-
-
News
News Highlights
- Books
Featured Books
- pcb007 Magazine
Latest Issues
Current IssueThe Hole Truth: Via Integrity in an HDI World
From the drilled hole to registration across multiple sequential lamination cycles, to the quality of your copper plating, via reliability in an HDI world is becoming an ever-greater challenge. This month we look at “The Hole Truth,” from creating the “perfect” via to how you can assure via quality and reliability, the first time, every time.
In Pursuit of Perfection: Defect Reduction
For bare PCB board fabrication, defect reduction is a critical aspect of a company's bottom line profitability. In this issue, we examine how imaging, etching, and plating processes can provide information and insight into reducing defects and increasing yields.
Voices of the Industry
We take the pulse of the PCB industry by sharing insights from leading fabricators and suppliers in this month's issue. We've gathered their thoughts on the new U.S. administration, spending, the war in Ukraine, and their most pressing needs. It’s an eye-opening and enlightening look behind the curtain.
- Articles
- Columns
- Links
- Media kit
||| MENU - pcb007 Magazine
A Conversation (and Day) with Joe Fjelstad, Part 1
May 3, 2015 | Barry Matties, I-Connect007Estimated reading time: 7 minutes
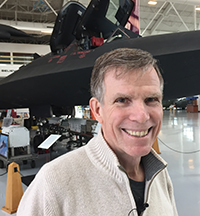
Joe Fjelstad spent a day with me recently as we toured the Evergreen Aviation & Space Museum (home of the Spruce Goose), located in the Oregon community of McMinnville. Our conversation ebbed and flowed between a wide variety of topics, from the electronics industry, to political shenanigans and the “war against failure.” In Part 1 of this multi-part series, Fjelstad introduces his “war against failure” idea, and what went terribly wrong in the advent of lead-free manufacturing.
Barry Matties: Joe, you’ve mentioned to me recently that you are changing your approach to the world—that your message is different. You said, “the war is against failure.” What do you mean by that?
Joe Fjelstad: Ah yes, the war on failure. It is a recent epiphany of mine that failure is the true enemy of electronics. It is the disease, not the symptom, which must be attacked. To date, the industry has largely focused attention on trying to make something reliable using materials and processes that are intrinsically weak. It is a Sisyphean task that will never end. It's like the arcade game Whack-a-Mole. You bang down one problem and a new problem pops up in its place somewhere else.
Much of the challenge and most of the problems are related to solder, which has gotten worse with the introduction of lead-free, a movement that I and others rallied against for several years without success, having seen that the science did not support the claims of the proponents. On the bright side, that failure was what led to the inspiration for manufacturing electronics without solder. That said, I continue to pursue that goal. However, truth be told, I would be perfectly satisfied, and I've said this on more than one occasion publicly, if the only thing that came out of my effort was that the EU reversed the ban on lead in tin-lead solder. A lot of lead has been used in electronics over the last several decades and nobody was ever harmed by it. Well I take that back. An uncounted number of people in Asia and South Asia have been harmed by leaded solder in reclamation activities there. However, that failure and onus rests at the feet of unscrupulous businesspeople in the West, who were shipping electronic waste to those areas without giving people education and training as to what the hell they were doing and what the risks were. It was a case of capitalism gone awry and innocents victimized in the process. Elimination of lead from paint and gasoline were excellent decisions relative to human health; the elimination of lead from solder, except in the case just mentioned, was, at the end of the day, an expensive and wasteful exercise with ongoing expensive ramifications.
Matties: I was listening this morning on the news about the lead-free exemption for the military and they were talking about how that may even disappear. What do you think of that as a possibility?
Fjelstad: I would say that fundamentally it has already disappeared.
Matties: Is that because components just aren't available?
Fjelstad: Yes, and that's the great irony. I made a point of that in my recent talk at the IEEE Aerospace conference in Big Sky, Montana. Here's the scenario: Presently the military is exempt and can use tin lead solder. However, the military transitioned to commercial-off-the-shelf (COTS) parts because it was going to be cheaper to make their electronics. It makes a good deal of sense. In fact, when I worked on the Land Warrior project with Pacific Consultants, we built the entire soldier-of-the-future system out of COTS. Colonel Jette, the Pentagon’s project manager overseeing this whole development made very clear his desire to use COTS. At the time, Pacific Consultants, which consisted of 35 to 40 scientists and engineers, went up against General Dynamics, Raytheon, and Motorola for the contract, and we beat them. The reason we beat them is because we actually made what the Pentagon asked for in its procurement spec. When it came to delivery, the product had the right look and feel as well as performance. In contrast, some of the competitive solutions delivered were quite bizarre. The military industrial complex got that name for a reason. It's because the military is so interwoven with the aerospace and weapons industries.
Anyway, we beat them and built the system completely out of commercial, off-the-shelf hardware. That makes sense to try and control your budgets and we built it with success and within budget, but did not win the production contract. That was given to one of the big boys. Now fast forward to what you have today with lead-free. Who drives the electronics industry? It’s not the military. They had their turn—back in the '60s and '70s; now they're just the caboose at the end of the train.Page 1 of 2
Suggested Items
Driving Innovation: Direct Imaging vs. Conventional Exposure
07/01/2025 | Simon Khesin -- Column: Driving InnovationMy first camera used Kodak film. I even experimented with developing photos in the bathroom, though I usually dropped the film off at a Kodak center and received the prints two weeks later, only to discover that some images were out of focus or poorly framed. Today, every smartphone contains a high-quality camera capable of producing stunning images instantly.
Hands-On Demos Now Available for Apollo Seiko’s EF and AF Selective Soldering Lines
06/30/2025 | Apollo SeikoApollo Seiko, a leading innovator in soldering technology, is excited to spotlight its expanded lineup of EF and AF Series Selective Soldering Systems, now available for live demonstrations in its newly dedicated demo room.
Indium Corporation Expert to Present on Automotive and Industrial Solder Bonding Solutions at Global Electronics Association Workshop
06/26/2025 | IndiumIndium Corporation Principal Engineer, Advanced Materials, Andy Mackie, Ph.D., MSc, will deliver a technical presentation on innovative solder bonding solutions for automotive and industrial applications at the Global Electronics A
Fresh PCB Concepts: Assembly Challenges with Micro Components and Standard Solder Mask Practices
06/26/2025 | Team NCAB -- Column: Fresh PCB ConceptsMicro components have redefined what is possible in PCB design. With package sizes like 01005 and 0201 becoming more common in high-density layouts, designers are now expected to pack more performance into smaller spaces than ever before. While these advancements support miniaturization and functionality, they introduce new assembly challenges, particularly with traditional solder mask and legend application processes.
Knocking Down the Bone Pile: Tin Whisker Mitigation in Aerospace Applications, Part 3
06/25/2025 | Nash Bell -- Column: Knocking Down the Bone PileTin whiskers are slender, hair-like metallic growths that can develop on the surface of tin-plated electronic components. Typically measuring a few micrometers in diameter and growing several millimeters in length, they form through an electrochemical process influenced by environmental factors such as temperature variations, mechanical or compressive stress, and the aging of solder alloys.