-
- News
- Books
Featured Books
- smt007 Magazine
Latest Issues
Current IssueMoving Forward With Confidence
In this issue, we focus on sales and quoting, workforce training, new IPC leadership in the U.S. and Canada, the effects of tariffs, CFX standards, and much more—all designed to provide perspective as you move through the cloud bank of today's shifting economic market.
Intelligent Test and Inspection
Are you ready to explore the cutting-edge advancements shaping the electronics manufacturing industry? The May 2025 issue of SMT007 Magazine is packed with insights, innovations, and expert perspectives that you won’t want to miss.
Do You Have X-ray Vision?
Has X-ray’s time finally come in electronics manufacturing? Join us in this issue of SMT007 Magazine, where we answer this question and others to bring more efficiency to your bottom line.
- Articles
- Columns
- Links
- Media kit
||| MENU - smt007 Magazine
It’s Time to Retire ROSE Testing
June 27, 2018 | Joe Russeau, Precision Analytical Laboratory, and Mark Northrup, IEC ElectronicsEstimated reading time: 3 minutes
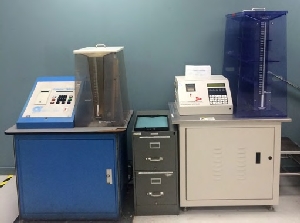
For decades now, the electronics industry has had a growing need to understand the impacts of chemical residues on PCB and PCBA reliability. Residues left from flux and other process chemistries can potentially lead to premature failure of assemblies once in the field. Understanding where such residues originate and their impact on product function is paramount to mitigating product failures due to cleanliness issues. One tool that has been used for decades to evaluate printed board and assembly cleanliness has been the resistivity of solvent extract (ROSE) test.
The ROSE test was developed in the early 1970s by the Naval Avionics Warfare Center in Indianapolis, Indiana. The early test used a squeeze bottle containing a solvent comprised of 75% 2-propanol and 25% deionized water (75/25). The surface of an assembly was rinsed with the 75/25 mixture and any material (e.g., flux) easily soluble in the mixture was dissolved and captured in a beaker. The resistivity of the captured solution was measured, and the result was expressed in terms of sodium chloride equivalents (NaCl eq.). Later versions of the test were automated and a 10.06 microgram (μg) of NaCl eq./in2 (1.56 μg of NaCl eq./cm2) limit was eventually ascribed to the test. That limit became enshrined in various military specifications, such as MIL-P-28809 and WS-6536 and eventually became the industry pass/fail standard. The limit persists today and is used across a wide base of material sets, from bare boards to assemblies to components.
Over the last two to three years, there has been considerable discussion within various IPC committees about the role of the ROSE test in today’s assembly environment. The transition from predominantly water wash processes to “no clean” has meant the advent of very different flux compositions. The question has been posed—on numerous occasions, we might add—as to whether the ROSE test is still a viable option for evaluating PCB and PCBA cleanliness. There have essentially been two camps of thought on the subject: those who want to continue using the test and re-invent it as a process control tool and those that think the test has run its useful course.
To update the test, IPC’s J-STD-001 committee commissioned a subgroup of users and subject matter experts to determine if there was a best-practices use that would bolster its continued application. Two conclusions were reached by that subgroup. First, the ROSE test should no longer be referred to as a cleanliness test, but as a process control tool. This was a reasonable conclusion since ROSE was never meant for cleanliness as industry had defined it. Second, users of the test must provide objective evidence, aside from just ROSE alone, to show that their manufacturing process is in control. More information about what the subgroup defined as “objective” evidence can be found in IPC-WP-019.
The statement made in the title to this article is where we want to focus most of our discussion. We are in the camp that believes the ROSE test provides little value for evaluating today’s assembly products and here’s why. The first significant concern with the validity of the ROSE test is the solvent. Back when the test was developed the predominant flux being used was heavily comprised of rosin (>30%). The 75/25 mixture was a very effective solvent for breaking down that flux and bringing it into solution. This is an important factor to consider because to accurately measure the amount of residual flux on a PCBA, you must first have a solvent that can dissolve it into solution. This is one of the major problems with the ROSE test today.
Why is the solvent an important consideration? Typically, four questions that are asked when performing cleanliness testing of assemblies. The questions are as follows:
1. What types of residues are on the surface of the assembly?
2. What are the concentrations of those residues?
3. Do those residues/concentrations pose any risk to product performance/function?
4. Where are the residues originating?
To have any hope of answering these questions, we need to consider a testing platform with two very specific attributes: selectivity and sensitivity. With the advances in board design, product miniaturization, process improvement and the myriad of chemicals used in assembly production today, a bulk-solvent measurement is not adequate for determining if there are any hidden residue traps.
To read the full version of this article, which appeared in the in the May 2018 issue of SMT007 Magazine, click here.
Suggested Items
Magnalytix and Foresite to Host Technical Webinar on SIR Testing and Functional Reliability
06/26/2025 | MAGNALYTIXMagnalytix, in collaboration with Foresite Inc., is pleased to announce an upcoming one-hour Webinar Workshop titled “Comparing SIR IPC B-52 to Umpire 41 Functional & SIR Test Method.” This session will be held on July 24, 2025, and is open to professionals in electronics manufacturing, reliability engineering, and process development seeking insights into new testing standards for climatic reliability.
IPC Rebrands as Global Electronics Association: Interview With Dr. John W. Mitchell
06/22/2025 | Marcy LaRont, I-Connect007Today, following a major announcement, IPC is embracing the rapid advancement of technology with a bold decision to change its name to the Global Electronics Association. This name more accurately reflects the full breadth of its work and the modern realities of electronics manufacturing. In this exclusive interview, Global Electronics Association President and CEO Dr. John W. Mitchell shares the story behind the rebrand: Why now, what it means for the industry, and how it aligns with the organization’s mission.
Global Electronics Association Debuts; New Name Elevates IPC’s 70-Year Legacy as Voice of $6 Trillion Electronics Industry
06/25/2025 | Global Electronics AssociationToday begins a new chapter for IPC as it officially becomes the Global Electronics Association, reflecting its role as the voice of the electronics industry. Guided by the vision of “Better electronics for a better world,” the Global Electronics Association (electronics.org) is dedicated to enhancing supply chain resilience and promoting accelerated growth through engagement with more than 3,000 member companies, thousands of partners, and dozens of governments across the globe.
I-Connect007 Editor’s Choice: Five Must-Reads for the Week
06/20/2025 | Andy Shaughnessy, I-Connect007It’s been a busy week in this industry, and we have news and articles from the PCB design, fabrication and assembly communities. Some of this news is out of this world. We may be losing the high ground—the really high ground. Columnist Jesse Vaughan explains how the U.S. seems to be falling behind in space, and how this could affect our ability to defend ourselves in the future. We have an update on the U.S.-China tariff talks, which seem to be moving forward, though sometimes at a snail’s pace.
New IPC VP Joe Schneider Building Stronger Focus on U.S., Canada
06/19/2025 | Marcy LaRont, I-Connect007IPC has hired Joe Schneider as a vice president to strengthen its regional focus and address the specific needs in the U.S. and Canada. Joe brings a rich background in OEM and contract manufacturing, including with industry giants like Siemens and Abbott Laboratories. In this interview, he shares his vision for the region, which emphasizes workforce development and supply chain challenges.