-
- News
- Books
Featured Books
- pcb007 Magazine
Latest Issues
Current IssueInventing the Future with SEL
Two years after launching its state-of-the-art PCB facility, SEL shares lessons in vision, execution, and innovation, plus insights from industry icons and technology leaders shaping the future of PCB fabrication.
Sales: From Pitch to PO
From the first cold call to finally receiving that first purchase order, the July PCB007 Magazine breaks down some critical parts of the sales stack. To up your sales game, read on!
The Hole Truth: Via Integrity in an HDI World
From the drilled hole to registration across multiple sequential lamination cycles, to the quality of your copper plating, via reliability in an HDI world is becoming an ever-greater challenge. This month we look at “The Hole Truth,” from creating the “perfect” via to how you can assure via quality and reliability, the first time, every time.
- Articles
- Columns
- Links
- Media kit
||| MENU - pcb007 Magazine
Increasing Productivity for Flex Fabricators
November 14, 2018 | I-Connect007 Editorial TeamEstimated reading time: 11 minutes
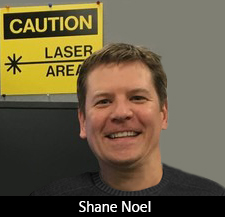
Barry Matties and Nolan Johnson of I-Connect007 met with Shane Noel and industry veteran Mike Jennings of ESI to discuss the introduction of their CapStone laser tool, a product aimed at doubling their flex circuit fabricators’ throughput. Mike also shares advice for fabricators who are looking to move into the ever-growing flex market.
Barry Matties: Shane, please start first by telling us a little bit about ESI?
Shane Noel: ESI is one of Oregon's oldest technology companies. We've been around since the 1940s. ESI started off as a test and measurement company for military and electronics. We have been serving the flex market since the late 1990s and developed laser-drilling applications in the flex market. The flex business has become a core business here, although we still do test and measurement, and we're moving into some other laser processing applications as well, like HDI.
Matties: And your role here is the product marketing manager?
Noel: Yes. I work as a product marketing manager in the flex business. I previously managed the applications engineering side of the flex business unit and it was a natural step in my career to move into the product marketing and management of that product. I now work under Patrick Riechel, the lead product manager.
Matties: Well, we recently received a press release announcing your new CapStone product. Why don't you just give a quick overview of what that technology is about?
Noel: The CapStone is building on and expanding upon our capabilities in flex processing. About six years ago we introduced the 5335 system, which is pretty much the gold standard in flex laser processing right now. The CapStone utilizes some of that technology and expands upon that technology to create even greater throughput and advantages in production and high volume manufacturing for our main customer base, which include the top 10 flex manufacturers in the world.
Our aim is to double throughput over our previous product in order to give the customers a better cost of ownership and also to improve upon yield and reliability. So we've also partnered with one of the top laser manufacturers to develop and uniquely market a laser engine that can utilize our technology capabilities in the beam-positioning field and provide that throughput to the work surface, which a lot of older technologies could not provide.
Matties: So in your press release you talked about how it was twice the speed. That's quite an accomplishment right there. Still a competitive price and adding capacity in a smaller footprint, basically.
Noel: That's right. If you double your throughput, you have to invest in less of the large machines on your floor, which has been a continual problem with a lot of our customers. As they build out their factories, they find that they fill up their rooms with laser systems when they get a large order, and then they have to build another factory.
Matties: That was a bottleneck.
Noel: It's definitely a bottleneck because you've got to maintain all the facilities for each and every one of these tools. So as you mentioned, the new system doubles the throughput over the older system that we provided, which was already the industry leader. We're not doing this by doubling the amount of laser heads or anything like this. It all comes from our optical beam delivery technology.
Matties: We were talking earlier about the digital factory, the data part of the factory. How is your equipment plugging into that strategy for people?
Noel: That's an excellent question. Like most companies in the industry, we’re looking for how to implement more automation into our systems as well as diagnostic tools for better health monitoring. For instance, we're getting ideas to put into our software, like easier data introduction to the tool. The current process is to use an offline CAD/CAM system to take the customer data, work it into a format that we can use on a tool. We're working right now with one of our partners in Taiwan to bring in direct data import from what their customers provide them so that they take this step out of the process.
In addition, we’re looking at how best to implement remote communication with our tools, so you can see a snapshot of the health of that tool and then start to better predict when to perform a service intervention.
Matties: That's a great goal. You've been in the industry for many years, so there are a lot of ESI units out there. What about retrofitting or upgrading units in the field? Is that a possibility for someone who may not want to purchase this new one but wants some of the benefits?
Noel: That's a good point. So with the new tool, we have developed certain features from feedback from our customers, including even better protection of the optical path than previously available. On our last generation of systems, those had more service interventions than we, as well as our customers, would like to see. On the new tool, that improved protection is designed in, and during that design, we backported that into the older tool. Customers can purchase this option. You can retrofit your old system, or you can buy that older tool with the new optical path. All the software features, all those automated features, are going to be backportable into the older tools. And then again, in our roadmap, we're looking at improving accuracy and being able to backport that also into our older tools.
Matties: Mike, you've been in this part of the industry for many years.
Mike Jennings: I'm starting year 43 in bare boards.
Matties: Wow! Congratulations. You've seen a lot of changes. What are some of the most notable changes that you've seen in this sector?
Jennings: In the flex sector, it's been the change. If you go back years and years ago, the flex sector was focused on military, aerospace, small production runs, cable replacements, heaters, basic levels of technology. They're now the building blocks of the devices we carry every day. You can't have a cellphone or a tablet without having multiple iterations of flex circuits on many different kinds of materials.Page 1 of 2
Testimonial
"In a year when every marketing dollar mattered, I chose to keep I-Connect007 in our 2025 plan. Their commitment to high-quality, insightful content aligns with Koh Young’s values and helps readers navigate a changing industry. "
Brent Fischthal - Koh YoungSuggested Items
Meet the Author Podcast: Martyn Gaudion Unpacks the Secrets of High-Speed PCB Design
07/16/2025 | I-Connect007In this special Meet the Author episode of the On the Line with… podcast, Nolan Johnson sits down with Martyn Gaudion, signal integrity expert, managing director of Polar Instruments, and three-time author in I-Connect007’s popular The Printed Circuit Designer’s Guide to... series.
Intervala Hosts Employee Car and Motorcycle Show, Benefit Nonprofits
08/27/2024 | IntervalaIntervala hosted an employee car and motorcycle show, aptly named the Vala-Cruise and it was a roaring success! Employees had the chance to show off their prized wheels, and it was incredible to see the variety and passion on display.
KIC Honored with IPC Recognition for 25 Years of Membership and Contributions to Electronics Manufacturing Industry
06/24/2024 | KICKIC, a renowned pioneer in thermal process and temperature measurement solutions for electronics manufacturing, is proud to announce that it has been recognized by IPC for 25 years of membership and significant contributions to electronics manufacturing.
Boeing Starliner Spacecraft Completes Successful Crewed Docking with International Space Station
06/07/2024 | BoeingNASA astronauts Barry "Butch" Wilmore and Sunita "Suni" Williams successfully docked Boeing's Starliner spacecraft to the International Space Station (ISS), about 26 hours after launching from Cape Canaveral Space Force Station.
KIC’s Miles Moreau to Present Profiling Basics and Best Practices at SMTA Wisconsin Chapter PCBA Profile Workshop
01/25/2024 | KICKIC, a renowned pioneer in thermal process and temperature measurement solutions for electronics manufacturing, announces that Miles Moreau, General Manager, will be a featured speaker at the SMTA Wisconsin Chapter In-Person PCBA Profile Workshop.