-
- News
- Books
Featured Books
- pcb007 Magazine
Latest Issues
Current IssueInventing the Future with SEL
Two years after launching its state-of-the-art PCB facility, SEL shares lessons in vision, execution, and innovation, plus insights from industry icons and technology leaders shaping the future of PCB fabrication.
Sales: From Pitch to PO
From the first cold call to finally receiving that first purchase order, the July PCB007 Magazine breaks down some critical parts of the sales stack. To up your sales game, read on!
The Hole Truth: Via Integrity in an HDI World
From the drilled hole to registration across multiple sequential lamination cycles, to the quality of your copper plating, via reliability in an HDI world is becoming an ever-greater challenge. This month we look at “The Hole Truth,” from creating the “perfect” via to how you can assure via quality and reliability, the first time, every time.
- Articles
- Columns
- Links
- Media kit
||| MENU - pcb007 Magazine
HDI’s Beneficial Influence on High-Frequency Signal Integrity
October 17, 2017 | Happy Holden, I-Connect007Estimated reading time: 1 minute
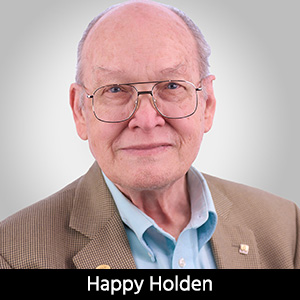
Introducing the Benefits of Microvias
The increasingly widespread use of finepitch ball-grid array (BGA), chip scale packaging (CSP), and other evolving technology form-factors means that new fabrication techniques must be used to create printed circuit boards (PCBs). In addition, extremely fast clock speeds and high signal bandwidths challenge systems designers to find better ways to overcome the negative effects of noise, radio frequency interference (RFI) and electro-magnetic interference (EMI) have on their product’s performance. Finally, increasingly restrictive cost targets are compounding problems associated with today’s smaller, denser, lighter, and faster systems.
Staying competitive and delivering the products people want means seeking out and embracing the best available technologies and design methodologies. The use of PCBs incorporating microvia circuit interconnects is currently one of the most viable solutions on the market (Figure 1). Adopting microvia technology means that products can use the newest, smallest, and fastest devices, meet stringent RFI/ EMI requirements, and keep pace with downward-spiraling cost targets.
What are Microvia Technologies?
Microvias are vias of 6-mils (150 microns) diameter or less. Their most typical use today is in blind and buried vias used to create interconnections through one dielectric layer within a PCB. Microvias are commonly used in blind via constructions where the outer layers of a multilayer PCB are connected to the next adjacent signal layer. Used in all forms of electronic products, they effectively allow for the cost effective fabrication of high-density assemblies.
The IPC has selected high-density interconnection structures (HDIS) as the term to refer to these various microvia technologies. This definition is by no means universal. The Japanese refer to any via drilled by lasers in a thin dielectric as a microvia.
To read the full version of this article which appeared in the October 2017 issue of The PCB Magazine, click here.
Testimonial
"Our marketing partnership with I-Connect007 is already delivering. Just a day after our press release went live, we received a direct inquiry about our updated products!"
Rachael Temple - AlltematedSuggested Items
Flexible Circuit Technologies to Host Free Flex Heater Webinar
08/18/2025 | Flexible Circuit TechnologiesGlobal Supplier of flexible circuits, flex design services, and assembly/box-build services, Flexible Circuit Technology will host their latest webinar, "Thermal Precision Meets Flexibility: The Technology Behind Heater Circuits" on Tuesday, August 26th, 2025 at 11 AM EDT.
A.R.T. Ltd. Nominated in Four Categories at 2025 Instrumentation and Electronics Industry Awards
08/11/2025 | A.R.T. Ltd.Advanced Rework Technology Ltd. (A.R.T. Ltd.), a leading provider of electronics training and consultancy, has been shortlisted in four categories at the 2025 Instrumentation and Electronics Industry Awards, including Industry Personality, Academic Support, Rising Star, and Best Customer Service.
EMC Taiwan Receives IPC-4101 Qualified Products Listing Certification
08/08/2025 | Global Electronics AssociationIPC’s Validation Services Program has awarded an IPC-4101 Qualified Products Listing (QPL) to Elite Materials Co. (EMC), an electronics base material manufacturing company headquartered in Taoyuan City, Taiwan.
Global Excellence in PCB Design: The Global Electronics Association Expands to Italy
08/07/2025 | Global Electronics AssociationIn today's rapidly evolving electronics industry, printed circuit boards (PCBs) serve as the critical backbone influencing the success, reliability, and time-to-market of countless products. Recognizing this essential role, the Global Electronics Association (formerly IPC), a worldwide leader in electronics standards, certification, and education, is now expanding its internationally acclaimed PCB design training to Italy.
Dana on Data: Best Practices in Interpreting Drawing Notes—‘Use Latest Revision’
08/07/2025 | Dana Korf -- Column: Dana on DataThe global nature of electronics manufacturing requires clear, consistent, and precise communication, particularly in technical documentation. An area where miscommunication often arises is in interpreting drawing notes—small lines of text with the potential to dramatically impact product quality, manufacturing efficiency, and customer satisfaction.