EPFL is Developing Next-Generation Soft Hearing Implants
October 21, 2019 | EPFLEstimated reading time: 2 minutes
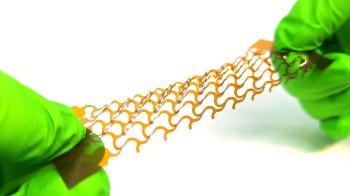
Working with clinicians from Massachusetts Eye and Ear and Harvard Medical School, a team of EPFL researchers has developed a conformable electrode implant that will allow people with a dysfunctional inner ear to hear again. This new device could replace existing auditory brainstem implants, which have a number of shortcomings.
Close to half a million people around the world suffer from a serious hearing impairment. In some cases, they can find relief in cochlear and other types of implants. Yet these devices do not help people whose inner ear is damaged or whose auditory nerve does not function properly.
For these patients to recover their sense of hearing, electrical signals must be sent directly to the auditory brainstem. The neuroprosthetic used for this purpose is called an auditory brainstem implant, or ABI. Yet the outcomes of ABIs are mixed and, in many cases, patients recover only sound perception. What’s more, clinical ABIs are stiff and cannot conform precisely to the curvature of the auditory brainstem.
To address this problem, Stéphanie Lacour's team at EPFL’s Laboratory for Soft BioElectronic Interface (LSBI) worked with clinicians from Harvard Medical School and Massachusetts Eye and Ear to develop a soft electronic interface. The highly elastic implant conforms neatly to the curved surface of the auditory brainstem and can therefore send highly targeted electrical signals. It has been tested successfully on mice—the implant has a surface area only 0.25 mm2—and has now been produced at a size suitable for human use and in a form that is compatible with current surgical techniques. It will undergo further study in preparation for human trials. The researchers’ study was just published in Science Translational Medicine.
Inspired by Japanese Cutouts
The new implant consists of a conformable array of platinum electrodes encased in silicone. “We focused on platinum because it’s already used widely in clinical settings,” says Nicolas Vachicouras, a post-doc at EPFL's School of Engineering and the article’s lead author.
Unfortunately, platinum is a rigid metal that cannot be distorted without being damaged. The researchers overcame this hurdle by applying the traditional Japanese paper-cutting technique called kirigami, etching a Y-shaped pattern into metalized plastic segments. Then they machined the metal at the micron scale (one micron = one thousandth of a millimeter), using techniques commonly found in the microfabrication of integrated circuits. The result is a very compliant and highly conductive electrode implant.
The EPFL researchers are already eyeing other applications. “The properties of our device would be of value for all sorts of implantable neuroprosthetics,” says Stéphanie Lacour, “such as those used to stimulate or record neural activity in the spine, brain or even peripheral nerves.”
Suggested Items
Happy’s Tech Talk #38: Novel Metallization for UHDI
05/07/2025 | Happy Holden -- Column: Happy’s Tech TalkI have been involved in high-density electronics substrates since 1970 when I joined Hewlett-Packard’s RF semiconductor group after college. Figure 1 shows the difference between trace/space lithography for substrates and silicon starting in 1970. My projects involved sapphire circuits for RF devices, but the figure displays the state of PCBs and integrated CMOS circuits and their packaging, not discreet RF devices. Even then, semiconductors were 50X higher density.
New Database of Materials Accelerates Electronics Innovation
05/05/2025 | ACN NewswireIn a collaboration between Murata Manufacturing Co., Ltd., and the National Institute for Materials Science (NIMS), researchers have built a comprehensive new database of dielectric material properties curated from thousands of scientific papers.
New Database of Materials Accelerates Electronics Innovation
05/02/2025 | ACN NewswireIn a collaboration between Murata Manufacturing Co., Ltd., and the National Institute for Materials Science (NIMS), researchers have built a comprehensive new database of dielectric material properties curated from thousands of scientific papers.
Micron Announces Business Unit Reorganization to Capitalize on AI Growth Across All Market Segments
04/23/2025 | MicronMicron Technology, Inc., a leader in innovative memory and storage solutions, announced a market segment-based reorganization of its business units to capitalize on the transformative growth driven by AI, from data centers to edge devices.
Connected Commercial Drone Market to Reach $37.3 Billion Worldwide by 2029
04/04/2025 | Berg InsightBerg Insight, a leading IoT market research provider, today released a new report covering connected commercial drones used for industrial and governmental purposes.