Designing With Tighter Tolerances
July 19, 2016 | David Ledger-Thomas, Honeywell AerospaceEstimated reading time: 2 minutes
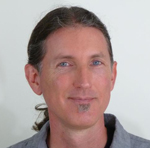
David Ledger-Thomas is a PCB design engineer with Honeywell Aerospace. He’s spent decades designing PCBs for a variety of applications, including defense, aerospace, computers, and high-performance audio. I asked David to share some of his thoughts on designing high-tech boards with increasingly finer spaces, traces and pitch.
Andy Shaughnessy: What are the tightest tolerances you are currently designing?
David Ledger-Thomas: Out of the gate, the assumption for “tight tolerances” is referring to trace and space width. That would be 4.5 mil trace width and 4.5 mil trace spacing. But to add for conversation, tightest tolerance may also reference how much trouble is the PCB fabricator going to have with a particular design (i.e., layer count in a specified thickness, drill size aspect ratio, annular ring, cost, schedule, etc.) while still meeting customer requirements. The PCB design team must also take into account some design parameters such as mechanical/electrical performance, manufacturability, reliability and schedule. So all these could be a part of the “tight tolerance” vocabulary.
Shaughnessy: What are the most challenging issues designers face regarding fine spaces, traces, and pitch?
Ledger-Thomas: Signal integrity would weigh heavy on the application of fine spaces, traces and pitch. Reliability would also be a factor, as in, will the board perform over temperature with a very low mean time between failures (MTBF). And of course can the board be fabricated to required specifications repeatedly and in a timely manner. If a fabricator had to manufacture 20 boards to get one good one, then that would be a poor performer for cost, time and reliability (even though the design was great in the PCB design tool).
Shaughnessy: Does your PCB design tool handle tighter tolerances well? What about PCB design tools in general?
Ledger-Thomas: That’s a somewhat “loaded” question. To answer straight out, yes. Here’s the caveat: Some PCB design tools do handle very tight tolerances well and some do not. So the “right tool for the job” rule applies, i.e., expecting a free/web-based PCB tool to design an HDI board would be rather troublesome. But remember that these are “design tools.” Once the “right tool for the job” is selected, then, as with any other tool, it is the applied knowledge of the user that provides the level of results and quality for the design activity.
Now for the fine print. The PCB tool of choice may have issues with handling data of a tight tolerance board with generating outputs for fabrication/assembly. Meaning the as-designed PCB tool board data is not represented correctly in the fabrication/assembly outputs. Due to rounding issues, the Gerber format/ODB++/data output translation from the PCB tool may not have been correlated as expected. Or there may be other not-so-nice nuances of the PCB tool.
Another point would be the preferred/selected fabricator has not been informed/contacted (or received their feedback) as to the specific tight tolerance implementation. This means that the tight design constraint “as designed/specified” in the PCB tool could cause a resultant of fabrication issues.
To read this entire article, which appeared in the June 2016 issue of The PCB Design Magazine, click here.
Suggested Items
TT Electronics Secures Multi-Million-Pound Defense Contract with Ultra PCS
07/18/2025 | TT ElectronicsTT Electronics, a leading provider of global manufacturing solutions and engineered technologies, announced that it has been awarded a significant new contract with long-standing customer Ultra PCS Ltd (Ultra Precision Control Systems).
NEOTech’s Agave 1 Facility Earns AS9100 Certification for Commercial Aerospace Manufacturing Excellence
07/17/2025 | NEOTechNEOTech, a premier provider of electronic manufacturing services (EMS), integrated design engineering, and advanced supply chain solutions for the aerospace and defense, medical device, and high-tech industrial markets, proudly announces that its Agave 1 manufacturing facility in Juarez, Mexico has officially received AS9100 certification.
Federal Electronics Invests in HydroJet Inline Cleaning Technology at Hermosillo Facility
07/15/2025 | Federal ElectronicsFederal Electronics, a leader in providing advanced electronic manufacturing services, has strengthened the advanced cleaning capabilities of its Hermosillo, Mexico facility with the recent installation of a HydroJet Inline Cleaner from Austin American Technology (AAT).
FTG Announces Q2 2025 Financial Results
07/09/2025 | Globe NewswireFiran Technology Group Corporation announced financial results for the second quarter 2025. Revenue: Recorded at $48.7 million, a 25.6% increase over Q2 2024.
Moog Announces Acquisition of COTSWORKS
07/07/2025 | BUSINESS WIREMoog Inc., a worldwide designer, manufacturer and systems integrator of high-performance precision motion and fluid controls and control systems, announced the acquisition of COTSWORKS Inc., an aerospace and defense fiber optics transceiver component manufacturer, for a purchase price of $63 million.