-
- News
- Books
Featured Books
- pcb007 Magazine
Latest Issues
Current IssueInventing the Future with SEL
Two years after launching its state-of-the-art PCB facility, SEL shares lessons in vision, execution, and innovation, plus insights from industry icons and technology leaders shaping the future of PCB fabrication.
Sales: From Pitch to PO
From the first cold call to finally receiving that first purchase order, the July PCB007 Magazine breaks down some critical parts of the sales stack. To up your sales game, read on!
The Hole Truth: Via Integrity in an HDI World
From the drilled hole to registration across multiple sequential lamination cycles, to the quality of your copper plating, via reliability in an HDI world is becoming an ever-greater challenge. This month we look at “The Hole Truth,” from creating the “perfect” via to how you can assure via quality and reliability, the first time, every time.
- Articles
- Columns
- Links
- Media kit
||| MENU - pcb007 Magazine
Deep Into Technology at Compunetics
May 24, 2017 | CompuneticsEstimated reading time: 14 minutes
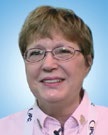
There aren’t many printed circuit companies in my neck of the woods. There is one, however, that has always fascinated me, and that is Compunetics, in Monroeville, Pennsylvania, a suburb of Pittsburgh. Having worked with them on the electrophoretic photoresist, a PPG product, many years ago, it was great to stop by and catch up with CTO Tim Schmitt and Technical Applications Manager Jesse Ward, along with General Manager Burhan Capar, a relative newbie to the company. As always, they are deep into some very interesting technology and always pushing the boundaries of what is possible in that realm.
Patty Goldman: Hello gentlemen. It is great to be here to talk technology and learn what you guys are up to here at Compunetics. How about we start with a little background about yourselves and your roles here.
Burhan Capar: I joined the company as the division manager about eight months ago. I had spent the previous 25 years in the printed circuit board industry with one company, prior to coming here. My charter is to grow this business, which operated as a semi-captive shop for many years. My career in the industry has included running sales, marketing, operations, and I was the president of my former company. This is a great opportunity for me. I am thrilled to be running a company that has this level technology and capabilities. What I am most thrilled with is the opportunity to be working with the most educated and talented group of engineers and scientists in the industry. We know that there is a real need in the PCB industry for a high-end shop with superb engineering and technology.
Jesse Ward: I’ve worked with Compunetics for 10 years and I am the technical applications manager. My background includes project engineering, front-end engineering, sales engineering, and technology development; most recently, I’ve been training in marketing and business development. For the past 10 years, I’ve managed highly technical projects from cradle to grave, including various flex, rigid-flex, HDI, custom requirements, and other aspects of advanced printed circuit boards.
Tim Schmitt: I've been with Compunetics over 30 years. Currently, Compunetics is one division of the larger organization, which is Chorus Call Inc., an ESOP company. The 650 employees of all the divisions have always been and continue to be the largest stockholder of the company. Compunetics has been producing printed circuit boards at this facility continually for the past 47 years. Dr. Giorgio Coraluppi founded the company in 1968 and continues to lead it today.
Dr. Coraluppi leads this organization with one goal for all divisions: maintaining a focus on leading edge technology. With that in mind, we've developed a broad range of technical capabilities. We service pretty much most markets—medical, satellite, military, etc.
Goldman: I’ve known Compunetics for a lot of years, and I’ve been in this shop quite a bit, so I know you do some pretty nifty things, especially with your electrophoretic photoresist, which I worked with. Maybe you can talk about that?
Capar: Our company has an incredible amount of technology, including the electrophoretic photoresist process, which really is an enabling technology. Since my arrival here, we have found new uses for that technology, including a bussing scheme for recessed gold fingers. That is just one of the technologies that we have here. We are one of the few small- to medium-sized printed circuit board fabricators to have a fully automated horizontal electroless plating line. We also have a semi-automated reverse pulse plating line and semi-automated DC plating line. We have a 16-watt laser direct imaging system and a brand new Hakuto cut sheet laminator. The company has the technology and it has the capabilities that most very large companies have. I can confidently say Compunetics has higher technology than any other company of its size.
Every day we run 3-mil lines and spaces. We can do 2-mil lines and spaces using our electrophoretic photoresist. We have a team that is working on 1-mil line and space technology now. Our parent company’s PCBs are generally 18-layer boards so high layer count is common for us. High aspect ratio work is a specialty with a horizontal electroless line and automated reverse pulse plating line. We are very good with flex and rigid-flex, including flex circuits with constantan instead of copper. We also play in the IC package substrate market. We have superb capabilities in the RF/microwave and high-speed digital/SI markets.
Goldman: Some of that is the neat stuff that Tim and I wrote about some years ago. You’ve been doing some interesting technology for many years.
Schmitt: We have developed many technologies and they're on our technical shelf. We have an engineering team that is capable of using these technologies and are constantly developing new technologies. That's the name of the game here, developing new market-driven technologies. We've had very high end customers that required new technologies and required them in a certain time frame, an aggressive time frame. They actually paid our engineers at a cost-plus rate to develop their technologies at our site. Those are the kind of relationships we have with our customers—long-term because we have the engineering expertise they need.
Goldman: Basically, they're partners with you.
Schmitt: They're partners, yes. Partners for the technology that they need now and might need in the future. Based on that, we'll go over some of the technologies from long, long ago, up until today. As you've heard, we have electrophoretic photoresist here. We've had that for at least 15 years. At the time, we installed this we were doing 2-mil lines and spaces with it. Test vehicles were sent out to test centers to determine our yields, etc., and it worked out pretty well. That is a technology that we still have. We were doing 2-mil lines and spaces when nobody really wanted them, because there was no such thing as a microvia, so it was developed before its time.
Page 1 of 3
Testimonial
"Advertising in PCB007 Magazine has been a great way to showcase our bare board testers to the right audience. The I-Connect007 team makes the process smooth and professional. We’re proud to be featured in such a trusted publication."
Klaus Koziol - atgSuggested Items
Indium Corporation Promotes Two Leaders in EMEA (Europe, Middle East, and Africa) Markets
08/05/2025 | Indium CorporationWith its commitment to innovation and growth through employee development, Indium Corporation today announced the promotions of Andy Seager to Associate Director, Continental Sales (EMEA), and Karthik Vijay to Senior Technical Manager (EMEA). These advancements reflect their contributions to the company’s continued innovative efforts with customers across Europe, the Middle East, and Africa (EMEA).
MacDermid Alpha Electronics Solutions Unveils Unified Global Website to Deepen Customer, Talent, and Stakeholder Engagement
07/31/2025 | MacDermid Alpha Electronics SolutionsMacDermid Alpha Electronics Solutions, the electronics business of Elements Solutions Inc, today launched macdermidalpha.com - a unified global website built to deepen digital engagement. The launch marks a significant milestone in the business’ ongoing commitment to delivering more meaningful, interactive, and impactful experiences for its customers, talent, and stakeholders worldwide.
KOKI to Showcase Analytical Services and New HF1200 Solder Paste at SMTA Guadalajara 2025
07/31/2025 | KOKIKOKI, a global leader in advanced soldering materials and process optimization services, will exhibit at the SMTA Guadalajara Expo & Tech Forum, taking place September 17 & 18, 2025 at Expo Guadalajara, Salón Jalisco Halls D & E in Guadalajara, Mexico.
Weller Tools Supports Future Talent with Exclusive Donation to SMTA Michigan Student Soldering Competition
07/23/2025 | Weller ToolsWeller Tools, the industry leader in hand soldering solutions, is proud to announce its support of the upcoming SMTA Michigan Expo & Tech Forum by donating a limited-edition 80th Anniversary Black Soldering Set to the event’s student soldering competition.
Koh Young Appoints Tom Hattori as President of Koh Young Japan
07/21/2025 | Koh YoungKoh Young Technology, the global leader in True 3D measurement-based inspection solutions, announced the appointment of Tom Hattori as President of Koh Young Japan (JKY).