Estimated reading time: 4 minutes
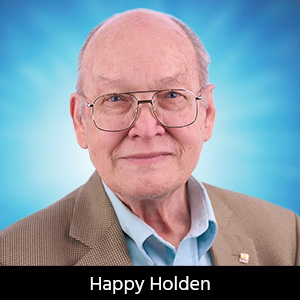
Contact Columnist Form
Happy’s Tech Talk #38: Novel Metallization for UHDI
I have been involved in high-density electronics substrates since 1970 when I joined Hewlett-Packard’s RF semiconductor group after college. Figure 1 shows the difference between trace/space lithography for substrates and silicon starting in 1970. My projects involved sapphire circuits for RF devices, but the figure displays the state of PCBs and integrated CMOS circuits and their packaging, not discreet RF devices. Even then, semiconductors were 50X higher density.
HP’s Involvement With Asia
I started in HP’s advanced semiconductor group. HP was a leader like IBM. However, it used sapphire for many high-frequency and thermal performances. The process was called silicon-on-sapphire (SoS). HP used this to create the first single-chip 4-, 8-, 12- 16-, 32- and 64-bit microprocessors over the next 40 years, as seen in Figure 1’s die size—driven by HP’s SoS/NMOS3 process. Today, the gap has increased 1600 times, and HP’s IC fab is now Broadcom.
This process led to HP’s heavy investment in Asia for back-end fabrication, assembly, and testing in Singapore and Malaysia. When HP became involved in creating advanced multilayer PCB fabrication in Taiwan in 1984 (where I was in charge of the project), I included our new HDI laser drilling process and metallization, which was 20 years ahead of IBM and Europe.
What Drives Metallization?
One of the oldest metallizations for PCBs was silver, first as a paste, then as an electroless conversion. This was later replaced when Shipley developed a reliable palladium/formaldehyde copper reduction process. Together with traditional sputtering and vacuum metal deposition, UHDI metallizations have increased to:
- Sputtering: Ti/Cu, Indium-tin-oxide (ITO), Carbon nano tube (CNT) (PlasmaLineD, Scheldahl-ViaThin)
- mSAP, amSAP, A/SAPTM with Cu foil (LQDX, ATOTECH, MacDermid, Uyemura)
- SAP with electroless copper Cu (ABF, AGC fastRise™)
- SAP with additive MOD inks (KDI)
- SAP with metallic conductive pastes (Ormet/TLPS, ALIVH, Bbit, PALUP, Parelec/PARAMOD, Namics/Unimac)
- Chemical vacuum deposition
- EHD: By Scrona allows inkjet printing of resin and metals with features down to 2 µm
- QCIATM (Hyperion QCPTM)
Metal-organic Decompositions (MOD) Inks/Pastes
The liquid metal inks and MOD inks/metallic conductive pastes are popular with newer additive processes for printed electronics. Their wide variety of materials and sources are seen in Table 1. The Ormet TLPS pastes have been around for a long time. I used them in the early 1990s, as did many other fabricators.
These conductive pastes were commonly used in Japan to develop HDI substrates without the need for electroplating. There were many processes developed, but all have fallen by the wayside as laser-drilling and various xSAP and AP have become dominant. Newer HDI processes, like VeCS3, which are true 3D in structure, are gaining popularity, especially in Asia.
The newer MOD metallizations have several advantages over older, traditional copper reduction chemistry:
- Significant size and weight reduction compared to current processes
- Improved reliability achieved through reduced layer count, microvias, and lamination cycles
- Reduced costs, specifically for complex, high-performance substrates
- Improved RF performance over traditional subtractive-etch processes
- Biocompatibility advantages of utilizing gold as a conductive metal
The ORMET-TLPS (OrmeLink) metallic paste has been used for the last 30 years to connect various multilayers to form HLC complex stackups.
Newer Methods of Metallization Application
Four of the newer methods, some still in development, are: laser ablation, direct printing, aerosol jet printing, and electrohydrodynamic (EHD) jet printing. Examples are shown in Figure 2.
- Laser ablation: Popular with Amkor-Korea and Siemens, lasers can ablate circuit trenches and vias, making them easy to fill with silver or MOD inks.
- Direct printing: Also conducted with lasers or LED light sources. The laser catalyzes the photosensitive metallization to become conductive.
- Aerosol printing: Prints at room temperature with a resolution of 15 µm L/S. The Ag MOD has high conductivity and a short curing time at 120°C. Thick, 10 µm printing can be achieved with multiple passes.
- Copper highlights: The initial test shows a resolution of <100 µm but needs to be cured under nitrogen.
Figure 3: An MOD inkjet prototype method of printing: the circuitJet2.
Summary
There are many methods now available to metallize UHDI substrates. In addition to the long-traditional electroless Cu, graphite, or sputtering, we now have MOD inks and pastes, even for prototyping. Figure 3 shows a portable MOD jet printer available today.
References
- “HDPUG Keynote-Advanced Packaging Substrate/Ultra HDI Update,” by Gene Weiner, PCB West, October 2024.
- SMTA Technical Knowledge, UHDI Symposium, January 2024, and UHDI Pavilion, October 2024.
- Happy’s Tech Talk #1: VeCS,” by Happy Holden, PCB007 Magazine, October 2021.
Happy Holden has worked in printed circuit technology since 1970 with Hewlett-Packard, NanYa Westwood, Merix, Foxconn, and Gentex. He is currently a contributing technical editor with I-Connect007, and the author of Automation and Advanced Procedures in PCB Fabrication, and 24 Essential Skills for Engineers.
This column originally appeared in the April 2025 issue of PCB007 Magazine.
More Columns from Happy’s Tech Talk
Happy’s Tech Talk #42: Applying Density Equations to UHDI DesignHappy’s Tech Talk #41: Sustainability and Circularity for Electronics Manufacturing
Happy’s Tech Talk #40: Factors in PTH Reliability—Hole Voids
Happy’s Tech Talk #39: PCBs Replace Motor Windings
Happy’s Tech Talk #37: New Ultra HDI Materials
Happy’s Tech Talk #36: The LEGO Principle of Optical Assembly
Happy’s Tech Talk #35: Yields March to Design Rules
Happy’s Tech Talk #34: Producibility and Other Pseudo-metrics