-
- News
- Books
Featured Books
- pcb007 Magazine
Latest Issues
Current IssueInventing the Future with SEL
Two years after launching its state-of-the-art PCB facility, SEL shares lessons in vision, execution, and innovation, plus insights from industry icons and technology leaders shaping the future of PCB fabrication.
Sales: From Pitch to PO
From the first cold call to finally receiving that first purchase order, the July PCB007 Magazine breaks down some critical parts of the sales stack. To up your sales game, read on!
The Hole Truth: Via Integrity in an HDI World
From the drilled hole to registration across multiple sequential lamination cycles, to the quality of your copper plating, via reliability in an HDI world is becoming an ever-greater challenge. This month we look at “The Hole Truth,” from creating the “perfect” via to how you can assure via quality and reliability, the first time, every time.
- Articles
- Columns
- Links
- Media kit
||| MENU - pcb007 Magazine
EIPC Reliability Workshop, Tamworth, UK, September 22, 2016
October 3, 2016 | Pete Starkey, I-Connect007Estimated reading time: 17 minutes
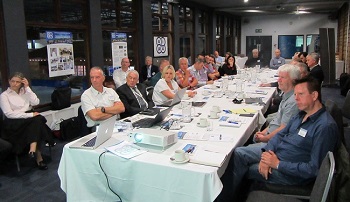
EIPC’s reliability workshop, presented in cooperation with Amphenol Invotec, attracted a capacity audience from eight countries—some delegates having travelled from as far away as Russia—to take the opportunity to learn first-hand how to meet OEM, ODM and EMS product quality and safety requirements, and to understand how interconnection stress testing techniques could be applied to determine the reliability of multilayer PCBs.
The workshop was introduced and moderated by EIPC technical director Michael Weinhold, and delegates were welcomed by Amphenol Invotec managing director Tim Tatton, who gave a brief history of the company from its foundation in 1978 to its present position as the UK’s largest PCB manufacturer and now, as part of Amphenol, a member of the world’s second largest interconnect company. Amphenol Invotec’s accredited expertise in time critical and technologically complex HDI, flex and flex-rigid PCBs for the defence, aerospace and industrial sectors, in partnership with its counterparts in Amphenol Printed Circuit Board Technology in Nashua, New Hampshire, enabled the capability to offer a full spectrum of interconnect solutions.
Michael Weinhold set the scene for the workshop with an overview of the global market for PCBs, the European landscape and trends in technologies and opportunities for PCB fabricators. He posed the question: Were fabricators and assemblers ready for the future, and were they ready for evolutionary, or possibly revolutionary, change?
It was clear from the geographical distribution of PCB production that the western world manufactured less than 10% of a total value estimated at 60 billion USD: “The action takes place where the money is…” But the development work was still largely done in Europe and USA, where there was continuing growth in medical, automotive and aerospace electronics.
Emerging and evolving technologies—applications requiring thermal management, for example, and PCBs with embedded devices—presented challenges to the fabricator, and trends in component miniaturisation—next generation monolithic ceramic capacitors in 008004 format, for example—presented challenges to the assembler. And reliability became an increasingly non-negotiable demand.
But how to define “reliability” in the context of present-day electronics? “Mean Time Between Failures (MTBF)” related to the days when electronic devices could be repaired, whereas nowadays devices that failed were more likely to be replaced than repaired, and this was generally true for automotive, medical and avionics as well as consumer applications. “Mean Time to Failure” was a more appropriate measure—the length of time a device could be expected to last in operation. And to be able to measure it in advance, with a way of simulating the thermal stresses of assembly and in-service operation, would enable the design and manufacture of better boards.
Emphasising the point that a successful PCB fabricator in today’s marketplace was also a trader, Weinhold’s advice to European fabricators was to understand market trends and the needs of the industry, to build on their strengths in engineering know-how, networking and communication, to sell within the capabilities of themselves and their partners in lower-cost countries, and to measure product functionality and performance. How to control product quality? How to control reliability? How to minimise risk and liability? These would be issues addressed by the workshop.
Although the PCB only accounted for between 4% and 10% of the value of an assembly, and there were many other ways in which a device could fail, interconnection failures could be initiated during assembly processes and subsequent in-service thermal cycling as a consequence of thermal expansion of the substrate material. And complex high density interconnects offered a potentially enormous number of opportunities for failure of via connections.
Interconnection stress testing (IST) was a proven technique for rapidly quantifying the robustness of via connections on even the most complex multilayer PCBs, and Weinhold invited Bill Birch, the originator and world expert, to explain and discuss process control and performance classification using IST test systems.
Well-known for his deadpan humour, Birch apologised in advance for over-running his time allocation, although no apology was necessary—his presentation, and his responses to many questions and comments, were a tribute to the depth of knowledge and analytical insight gained over almost 30 years of developing and refining techniques for interconnection stress testing. Delegates had the opportunity to learn an awful lot about what could go wrong and why, and how it could be detected, with many informative and illuminating illustrations and explanations.
Having originally devised the concept of interconnection stress testing in Digital Equipment Company (DEC) in the early 1990s, as a tool to give a quick and repeatable measure of reliability, Birch founded PWB Interconnect Solutions in 1996 as an independent company to develop and market IST as a standardised test method. Its acceptance in 2000 by IPC for inclusion in the TM-650 manual (2.6.26A) was a major step forward and there were currently more than 190 systems globally deployed and supported. The recently established partnership with UL offered additional scope for future standardisation of IST services, and PWBIS continued to cooperate with the High Density Packaging User Group (HDPUG) on a number of ongoing reliability projects and materials characterisation programmes. It was clear that IST was gaining industry-wide acceptance as a powerful and flexible tool for determining the overall reliability of PCBs. Performance criteria for IST were becoming specified in all sectors of the electronics industry, standardised coupon designs were being introduced, and a major European manufacturer of automotive electronics now required all of its suppliers to use IST to qualify HDI product and to determine the limits of their process capability.
Page 1 of 3
Testimonial
"Advertising in PCB007 Magazine has been a great way to showcase our bare board testers to the right audience. The I-Connect007 team makes the process smooth and professional. We’re proud to be featured in such a trusted publication."
Klaus Koziol - atgSuggested Items
Indium Corporation Promotes Two Leaders in EMEA (Europe, Middle East, and Africa) Markets
08/05/2025 | Indium CorporationWith its commitment to innovation and growth through employee development, Indium Corporation today announced the promotions of Andy Seager to Associate Director, Continental Sales (EMEA), and Karthik Vijay to Senior Technical Manager (EMEA). These advancements reflect their contributions to the company’s continued innovative efforts with customers across Europe, the Middle East, and Africa (EMEA).
MacDermid Alpha Electronics Solutions Unveils Unified Global Website to Deepen Customer, Talent, and Stakeholder Engagement
07/31/2025 | MacDermid Alpha Electronics SolutionsMacDermid Alpha Electronics Solutions, the electronics business of Elements Solutions Inc, today launched macdermidalpha.com - a unified global website built to deepen digital engagement. The launch marks a significant milestone in the business’ ongoing commitment to delivering more meaningful, interactive, and impactful experiences for its customers, talent, and stakeholders worldwide.
KOKI to Showcase Analytical Services and New HF1200 Solder Paste at SMTA Guadalajara 2025
07/31/2025 | KOKIKOKI, a global leader in advanced soldering materials and process optimization services, will exhibit at the SMTA Guadalajara Expo & Tech Forum, taking place September 17 & 18, 2025 at Expo Guadalajara, Salón Jalisco Halls D & E in Guadalajara, Mexico.
Weller Tools Supports Future Talent with Exclusive Donation to SMTA Michigan Student Soldering Competition
07/23/2025 | Weller ToolsWeller Tools, the industry leader in hand soldering solutions, is proud to announce its support of the upcoming SMTA Michigan Expo & Tech Forum by donating a limited-edition 80th Anniversary Black Soldering Set to the event’s student soldering competition.
Koh Young Appoints Tom Hattori as President of Koh Young Japan
07/21/2025 | Koh YoungKoh Young Technology, the global leader in True 3D measurement-based inspection solutions, announced the appointment of Tom Hattori as President of Koh Young Japan (JKY).