-
-
News
News Highlights
- Books
Featured Books
- pcb007 Magazine
Latest Issues
Current IssueThe Hole Truth: Via Integrity in an HDI World
From the drilled hole to registration across multiple sequential lamination cycles, to the quality of your copper plating, via reliability in an HDI world is becoming an ever-greater challenge. This month we look at “The Hole Truth,” from creating the “perfect” via to how you can assure via quality and reliability, the first time, every time.
In Pursuit of Perfection: Defect Reduction
For bare PCB board fabrication, defect reduction is a critical aspect of a company's bottom line profitability. In this issue, we examine how imaging, etching, and plating processes can provide information and insight into reducing defects and increasing yields.
Voices of the Industry
We take the pulse of the PCB industry by sharing insights from leading fabricators and suppliers in this month's issue. We've gathered their thoughts on the new U.S. administration, spending, the war in Ukraine, and their most pressing needs. It’s an eye-opening and enlightening look behind the curtain.
- Articles
- Columns
- Links
- Media kit
||| MENU - pcb007 Magazine
An Examination of Glass-fiber and Epoxy Interface Degradation in Printed Circuit Boards
July 12, 2019 | Bhanu Sood, Michael Osterman, and Michael Pecht, Center for Advanced Life Cycle EngineeringEstimated reading time: 9 minutes
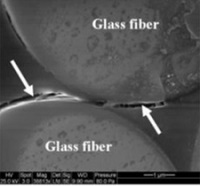
Multilayer organic laminates, which make up over 90% of the interconnecting substrates in electronics (standard FR-4 represents 85% of the substrates used for laminates), can develop a loss of electrical insulation resistance between two biased conductors due to conductive filament formation. The probability of conductive filament formation is a function of the temperature, moisture content, voltage bias, manufacturing quality and processes, materials, and other environmental conditions and physical factors.
With increases in design density and tighter spacing between conductors, the probability of failure due to conductive filament formation (CFF) in printed circuit board (PCB) electronic assemblies has increased. CFF is a failure observed within glass-reinforced epoxy PCB laminates caused by an electrochemical process involving the ionic transport of a metal through or across a non-metallic medium under the influence of an applied electric field [1 & 2]. The growth of the metallic filament is a function of temperature, humidity, voltage, laminate materials, manufacturing processes, and the geometry and spacing of the conductors [2]. The growth of these filaments can cause an abrupt loss of insulation resistance between the conductors under a DC voltage bias.
A statistical examination of field returns and root cause analysis performed at the Center for Advanced Life Cycle Engineering (CALCE) at the University of Maryland shows that failures in PCBs account for a significant percentage of field returns in electronic products and systems. Studies on CFF [2 & 3] have found that path formation in a PCB is often along the glass fiber to epoxy matrix interface (Figure 1).
Figure 1: Schematic describing CFF growth [3].
Delamination along the fiber-resin interface can occur as a result of stresses generated under thermal cycling due to coefficient of thermal expansion (CTE) mismatch between the glass fiber (CTE = ~5.5 ppm/°C) and the epoxy resin (CTE = ~65 ppm/°C) (Figure 2). CFF can take place in the plated through-hole to plated through-hole (PTH-PTH), PTH-plane, and trace-trace geometries.
Figure 2: CFF growth path along the glass fiber and resin interface [3].
A two-step model was developed to explain the growth of conductive filaments at the resin-glass interface in PCBs [1 & 3] where degradation of the resin-glass interfacial bond first occurs, followed by an electrochemical reaction. According to Lando [2], the path required for the transportation of metal ions formed by the degradation of the resin-glass interfacial bond results from the mechanical release of stresses, poor glass treatment, hydrolysis of the silane glass finish, or stresses originating from moisture-induced swelling of the epoxy resin.
Path formation was reported to be independent of bias; however, humidity was identified as a contributing factor towards degradation. After path formation, the PCB is viewed as an electrochemical cell. In this cell, the copper conductors are the electrodes, the absorbed water is the electrolyte, and the driving potential for the electrochemistry is the operating or test potential of the circuit. The electrode reactions for the metal migration are:
At the anode:
Equation 1:
Equation 2:
At the cathode:
Equation 3:
Pathway Formation in CFF
In PCBs, one manner in which the pathway between conductors is formed is through chemical hydrolysis of the silane glass finish or coupling agent. Past work has shown that the glass epoxy interface absorbs five to seven times more moisture than the bulk epoxy [5]. A common cross-linking agent used in FR-4 and many other epoxy-based laminated systems is dicyandiamide, or dicy. Dicy and glass surfaces are both hydrophilic. This combination of a hydrophilic surface and cross-linking agent is one of the factors responsible for the degradation of the glass fiber-epoxy resin interface due to hydrolysis. Williams [6] has shown that PCBs manufactured with non-dicy cross-linked epoxy resins are more resistance to CFF failures than PCBs manufactured with dicy cross-linked epoxy resins.
Organosilanes are bifunctional molecules that act as adhesion promoters, crosslink agents, and moisture scavengers in adhesive and sealant products [7]. Silane adhesion promoters act as molecular bridges between two chemically different materials and have been shown to dramatically improve the adhesion of polymeric resins to substrates such as glass, silica, alumina, or active metals.
Page 1 of 3
Suggested Items
The Evolution of Picosecond Laser Drilling
06/19/2025 | Marcy LaRont, PCB007 MagazineIs it hard to imagine a single laser pulse reduced not only from nanoseconds to picoseconds in its pulse duration, but even to femtoseconds? Well, buckle up because it seems we are there. In this interview, Dr. Stefan Rung, technical director of laser machines at Schmoll Maschinen GmbH, traces the technology trajectory of the laser drill from the CO2 laser to cutting-edge picosecond and hybrid laser drilling systems, highlighting the benefits and limitations of each method, and demonstrating how laser innovations are shaping the future of PCB fabrication.
Day 2: More Cutting-edge Insights at the EIPC Summer Conference
06/18/2025 | Pete Starkey, I-Connect007The European Institute for the PCB Community (EIPC) summer conference took place this year in Edinburgh, Scotland, June 3-4. This is the third of three articles on the conference. The other two cover Day 1’s sessions and the opening keynote speech. Below is a recap of the second day’s sessions.
Day 1: Cutting Edge Insights at the EIPC Summer Conference
06/17/2025 | Pete Starkey, I-Connect007The European Institute for the PCB Community (EIPC) Summer Conference took place this year in Edinburgh, Scotland, June 3-4. This is the second of three articles on the conference. The other two cover the keynote speeches and Day 2 of the technical conference. Below is a recap of the first day’s sessions.
Preventing Surface Prep Defects and Ensuring Reliability
06/10/2025 | Marcy LaRont, PCB007 MagazineIn printed circuit board (PCB) fabrication, surface preparation is a critical process that ensures strong adhesion, reliable plating, and long-term product performance. Without proper surface treatment, manufacturers may encounter defects such as delamination, poor solder mask adhesion, and plating failures. This article examines key surface preparation techniques, common defects resulting from improper processes, and real-world case studies that illustrate best practices.
RF PCB Design Tips and Tricks
05/08/2025 | Cherie Litson, EPTAC MIT CID/CID+There are many great books, videos, and information online about designing PCBs for RF circuits. A few of my favorite RF sources are Hans Rosenberg, Stephen Chavez, and Rick Hartley, but there are many more. These PCB design engineers have a very good perspective on what it takes to take an RF design from schematic concept to PCB layout.