-
-
News
News Highlights
- Books
Featured Books
- pcb007 Magazine
Latest Issues
Current IssueThe Hole Truth: Via Integrity in an HDI World
From the drilled hole to registration across multiple sequential lamination cycles, to the quality of your copper plating, via reliability in an HDI world is becoming an ever-greater challenge. This month we look at “The Hole Truth,” from creating the “perfect” via to how you can assure via quality and reliability, the first time, every time.
In Pursuit of Perfection: Defect Reduction
For bare PCB board fabrication, defect reduction is a critical aspect of a company's bottom line profitability. In this issue, we examine how imaging, etching, and plating processes can provide information and insight into reducing defects and increasing yields.
Voices of the Industry
We take the pulse of the PCB industry by sharing insights from leading fabricators and suppliers in this month's issue. We've gathered their thoughts on the new U.S. administration, spending, the war in Ukraine, and their most pressing needs. It’s an eye-opening and enlightening look behind the curtain.
- Articles
- Columns
- Links
- Media kit
||| MENU - pcb007 Magazine
Standard of Excellence: Communication Breeds Success
August 29, 2016 | Anaya Vardya, American Standard CircuitsEstimated reading time: 3 minutes
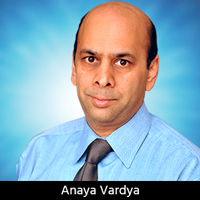
We all need to talk to one another. You need to work closely with your customers.
An open, collaborative, and cooperative partnership will lead to both your company’s success, and the success of your customers.
Now more than ever, the communications between the people using boards and those building boards has never been more important. The demands from our customers for the highest quality and technology PCBs ever built have never been more stringent. The requests range from lines and spaces sometimes as low as two mils, hole aspect ratios that we could only imagine a few years ago, special CTE, high-speed/low-loss materials, and special thermal management requirements. The process of building today’s technology PCBs has become more of a science than ever.
We can look back with fondness when many boards had unique designs, from daughter cards to mother boards to IBM’s famous little paddle cards, to large back panels, all of which had more or less the same configurations even though the requirement for these PCBs came from various customers.
How many of us stared in wonder at the sight of our computer boards with 5-mil lines and spaces, wondering how things would ever get tighter?
Then there were the lead times. Remember when a two-week turn was so rare and unusual that it demanded a paid premium as opposed the standard eight-week lead times? Heck, remember when polyimide was considered an exotic material?
Now, everything has changed, especially when dealing with companies who are building products of the future—super medical electronics, private space exploration, electric cars and printable and wearable electronics.
Frequently, these companies are relying on us to do their R&D and more often than not we are talking about boards that have never been built before, which means that no one even really knows if they can be built.
And there is one more challenge in this new world order: new, freshly minted designers and engineers who have never been in a board shop. Up to a few years ago most OEMs had their own board shops so that their people understood boards. Designers and operations people worked in the same building sharing their experiences and knowledge of designing boards that could be manufactured. Now the in-house board shops, for the most part, are gone, and so are the people who used to work in them; so are the designers who had a good understanding of the board process and how the way the board was designed and laid out could affect that process.
Now we have lost of all that. In most instances, these designers have never been in a board shop and have no understanding on how to design a board the will have maximum produceability. That’s the bad news. But here is the good news, these new designers are hungry for information. They want to know how a board is built, they want to understand the PCB process, and this is a good thing. This is something those of us in the board business may want to take advantage of.
Here are my suggestions:
- Get to know your customers, especially the designers and new product engineers.
- Develop a good understanding of their products and what they are trying to achieve with their products.
- Offer them all of the information they want: plant tours, classes on how a board is built, DFM tools, impedance calculators, assistance on material selection, books, articles, seminars, webinars, lunch-and-learns.
In short, whatever tools you can provide to educate your customers about how a board is built will lead to not only more robust designs, but better boards as well. This type of cooperative and collaborative partnership will in the end help your customers produce better products—products that will help them to be successful.
I encourage everyone in the board business to work with your customers. Invite them into your shops, visit their companies, check out their lines and see how your boards are being processed, from the very first step in the receiving department, through incoming inspection and assembly, to the final product. Doing this will make you a truly outstanding PCB supplier and fabricator.
Anaya Vardya is CEO of American Standard Circuits, Inc.
Suggested Items
Intervala Hosts Employee Car and Motorcycle Show, Benefit Nonprofits
08/27/2024 | IntervalaIntervala hosted an employee car and motorcycle show, aptly named the Vala-Cruise and it was a roaring success! Employees had the chance to show off their prized wheels, and it was incredible to see the variety and passion on display.
KIC Honored with IPC Recognition for 25 Years of Membership and Contributions to Electronics Manufacturing Industry
06/24/2024 | KICKIC, a renowned pioneer in thermal process and temperature measurement solutions for electronics manufacturing, is proud to announce that it has been recognized by IPC for 25 years of membership and significant contributions to electronics manufacturing.
Boeing Starliner Spacecraft Completes Successful Crewed Docking with International Space Station
06/07/2024 | BoeingNASA astronauts Barry "Butch" Wilmore and Sunita "Suni" Williams successfully docked Boeing's Starliner spacecraft to the International Space Station (ISS), about 26 hours after launching from Cape Canaveral Space Force Station.
KIC’s Miles Moreau to Present Profiling Basics and Best Practices at SMTA Wisconsin Chapter PCBA Profile Workshop
01/25/2024 | KICKIC, a renowned pioneer in thermal process and temperature measurement solutions for electronics manufacturing, announces that Miles Moreau, General Manager, will be a featured speaker at the SMTA Wisconsin Chapter In-Person PCBA Profile Workshop.
The Drive Toward UHDI and Substrates
09/20/2023 | I-Connect007 Editorial TeamPanasonic’s Darren Hitchcock spoke with the I-Connect007 Editorial Team on the complexities of moving toward ultra HDI manufacturing. As we learn in this conversation, the number of shifting constraints relative to traditional PCB fabrication is quite large and can sometimes conflict with each other.