Mr. Laminate Tells All: Who Would Like a Mil-Spec Audit?
January 5, 2016 | Doug Sober, Essex Technologies GroupEstimated reading time: 4 minutes
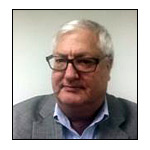
When the electronics industry transitioned from the military standards MIL-P-55110 and MIL-S-13949 to industry standards IPC-6012 and IPC-4101 respectively, there was great rejoicing in Whoville. No longer would we see the likes of George Smith, Ivan Jones, Dave Corbett or Lowell Sherman lurking at our manufacturing doors (all good guys and personable too, but with a horrible mission statement). We would no longer be testing the same properties at the same test frequency, even though there had not been a failing result in three years. No more scrapping prepreg every 400 yards for no real reason other than that was the requirement. No more mountains of test reports to be compiled for verification of performance analysis on a monthly, quarterly and yearly basis. No more fungus resistance testing. Put away the dicy crystal microscope. We were free at last—free at last.
I remember when IPC-4101 was completed and released in December 1997 and the question came up “should IPC create a policeman program to enforce it?” To a person that helped create IPC-4101, absolutely no one wanted such an audit program ever again. Including me and the IPC staff liaisons. Maybe we should have rethought that position.
Now, 18 years later, we realize that the military audits did a number of positive things for the industry. Long before there was ISO 9000, a milspec inspection was the first thing that a new factory would conduct when it opened its doors or a new product was being introduced. The military inspection included a review of the analytical and conformance test procedures, the sampling instructions, as well as any other written documents. The inspector wanted to see how non-conforming materials were isolated, re-tested and labeled. Traceability from raw materials to final lot numbers were verified. Once satisfied the product or facility was put on a QML or QPL by DSCC.
There was also a list of qualification tests that were required for a new product to be listed under MIL-S-13949. Under IPC-4101, the same list of qualification tests were required. The test results were to be available for review by any customer that made a request. However I would guess that very few new products have been qualification tested according to IPC-4101.
Page 1 of 2
Suggested Items
Intervala Hosts Employee Car and Motorcycle Show, Benefit Nonprofits
08/27/2024 | IntervalaIntervala hosted an employee car and motorcycle show, aptly named the Vala-Cruise and it was a roaring success! Employees had the chance to show off their prized wheels, and it was incredible to see the variety and passion on display.
KIC Honored with IPC Recognition for 25 Years of Membership and Contributions to Electronics Manufacturing Industry
06/24/2024 | KICKIC, a renowned pioneer in thermal process and temperature measurement solutions for electronics manufacturing, is proud to announce that it has been recognized by IPC for 25 years of membership and significant contributions to electronics manufacturing.
Boeing Starliner Spacecraft Completes Successful Crewed Docking with International Space Station
06/07/2024 | BoeingNASA astronauts Barry "Butch" Wilmore and Sunita "Suni" Williams successfully docked Boeing's Starliner spacecraft to the International Space Station (ISS), about 26 hours after launching from Cape Canaveral Space Force Station.
KIC’s Miles Moreau to Present Profiling Basics and Best Practices at SMTA Wisconsin Chapter PCBA Profile Workshop
01/25/2024 | KICKIC, a renowned pioneer in thermal process and temperature measurement solutions for electronics manufacturing, announces that Miles Moreau, General Manager, will be a featured speaker at the SMTA Wisconsin Chapter In-Person PCBA Profile Workshop.
The Drive Toward UHDI and Substrates
09/20/2023 | I-Connect007 Editorial TeamPanasonic’s Darren Hitchcock spoke with the I-Connect007 Editorial Team on the complexities of moving toward ultra HDI manufacturing. As we learn in this conversation, the number of shifting constraints relative to traditional PCB fabrication is quite large and can sometimes conflict with each other.