-
- News
- Books
Featured Books
- pcb007 Magazine
Latest Issues
Current IssueInventing the Future with SEL
Two years after launching its state-of-the-art PCB facility, SEL shares lessons in vision, execution, and innovation, plus insights from industry icons and technology leaders shaping the future of PCB fabrication.
Sales: From Pitch to PO
From the first cold call to finally receiving that first purchase order, the July PCB007 Magazine breaks down some critical parts of the sales stack. To up your sales game, read on!
The Hole Truth: Via Integrity in an HDI World
From the drilled hole to registration across multiple sequential lamination cycles, to the quality of your copper plating, via reliability in an HDI world is becoming an ever-greater challenge. This month we look at “The Hole Truth,” from creating the “perfect” via to how you can assure via quality and reliability, the first time, every time.
- Articles
- Columns
- Links
- Media kit
||| MENU - pcb007 Magazine
Würth Elektronik and FELA Collaborate on PCB Technology Digitization
December 13, 2017 | Würth ElektronikEstimated reading time: 3 minutes
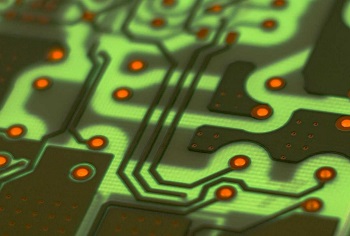
Started early in 2017, the two PCB fabricators Würth Elektronik and FELA with their sites in the land Baden Wurttemberg, have been jointly researching on PCB technology digitization. Prototype results in July were encouraging already – in October both partners dispatched first serial orders of their respective pilot projects.
The s.mask technology pushed by FELA and Würth pursues an approach of coating a defined functional surface by 3-D print, independent of varnish and machine fleet. This is – from both companies‘ perspective – the best starting point for gradually digitizing PCB production and its inherent processes.
Initial material tests and examination results prove a tremendously improved accuracy and various options for an application-specific mask definition. Both offset and basic tolerance ranges can be significantly reduced that way.
Especially the individual surface design allows consideration of customer demands and special requirements, e.g. on dielectric strength values. S.mask as the first and sole technology in the PCB sector allows for direct coating of even more than just one layer of defined and precisely designed dielectric.
First trial series on soldering processes brought another outstanding per-formance to light: Notable improvement could be achieved for most of soldering and assembly issues previously known. Should these observations be confirmed during the test runs envisaged for early 2018, they would yield immense benefits. Both partners are expecting concrete statements for mid of 2018 already.
Norbert Krütt, managing director of FELA in Villingen-Schwenningen, is highly satisfied with the outcomes achieved so far: "The digitization of PCB technology represents a real quantum leap under technological aspects. Functional coatings respectively dielectric are no more generously dispersed like with a watering can but rather utilized in a targeted manner for realizing benefits in downstream processes at both stages, within the PCB production and those at our customers’ sites.“
Beside the advantages in precision and performance, first pilot projects also show an upgrade of the PCB protection, turning out well through gentle application of the functional coating as well as reduced quantity and kind of the chemicals deployed.
The cooperation is conducted at all levels, from top management via R&D up to shared communication. Andreas Gimmer, managing director of Würth Elektronik CBT in Schopfheim, says: "Since the time we started our cooperative partnership, it has been seen that the way our companies are working together provides multifarious synergies. We expect economic success for us, but also find that common research and development is simply pleasure.“
About Würth Elektronik Circuit Board Technology (CBT)
Würth Elektronik Circuit Board Technology was founded in 1971 and has established itself as one of the leading PCB manufacturers in Europe. De-velopers are able get standard circuit boards, new and innovative technolo-gies and even complete system solutions all from one source. Here at Würth Elektronik, we cover the entire product life cycle, from the initial idea for a design, for example during early R&D projects, to the production of prototypes on the online shop WEdirekt and finally, manufacturing of medium and large volumes in Germany or Asia. Knowledgeable specialists are not just located at our German plants. Internationalization is an important strategic aspect for Würth Elektronik. We have numerous sales teams set up across many European countries.
Every day more than 120 new PCB designs enter our production. We have over 4,000 customers, ranging from large corporations to one-man designers. In addition to the personal care provided through our dense network of over 100 internal and external sales people, customers also have the option to purchase printed circuit boards online through the easy to use online shop, WEdirekt.
For more information, click here.
About FELA GmbH
FELA is one of the five largest circuit board manufacturers in Germany and has made the leap from simple contract manufacturer to innovative system provider. “Help us shape the future!” – with this motto, FELA GmbH is a fixture on today’s market.
FELA, a private, independent medium-sized enterprise based in the south-ern Black Forest with a 165-strong workforce, generated sales of €23.6m in 2016. The company has its headquarters in Villingen-Schwenningen and an additional distribution centre in Solingen.
As well as manufacturing and selling FR4-based circuit boards, other mainstays of the company’s activities include manufacturing capacitive glass input systems with the brand name FELAM GLASLINE and, as a technological leader, FELAM THERMOLINE technology, IMS circuit boards and sys-tems for aluminium or copper-based power LED applications. For more information, click here.
Testimonial
"We’re proud to call I-Connect007 a trusted partner. Their innovative approach and industry insight made our podcast collaboration a success by connecting us with the right audience and delivering real results."
Julia McCaffrey - NCAB GroupSuggested Items
Global PCB Connections: Understanding the General Fabrication Process—A Designer’s Hidden Advantage
08/14/2025 | Markus Voeltz -- Column: Global PCB ConnectionsDesigners don’t need to become fabricators, but understanding the basics of PCB fabrication can save you time, money, and frustration. The more you understand what’s happening on the shop floor, the better you’ll be able to prevent downstream issues. As you move into more advanced designs like HDI, flex circuits, stacked vias, and embedded components, this foundational knowledge becomes even more critical. Remember: the fabricator is your partner.
MKS’ Atotech to Participate in IPCA Electronics Expo 2025
08/11/2025 | AtotechMKS Inc., a global provider of enabling technologies that transform our world, announced that its strategic brands ESI® (laser systems) and Atotech® (process chemicals, equipment, software, and services) will showcase their latest range of leading manufacturing solutions for printed circuit board (PCB) and package substrate manufacturing at the upcoming 17th IPCA Show to be held at Pragati Maidan, New Delhi from August 21-23, 2025.
MKS Showcases Next-generation PCB Manufacturing Solutions at the Thailand Electronics Circuit Asia 2025
08/06/2025 | MKS Instruments, Inc.MKS Inc, a global provider of enabling technologies that transform our world, today announced its participation in Thailand Electronics Circuit Asia 2025 (THECA 2025), taking place August 20–22 at BITEC in Bangkok.
Point2 Technology, Foxconn Interconnect Technology Partner to Revolutionize AI Cluster Scalability with Terabit-Speed Interconnect
08/06/2025 | BUSINESS WIREPoint2 Technology, a leading provider of ultra-low-power, low-latency mixed-signal SoC solutions for multi-terabit interconnect, and Foxconn Interconnect Technology (FIT), a global leader in precision interconnect solutions, have signed a Memorandum of Understanding (MOU) to accelerate the commercialization of next-generation Active RF Cable (ARC) and Near Pluggable e-Tube (NPE) solutions.
Advancing Electrolytic Copper Plating for AI-driven Package Substrates
08/05/2025 | Dirk Ruess and Mustafa Oezkoek, MKS’ AtotechThe rise of artificial intelligence (AI) applications has become a pivotal force driving growth in the server industry. Its challenging requirements for high-frequency and high-density computing are leading to an increasing demand for development of advanced manufacturing methods of package substrates with finer features, higher hole densities, and denser interconnects. These requirements are essential for modern multilayer board (MLB) designs, which play a critical role in AI hardware. However, these intricate designs introduce considerable manufacturing complexities.