-
- News
- Books
Featured Books
- pcb007 Magazine
Latest Issues
Current IssueInventing the Future with SEL
Two years after launching its state-of-the-art PCB facility, SEL shares lessons in vision, execution, and innovation, plus insights from industry icons and technology leaders shaping the future of PCB fabrication.
Sales: From Pitch to PO
From the first cold call to finally receiving that first purchase order, the July PCB007 Magazine breaks down some critical parts of the sales stack. To up your sales game, read on!
The Hole Truth: Via Integrity in an HDI World
From the drilled hole to registration across multiple sequential lamination cycles, to the quality of your copper plating, via reliability in an HDI world is becoming an ever-greater challenge. This month we look at “The Hole Truth,” from creating the “perfect” via to how you can assure via quality and reliability, the first time, every time.
- Articles
- Columns
- Links
- Media kit
||| MENU - pcb007 Magazine
Staying Current on Flex Manufacturing is Smart Business
April 4, 2019 | Barry Matties, I-Connect007Estimated reading time: 4 minutes
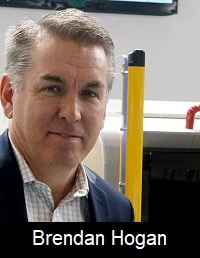
Brendan Hogan, managing director of smart electronics manufacturer MivaTek Global, discusses how to better design for flex, and ways designers can stay current on manufacturing technology that can impact their flex boards.
Barry Matties: First, can you tell us a little bit about MivaTek and what you do?
Brendan Hogan: Miva Technologies has developed a new method of using DLP and LED. About six or seven years ago, we replaced the laser technology with a DLP-LED technology with a lower cost of operation and all the obvious drivers to do that. We’ve evolved very quickly over the last four to five years to get better market penetration in the U.S., Europe, and parts of Asia now. We’re starting to expand more rapidly. One of the benefits of our technology is that it maps into many different platforms, and is pretty simple to map in a new platform. So, that gives us a lot of specialty application opportunities.
Matties: How do your products fit into the flex area?
Hogan: A lot of the flex applications we currently do largely deal with A/B registration—the precision with which you can have the two sides run a check to each other for signal-to-noise ratio or certain performance criteria, and how that end circuit performs in applications. That’s a more conventional application. In the last 12–16 months, we’ve been developing systems for reel-to-reel that have implications for flex and things like LED shadow mask and other reel-to-reel type applications. We see a lot of activity in Korea and China related to reel-to-reel, so that’s one of the main directions we’re headed.
Matties: If an OEM and their system designers are looking at integrating flex into their products, what considerations should they have in terms of imaging and technology that might help them improve either their overall quality or strategy?
Hogan: A significant element of direct imaging in general—whether you’re talking about MivaTek or anybody else—has to do with removing the A/B registration from an operator standpoint, and moving it into a digital camera-driven technology. You have better repeatability and control over your line width so that you can have a more predictive circuit at the end of the day. The other aspect with some of our systems is that you can go to larger and have longer cabling to reduce the connectivity from one circuit to the next. Thus, you don’t need connectors and can have much longer ribbon cables if you have a more extensive format system.
Matties: How does his designer learn about this or integrate this into their thinking?
Hogan: That’s a job for us in the marketing department to make sure we get out there and start writing more technical articles. The latest development of reel-to-reel technology is only starting to hit the market. We should be doing a better job, I suppose, of direct access through fine magazines like your own.
Matties: Thank you for that. What are the major points that they should consider when you say, “We need to tell the story more for them to understand us?” What is critical for them to know?
Hogan: Perhaps doing broader research than only talking to the circuit producer would help, so looking at some other standards and trying to understand what technologies are out there. The hard part about things like equipment technology is that as they emerge, a select few know about it. It’s very difficult to access the entire market simultaneously, so it’s kind of the job of the designer to be aware of what’s coming so that they can get into the design pattern. There’s a significant lag in the design loop—the lag time between design and production for the producer. By the time it hits the market for them, the product may be already outdated in terms of manufacturing technology and the best approach.
Matties: If somebody is looking at bringing flex into their product mix for the first time, do you have any advice for that?
Hogan: Well, that’s an interesting discussion because the transition from rigid panels to flex is an art form—it’s another animal. Participation in some of the industry groups is a valuable asset. Tap into the existing knowledge that’s out there, like IPC APEX EXPO in the U.S. or HKPCA in China, which both have a variety of training sessions on trade information. Establish best practice for that transition. There are a lot of new technologies and manufacturing methods coming. We participate in an organization called the CHIPS consortium, which is a group that formed to find new manufacturing methods. It’s out of the University of California, Los Angeles (UCLA) in the U.S. We’re also part of a group with Apple and Google trying to find lower-cost methods for manufacturing these high-tech products. Participation in those groups seems like a cost factor because it’s not the high priorities that we’re all driven by, but it adds a lot of benefits for long-term planning.
To read the full article, which appeared in the January 2019 issue of FLEX007 Magazine, click here.
Testimonial
"We’re proud to call I-Connect007 a trusted partner. Their innovative approach and industry insight made our podcast collaboration a success by connecting us with the right audience and delivering real results."
Julia McCaffrey - NCAB GroupSuggested Items
Meet the Author Podcast: Martyn Gaudion Unpacks the Secrets of High-Speed PCB Design
07/16/2025 | I-Connect007In this special Meet the Author episode of the On the Line with… podcast, Nolan Johnson sits down with Martyn Gaudion, signal integrity expert, managing director of Polar Instruments, and three-time author in I-Connect007’s popular The Printed Circuit Designer’s Guide to... series.
Intervala Hosts Employee Car and Motorcycle Show, Benefit Nonprofits
08/27/2024 | IntervalaIntervala hosted an employee car and motorcycle show, aptly named the Vala-Cruise and it was a roaring success! Employees had the chance to show off their prized wheels, and it was incredible to see the variety and passion on display.
KIC Honored with IPC Recognition for 25 Years of Membership and Contributions to Electronics Manufacturing Industry
06/24/2024 | KICKIC, a renowned pioneer in thermal process and temperature measurement solutions for electronics manufacturing, is proud to announce that it has been recognized by IPC for 25 years of membership and significant contributions to electronics manufacturing.
Boeing Starliner Spacecraft Completes Successful Crewed Docking with International Space Station
06/07/2024 | BoeingNASA astronauts Barry "Butch" Wilmore and Sunita "Suni" Williams successfully docked Boeing's Starliner spacecraft to the International Space Station (ISS), about 26 hours after launching from Cape Canaveral Space Force Station.
KIC’s Miles Moreau to Present Profiling Basics and Best Practices at SMTA Wisconsin Chapter PCBA Profile Workshop
01/25/2024 | KICKIC, a renowned pioneer in thermal process and temperature measurement solutions for electronics manufacturing, announces that Miles Moreau, General Manager, will be a featured speaker at the SMTA Wisconsin Chapter In-Person PCBA Profile Workshop.