-
-
News
News Highlights
- Books
Featured Books
- pcb007 Magazine
Latest Issues
Current IssueThe Hole Truth: Via Integrity in an HDI World
From the drilled hole to registration across multiple sequential lamination cycles, to the quality of your copper plating, via reliability in an HDI world is becoming an ever-greater challenge. This month we look at “The Hole Truth,” from creating the “perfect” via to how you can assure via quality and reliability, the first time, every time.
In Pursuit of Perfection: Defect Reduction
For bare PCB board fabrication, defect reduction is a critical aspect of a company's bottom line profitability. In this issue, we examine how imaging, etching, and plating processes can provide information and insight into reducing defects and increasing yields.
Voices of the Industry
We take the pulse of the PCB industry by sharing insights from leading fabricators and suppliers in this month's issue. We've gathered their thoughts on the new U.S. administration, spending, the war in Ukraine, and their most pressing needs. It’s an eye-opening and enlightening look behind the curtain.
- Articles
- Columns
- Links
- Media kit
||| MENU - pcb007 Magazine
Testing Flexible Circuits, Part 2: Raw Materials and Components
October 1, 2015 | Dave Becker, All FlexEstimated reading time: 4 minutes
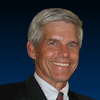
In this second part of a three-part series regarding testing flexible circuits, I will cover the testing of raw materials or components. The following are the common materials that go into a non-populated flex circuit:
- Copper foil
- Dielectric substrate
- Copper/dielectric laminate
- Dielectric insulators
For each of the above, there are several variations:
- Copper foil can be in different thicknesses and can be rolled annealed (RA), electro-deposited (ED) or high ductility electro-deposited (HDED). The copper surface can also come with different treatments. The variety of treatments often impart a different color to the foil. The treatments are generally used as ways to enhance bonding in subsequent lamination cycles.
- Dielectric substrates can also come in different thicknesses and compositions. Polyimide is by far the most popular film used to produce flex circuits. One of the most widely known polyimide film is DuPont’s Kapton®. Polyester, liquid crystal polymer, and PTFE (Teflon®) are also used in some specialty applications.
- Copper/dielectric laminate constructions come in many variations, as a result of combining the different copper foils with dielectrics. They also come with different adhesives that bond them together, including several adhesiveless systems. Films commonly range between .0005” and .005” in thickness. The most frequently used film is .001” thick, but as requirements vary, so will the film thickness.
- Dielectric insulators for cover films and solder masks also come in multiple thicknesses as well as material types. This would also include printable and photoimageable solder masks, which come in both film and liquid form.
In addition to raw materials, there are many consumable process materials used in the fabrication of a flexible circuit. These would include etchant chemistries, plating solutions, plating metals, resist material, developing solutions, press films and much more. These have test requirements as well, but are not specified in applicable IPC documentation.
There are two basic reasons for tests and specifications of raw materials:
1. To assure that the final flexible circuit product will meet the end user requirements.
2. To assure consistency of properties so the material can be processed with maximum efficiency. An example of a property that may make a difference to the circuit fabricator, but not to the end user, is etch-shrink of the laminate. Laminates used for flexible circuits tend to undergo small dimensional changes while being processed. This change is acceptable provided that they are consistent from lot-to-lot (predictable) and small enough so as to not adversely affect layer-to-layer alignment in multilayer circuits.
The vast majority of raw material test requirements are specified in IPC-6013, IPC-4202, IPC-4203, and IPC-4204. There are more than 24 different tests for materials. In some cases the supplier will certify compliance to a certain specification; in other cases the supplier will provide lot test data. There are also situations where the flexible circuit manufacturer will do its own incoming testing.
The following are some of the common test requirements for materials:
- Electrical Properties
- Dielectric constant
- Surface and volume resistance
- Insulation resistance
- Mechanical Properties
- Peel strength (as received, after solder float, and after temperature cycling)
- Flexural endurance
- Low temperature flexibility
- Dimensional stability
- Solder float
- Initiation tear strength
- Propagation tear strength
- Chemical Properties
- Chemical resistance
- Fungus resistance
- Thermal Properties
- Service temperature
- Temperature cycling
- Cosmetic Properties
- Wrinkles, creases, streaks and scratches
- Inclusions
- Voids
- Holes and tears
- Pits and dents
- Other Properties
- Flammability
- Moisture absorption
- Copper foil purity
- Solderability
Other testing is done based on specific customer or industry requirements, for example out-gassing specifications are common for products that need to operate in a vacuum. The automotive industry has some special chemical resistance testing that includes brake fluids, oils and gasoline. Many customers have their own unique requirements in terms of long term temperature aging, maximum service temperature and long term moisture absorption. In general, a flexible circuit supplier will work with customers on unique test requirements and create specifications for materials that are consistent with end use requirements.
Do material properties change after going through a flexible circuit fabrication process? Or is it possible that the raw materials meet the overall requirements, but the combinations and stack-up of materials do not? The answer to both those questions is yes. For example: Two properties that materials are commonly tested for are flexibility and thermal resistance. The ductility of copper can change under heat and pressure. Sometimes platen pressing at elevated temperatures and pressures is used for dielectric bonding. If the temperature and pressure are high enough, the ductility properties can change, although for typical processing parameters, the change is very small. Sometimes a given characteristic improves, such as thermal resistance, after exposure to temperature and pressure. In most cases, the material changes through processing are known and predictable. An experienced flexible circuit manufacturer will have test data to determine where potential issues might arise.
Flex testing done on strips of foil or laminate doesn’t necessarily translate to the final product. In the case of flexibility, the etched trace patterns, surface treatments and material stack-ups can dramatically change flex properties. It is important to test properties in the stack-up and configuration of the final product, just as the customer will perform reliability testing on the finished electronic package containing the flexible circuit.
Even though the raw materials may individually meet certain specifications, it is important to determine if the final product configuration meets those specs. So testing done at the finished circuit level is also needed. Tests specific to the finished circuit will be the topic of our next column on testing.
Dave Becker is vice president of sales and marketing at All Flex Flexible Circuits LLC.
Suggested Items
Driving Innovation: Direct Imaging vs. Conventional Exposure
07/01/2025 | Simon Khesin -- Column: Driving InnovationMy first camera used Kodak film. I even experimented with developing photos in the bathroom, though I usually dropped the film off at a Kodak center and received the prints two weeks later, only to discover that some images were out of focus or poorly framed. Today, every smartphone contains a high-quality camera capable of producing stunning images instantly.
Hands-On Demos Now Available for Apollo Seiko’s EF and AF Selective Soldering Lines
06/30/2025 | Apollo SeikoApollo Seiko, a leading innovator in soldering technology, is excited to spotlight its expanded lineup of EF and AF Series Selective Soldering Systems, now available for live demonstrations in its newly dedicated demo room.
Indium Corporation Expert to Present on Automotive and Industrial Solder Bonding Solutions at Global Electronics Association Workshop
06/26/2025 | IndiumIndium Corporation Principal Engineer, Advanced Materials, Andy Mackie, Ph.D., MSc, will deliver a technical presentation on innovative solder bonding solutions for automotive and industrial applications at the Global Electronics A
Fresh PCB Concepts: Assembly Challenges with Micro Components and Standard Solder Mask Practices
06/26/2025 | Team NCAB -- Column: Fresh PCB ConceptsMicro components have redefined what is possible in PCB design. With package sizes like 01005 and 0201 becoming more common in high-density layouts, designers are now expected to pack more performance into smaller spaces than ever before. While these advancements support miniaturization and functionality, they introduce new assembly challenges, particularly with traditional solder mask and legend application processes.
Knocking Down the Bone Pile: Tin Whisker Mitigation in Aerospace Applications, Part 3
06/25/2025 | Nash Bell -- Column: Knocking Down the Bone PileTin whiskers are slender, hair-like metallic growths that can develop on the surface of tin-plated electronic components. Typically measuring a few micrometers in diameter and growing several millimeters in length, they form through an electrochemical process influenced by environmental factors such as temperature variations, mechanical or compressive stress, and the aging of solder alloys.