Georgia Tech Researchers Support DARPA’s New 'CHIPS' Initiative
October 5, 2017 | Georgia TechEstimated reading time: 4 minutes
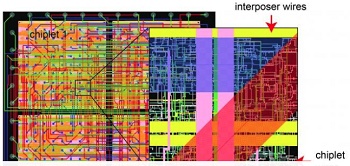
A team of Georgia Tech researchers is bringing electronic design software and communications expertise to DARPA's new CHIPS initiative, which will enable future generations of integrated circuits to be assembled from plug-and-play modules known as “chiplets.” Reusing blocks of existing microelectronics technology could reduce the need to design complex monolithic chips from scratch for new applications.
By allowing components such as memory modules or signal processors to be easily fitted together like the parts of a jigsaw puzzle, the initiative could help reduce the cost of new ICs for Department of Defense (DoD) agencies and accelerate the application of new technology. While the initiative is driven by DoD needs for its ships, tanks and aircraft, innovations developed by the program could also reduce the cost of developing low-volume specialized devices in the commercial world.
“The goal of this program is to make the design more modular so we can reuse existing components, making the design process much faster, easier and cheaper,” said Sung Kyu Lim, a School of Electrical and Computer Engineering professor who heads up Georgia Tech’s part of the initiative. “We’ll be able to create new chips to meet specific needs by reusing these chiplets and putting them together in modular fashion. The modular design will allow us to pick and choose the components we need for specific applications.”
Monolithic integrated circuits like those that go into smartphones contain billions of transistors. They cost tens to hundreds of millions of dollars and take months to design. Companies selling large volumes of consumer products can afford that design cost, but DoD agencies that need smaller numbers of specialized devices are looking for ways to reduce the design cost and time required.
Enter DARPA’s Common Heterogeneous Integration and Intellectual Property Reuse Strategies (CHIPS) effort, which will use interposer technology – a silicon and copper interface – that will interconnect the chiplets. While the interposer adds a level of complexity to the design of the devices, it’s necessary to facilitate the 3-D modular assembly. The chiplets themselves could arise from existing designs, with engineers modifying memory, signal processing and other blocks from ICs already in production.
“Instead of designing a whole new chip, you can borrow from what’s already been designed to put together a new chip quickly and at lower cost,” said Lim, who holds the Dan Fielder Endowed Chair. The chiplets would be assembled and then packaged together, facilitating shorter interconnect lengths that would reduce communication time and energy consumption between the components. The modular nature of the chiplets would also allow a block to be replaced by new technology without redesigning an entire IC.
The four-year CHIPS effort involves 11 teams, including major defense contractors, microelectronics companies, design firms – and two other universities: the University of Michigan and North Carolina State University. In addition to Lim, the Georgia Tech effort will involve three other faculty members: Pippin Chair Professor Madhavan Swaminathan, Professor Saibal Mukhopadhyay and Assistant Professor Tushar Krishna, all from the School of Electrical and Computer Engineering.
About $3.7 million will come to Georgia Tech as part of the project’s budget. In addition to the faculty members, that will fund a research engineer and up to eight graduate students.
The Georgia Tech team will provide electronic design automation software needed to produce the chiplets, develop translator technology that will allow chiplets operating in different languages to communicate, and evaluate different design standards brought to the project by other teams.
- Circuit design tools will be needed to create the chiplets, many of which will be adapted from existing designs. “A big part of what we’ll deliver for this project is electronic design automation (EDA) tools,” said Lim. “We want to automate the entire chiplet generation and integration process as much as possible using algorithms and software tools.”
- Modules from different companies may use different languages. To use them together in a new system, the chiplets will need translators, circuitry and software that will wrap around each chiplet. “We need to understand all the different languages, so we can help the chiplets communicate with one another,” Lim explained. “The complexity will depend on how many interface protocols are used in the system.”
- The project teams will have to work together using the same design standards. Lim’s team will establish tools and techniques for evaluating the different standards now used by different teams that are part of the overall effort. “We will provide a fair means of comparing the different technology options and picking the winner,” said Lim.
Though DARPA’s focus is on providing technology for DoD users, solutions developed from the initiative could also have broad benefits in the commercial microelectronics world. “Small- and medium-sized companies could will benefit a lot from this,” Lim said. “Small design houses that would like to develop their own ICs will likely be very interested.”
Meeting the program’s ambitious goals will be challenging, Lim says, with reliability, power, mechanical and thermal issues on the horizon. “The success of this program will make a significant contribution to the defense industry and the microelectronics community in general,” he said.
Suggested Items
Trouble in Your Tank: Can You Drill the Perfect Hole?
07/07/2025 | Michael Carano -- Column: Trouble in Your TankIn the movie “Friday Night Lights,” the head football coach (played by Billy Bob Thornton) addresses his high school football team on a hot day in August in West Texas. He asks his players one question: “Can you be perfect?” That is an interesting question, in football and the printed circuit board fabrication world, where being perfect is somewhat elusive. When it comes to mechanical drilling and via formation, can you drill the perfect hole time after time?
The Evolution of Picosecond Laser Drilling
06/19/2025 | Marcy LaRont, PCB007 MagazineIs it hard to imagine a single laser pulse reduced not only from nanoseconds to picoseconds in its pulse duration, but even to femtoseconds? Well, buckle up because it seems we are there. In this interview, Dr. Stefan Rung, technical director of laser machines at Schmoll Maschinen GmbH, traces the technology trajectory of the laser drill from the CO2 laser to cutting-edge picosecond and hybrid laser drilling systems, highlighting the benefits and limitations of each method, and demonstrating how laser innovations are shaping the future of PCB fabrication.
Day 2: More Cutting-edge Insights at the EIPC Summer Conference
06/18/2025 | Pete Starkey, I-Connect007The European Institute for the PCB Community (EIPC) summer conference took place this year in Edinburgh, Scotland, June 3-4. This is the third of three articles on the conference. The other two cover Day 1’s sessions and the opening keynote speech. Below is a recap of the second day’s sessions.
Day 1: Cutting Edge Insights at the EIPC Summer Conference
06/17/2025 | Pete Starkey, I-Connect007The European Institute for the PCB Community (EIPC) Summer Conference took place this year in Edinburgh, Scotland, June 3-4. This is the second of three articles on the conference. The other two cover the keynote speeches and Day 2 of the technical conference. Below is a recap of the first day’s sessions.
Preventing Surface Prep Defects and Ensuring Reliability
06/10/2025 | Marcy LaRont, PCB007 MagazineIn printed circuit board (PCB) fabrication, surface preparation is a critical process that ensures strong adhesion, reliable plating, and long-term product performance. Without proper surface treatment, manufacturers may encounter defects such as delamination, poor solder mask adhesion, and plating failures. This article examines key surface preparation techniques, common defects resulting from improper processes, and real-world case studies that illustrate best practices.