-
- News
- Books
Featured Books
- pcb007 Magazine
Latest Issues
Current IssueSales: From Pitch to PO
From the first cold call to finally receiving that first purchase order, the July PCB007 Magazine breaks down some critical parts of the sales stack. To up your sales game, read on!
The Hole Truth: Via Integrity in an HDI World
From the drilled hole to registration across multiple sequential lamination cycles, to the quality of your copper plating, via reliability in an HDI world is becoming an ever-greater challenge. This month we look at “The Hole Truth,” from creating the “perfect” via to how you can assure via quality and reliability, the first time, every time.
In Pursuit of Perfection: Defect Reduction
For bare PCB board fabrication, defect reduction is a critical aspect of a company's bottom line profitability. In this issue, we examine how imaging, etching, and plating processes can provide information and insight into reducing defects and increasing yields.
- Articles
- Columns
- Links
- Media kit
||| MENU - pcb007 Magazine
Estimated reading time: 1 minute
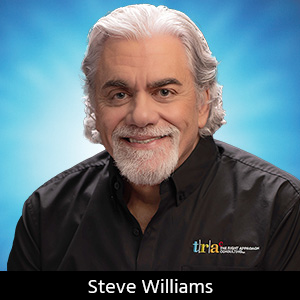
The Right Approach: Navigating Process Change? TPC is the Key
Introduction
Change is a given. While this adage may be quite true and normally a good thing, it can wreak process engineering havoc in a printed circuit operation. Change is good, but the operative word is controlled change relative to the complex processes involved in manufacturing a printed circuit board. The key to successfully navigating process change is to develop a robust Temporary Process Change (TPC) program.
Process Engineering: 75% Science, 20% Black Magic and 5% Luck
My process engineer friends will certainly take exception to this statement, however, no matter how talented our process gurus are, I believe I could make a compelling argument with them over a couple of beers. It is incontrovertible that two plus two will always equal four, no matter who is doing the math. If printed circuit process engineering was 100% science, then what works in one shop would work just as well in every other shop, period. We all know that is about as true as the statement that “politicians never lie.” That is why it is so important, once the process recipe has been engineered to be highly repeatable, to have a controlled method to continue to tweak and improve it.
Even in the most controlled manufacturing environment, internal audits, rework and yield issues can oftentimes be traced back to an unauthorized minor process change. Changing a bath temperature or time, skipping a traveler step, or changing the supplier for a consumable may seem like a good idea at the time—until everyone is scratching their heads over a spike in scrap. Operators, leads and supervisors have their hearts in the right place when they want to try an idea to improve a process. More times than not they simply lack experience with the DoE (design of experiment) or other controlled change methodology.
To read the full version of this article which appeared in the September 2017 issue of The PCB Magazine, click here.
More Columns from The Right Approach
The Right Approach: ‘Twas the Night Before Christmas (Harley-style)The Right Approach: I Hear the Train A Comin'
The Right Approach: Culture Change is Key to a QMS
The Right Approach: Leadership 101—Be a Heretic, Not a Sheep
The Right Approach: Leadership 101—The Law of Legacy
The Right Approach: Leadership 101: The Law of Explosive Growth
The Right Approach: Leadership 101—The Law of Timing
The Right Approach: The Law of Sacrifice