-
- News
- Books
Featured Books
- smt007 Magazine
Latest Issues
Current IssueSupply Chain Strategies
A successful brand is built on strong customer relationships—anchored by a well-orchestrated supply chain at its core. This month, we look at how managing your supply chain directly influences customer perception.
What's Your Sweet Spot?
Are you in a niche that’s growing or shrinking? Is it time to reassess and refocus? We spotlight companies thriving by redefining or reinforcing their niche. What are their insights?
Moving Forward With Confidence
In this issue, we focus on sales and quoting, workforce training, new IPC leadership in the U.S. and Canada, the effects of tariffs, CFX standards, and much more—all designed to provide perspective as you move through the cloud bank of today's shifting economic market.
- Articles
- Columns
- Links
- Media kit
||| MENU - smt007 Magazine
Using Lead-Free BGAs in a Tin/Lead Soldering Process
July 20, 2017 | David Hillman, Rockwell CollinsEstimated reading time: 3 minutes
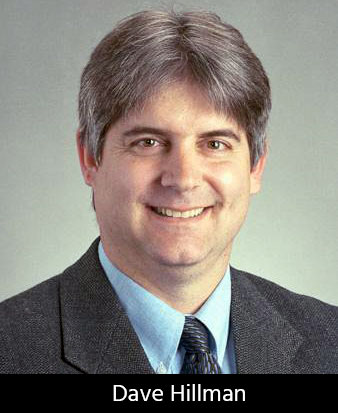
Several electronic market segments remain exempt from lead-free material restrictions such as Restriction of Hazardous Substances (RoHS) legislation. These market segments tend to be electronics used in harsh environments and/or that have life/system critical functionality. While these market segments, which include avionics, can use solder containing lead, it is increasingly difficult to procure advanced components in non-ROHS compliant configurations. Product design teams that continue to use tin/lead soldering processes are faced with the dilemma of how to use ball grid array (BGA) components that are only available with lead-free solder spheres in their assembly processes. This paper discusses several aspects of having lead-free BGA components in a tin/lead soldering process: (1) mixed metallurgy; (2) solidification; (3) tin whiskers. The possible methodologies of utilization without compromising product integrity will be discussed.
The Mixed Metallurgy Concern
Environmental legislation has caused significant impact to the electronic industry in terms of the material sets used in electronic products. The prohibition of materials such as cadmium, hexavalent chromium, mercury and lead has eliminated a number of electronic components and material processes that were historically used in producing electronic products. The removal of lead for solder alloys has arguably the greatest impact on electronic products due to its role as the primary mechanical and electrical functionality material. Figure 1 illustrates how global solder usage trends show the replacement of tin/lead solder alloys with lead-free solder alloys since 2004 as tracked by the IPC Global Solder Statistical Program.
Product design teams that continue to use tin/lead soldering processes are faced with the dilemma of how to use BGA components that are only available with lead-free solder balls. The combination of a tin/lead solder paste alloy with a BGA component with lead-free solder balls results in a “mixed metallurgy” solder joint microstructure that has poor solder joint integrity in many product use environments. Three industry solutions have emerged as acceptable methodologies to address the potential solder joint integrity issue of a mixed metallurgy (i.e., lead-free parts used on a tin/lead assembly, condition). The first solution is to send the lead-free BGA component to an external service provide to be “reballed” (i.e., the lead-free solderballs are removed and replaced with tin/lead alloy solderballs). The reballing process has been shown to be reliable, provided that strictly controlled process procedures are followed. The advantage of a reballed BGA component is that it is transparent to a tin/lead soldering process; the disadvantages are the cost and time required to reball the BGA component.
Figure 1: Global solder usage trends. (IPC Global Solder Statistical Program)
The reballing of a BGA component requires the control of several key process parameters: moisture sensitivity level, solderball removal/attachment temperature/time and cleanliness of the reballed BGA component. Functional component testing is necessary to ensure that no process or component defects result from the reballing process. The following example illustrates how conducting functional assessment due diligence prevents the introduction of defective reballed BGAs into products.
A BGA component was found to have functional errors during engineering prototype testing. The BGA component in question had been procured from the component supplier as a lead-free BGA and was subsequently reballed using a eutectic tin/lead solder alloy. An X-ray of the suspect BGA revealed excessive solder joint voiding.
Figure 2: X-ray image of suspect BGA.
Industry investigations have shown that BGA voiding, in general, is not a solder joint integrity issue but is a clear indicator of a pad design or soldering process problem. The BGA pads did not contain any microvia technology so it was initially believed that an issue relating to a solder paste deposit or reflow profile was the voiding root cause. Figure 2 shows the excessive voiding observed in the BGA solder joints during X-ray assessment.
Metallographic cross-sectional analysis was conducted to verify that the observed solder joint voiding was a solder process issue. The cross-sectional analysis revealed component copper pad thicknesses so thin that, during the assembly reflow process, the molten solderball made contact with the BGA laminate material, which resulted in outgassing that created the void. Measurement of the copper pad plating revealed a nonexistent nickel plating barrier, which allowed 50%–100% copper plating dissolution of the BGA pad.
To read this entire article, which appeared in the July 2017 issue of SMT Magazine, click here.
Testimonial
"Our marketing partnership with I-Connect007 is already delivering. Just a day after our press release went live, we received a direct inquiry about our updated products!"
Rachael Temple - AlltematedSuggested Items
Indium Corporation Promotes Two Leaders in EMEA (Europe, Middle East, and Africa) Markets
08/05/2025 | Indium CorporationWith its commitment to innovation and growth through employee development, Indium Corporation today announced the promotions of Andy Seager to Associate Director, Continental Sales (EMEA), and Karthik Vijay to Senior Technical Manager (EMEA). These advancements reflect their contributions to the company’s continued innovative efforts with customers across Europe, the Middle East, and Africa (EMEA).
MacDermid Alpha Electronics Solutions Unveils Unified Global Website to Deepen Customer, Talent, and Stakeholder Engagement
07/31/2025 | MacDermid Alpha Electronics SolutionsMacDermid Alpha Electronics Solutions, the electronics business of Elements Solutions Inc, today launched macdermidalpha.com - a unified global website built to deepen digital engagement. The launch marks a significant milestone in the business’ ongoing commitment to delivering more meaningful, interactive, and impactful experiences for its customers, talent, and stakeholders worldwide.
KOKI to Showcase Analytical Services and New HF1200 Solder Paste at SMTA Guadalajara 2025
07/31/2025 | KOKIKOKI, a global leader in advanced soldering materials and process optimization services, will exhibit at the SMTA Guadalajara Expo & Tech Forum, taking place September 17 & 18, 2025 at Expo Guadalajara, Salón Jalisco Halls D & E in Guadalajara, Mexico.
Weller Tools Supports Future Talent with Exclusive Donation to SMTA Michigan Student Soldering Competition
07/23/2025 | Weller ToolsWeller Tools, the industry leader in hand soldering solutions, is proud to announce its support of the upcoming SMTA Michigan Expo & Tech Forum by donating a limited-edition 80th Anniversary Black Soldering Set to the event’s student soldering competition.
Koh Young Appoints Tom Hattori as President of Koh Young Japan
07/21/2025 | Koh YoungKoh Young Technology, the global leader in True 3D measurement-based inspection solutions, announced the appointment of Tom Hattori as President of Koh Young Japan (JKY).