP WSS) in Mechanicsburg, PA.
Green Circuits to Exhibit Full-Service Electronics Manufacturing Solutions at 2025 SMD Symposium
07/02/2025 | Green CircuitsGreen Circuits, a full-service Electronics Manufacturing Services (EMS) partner to leading OEMs, is pleased to announce its participation in the 2025 SMD Symposium, taking place August 5-7 at the Von Braun Center in Huntsville, Alabama.
I-Connect007 Editor’s Choice: Five Must-Reads for the Week
06/27/2025 | Nolan Johnson, I-Connect007While news outside our industry keeps our attention occupied, the big news inside the industry is the rechristening of IPC as the Global Electronics Association. My must-reads begins with Marcy LaRont’s exclusive and informative interview with Dr. John Mitchell, president and CEO of the Global Electronics Association. For designers, have we finally reached the point in time where autorouters will fulfill their potential?