Flexible Batteries: Evolving Energy for the 'New' Reality
October 18, 2016 | Wright-Patterson Air Force BaseEstimated reading time: 3 minutes
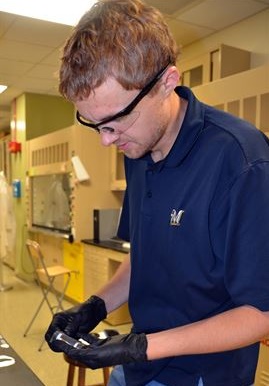
It’s a $7 million research industry today, expected to be worth $400 million dollars by 2025. For researchers at the Air Force Research Laboratory’s Materials and Manufacturing Directorate, the “energy” spent in this research area is worth much more.
By using highly conductive, flexible carbon nanotube mats, scientists here have developed a new type of flexible lithium-ion battery that not only stores energy, but can be folded, bent and manipulated hundreds of times without voltage fluctuations, revolutionizing power sources for the warfighter technology of today.
“It’s time to ‘rethink’ energy,” said Ryan Kohlmeyer, a materials research scientist with UES, Inc. and contractor at AFRL. “There is great interest in flexible electronics. People want to have things like wearable sensors and flexible displays that need power. Traditional lithium-ion batteries, which are hard and rigid, need to evolve to meet the new reality.”
Lithium-ion batteries are common in many home and portable electronics, including computers, mobile phones and wearable fitness trackers. Compared to traditional batteries, lithium-ion batteries charge faster, last longer and have a high energy capacity, enabling them to deliver a large amount of power in a small package.
Given these benefits, lithium-ion batteries provide the perfect platform for powering small sensors and battlefield devices—if the form factor can be changed to meet the application needs.
“If you’re moving around in the field, you don’t want to wear something that is bulky and rigid,” said Kohlmeyer. “Flexible batteries are conformal, meaning that they can move with the person and the device they power. The applications for this type of technology are limitless.”
Traditional lithium-ion batteries consist of a negative electrode, or anode, and a positive electrode, or cathode, coated on a metal foil current collector. Between these electrodes is a thin polymer separator, which keeps the electrodes from touching and allows lithium ions to pass though during charging or discharging.
To fabricate their flexible power source, Kohlmeyer and fellow researcher Aaron Blake, a graduate student at Wright State University, exchanged the commonly used metal foil current collectors for Chemical Vapor Deposition (CVD)-grown carbon nanotube mats. Carbon nanotubes are known to be highly conductive and extremely strong—two features a flexible battery would need in order to generate power in diverse forms.
The researchers prepared the batteries by placing a separator between a carbon nanotube-based anode and cathode that they then encapsulated in a thin, flexible plastic film. The battery was then charged and placed under mechanical testing where it was bent and creased to see if it could perform consistently under extreme mechanical abuse.
The battery’s performance exceeded expectations, maintaining a steady voltage even after more than 288 folds and manipulations. In contrast, a similar device made with traditional metal foil current collectors showed a performance loss with each crease and catastrophic fracture after only 94 folds.
“The voltage of the flexible battery remained steady even when it was flexed or creased hundreds of times. We only started to lose power when the material encapsulating our battery began to allow moisture to get inside the system and degrade the electrolyte and active materials,” said Kohlmehyer. “We believe that our system is way ahead of anything else in this area.”
The research team, led by Dr. Michael F. Durstock and supported by Dr. Les Lee, with funding from the Air Force Office of Scientific Research, has filed a provisional patent related to this system and is excited at the potential to see the technology get into the field.
“Flexible batteries are a natural extension of AFRL’s research in flexible electronics. Our battery can help meet the new power needs for flexible devices. We now know that we can completely deform batteries and still get excellent performance. The implications are enormous,” Kohlmeyer said.
As human performance sensors and flexible device development continues, the flexible battery will be there to meet the power needs of the future.
Suggested Items
Flexible Printed Circuit Board Market to Reach US$40.447 Billion by 2030
07/10/2025 | Globe NewswireThe flexible printed circuit board market will grow at a CAGR of 8.28% to be valued at US$40.447 billion in 2030 from US$27.17 billion in 2025.
Taiwan PCB Industry Adopts Cautious CapEx Strategy, Eyes AI and Southeast Asia for Growth
07/10/2025 | TPCADriven by the stabilization of the global electronics market and the strong demand for AI applications, although the Taiwan printed circuit (PCB) industry is facing a trend of capital expenditure convergence for three consecutive years, its output value and operating performance continue to rise, indicating that the industry is shifting from high investment to high added value development, and the industrial structure is undergoing a steady transformation.
IBIDEN Earns Recognition in FTSE Russell ESG Indexes, Reinforcing Commitment to Sustainable Growth
07/07/2025 | IBIDENIBIDEN Co, Ltd. is pleased to announce that it has been selected for FTSE4Good Index Series for the tenth consecutive year, FTSE Blossom Japan Index for the nineth consecutive year, and FTSE Blossom Japan Sector Relative Index for the fourth consecutive year.
Symposium Review: Qnity, DuPont, and Insulectro Forge Ahead with Advanced Materials
07/02/2025 | Barb Hockaday, I-Connect007In a dynamic and informative Innovation Symposium hosted live and on Zoom on June 25, 2025, representatives from Qnity (formerly DuPont Electronics), DuPont, and Insulectro discussed the evolving landscape of flexible circuit materials. From strategic corporate changes to cutting-edge polymer films, the session offered deep insight into design challenges, reliability, and next-gen solutions shaping the electronics industry.
Flexible Electronics Market to Reach $66.9 Billion by 2032, Growing at a CAGR of 9.2% from 2025
06/30/2025 | PRNewswireThe flexible electronics market is projected to reach $66.9 billion by 2032, up from an estimated $38.4 billion in 2025, growing at a robust CAGR of 9.2% during the forecast period.