-
- News
- Books
Featured Books
- pcb007 Magazine
Latest Issues
Current IssueInventing the Future with SEL
Two years after launching its state-of-the-art PCB facility, SEL shares lessons in vision, execution, and innovation, plus insights from industry icons and technology leaders shaping the future of PCB fabrication.
Sales: From Pitch to PO
From the first cold call to finally receiving that first purchase order, the July PCB007 Magazine breaks down some critical parts of the sales stack. To up your sales game, read on!
The Hole Truth: Via Integrity in an HDI World
From the drilled hole to registration across multiple sequential lamination cycles, to the quality of your copper plating, via reliability in an HDI world is becoming an ever-greater challenge. This month we look at “The Hole Truth,” from creating the “perfect” via to how you can assure via quality and reliability, the first time, every time.
- Articles
- Columns
- Links
- Media kit
||| MENU - pcb007 Magazine
Looking Back on IPC’s First Annual Electronics Materials Forum
December 6, 2019 | Brook Sandy-Smith, IPCEstimated reading time: 5 minutes
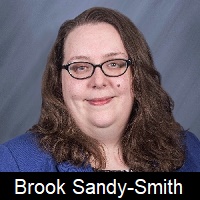
This year, IPC tried something new and developed a technical conference to bring together industry professionals focused on materials development. Typically, the electronics manufacturing world tends to silo itself into design, PCB fabrication, components/semiconductor, assembly, and cleaning/coatings/reliability. IPC’s Electronics Materials Forum stretched through each silo and focused on the commonality of developing the materials we all use. Topics ranged from the bare copper used to start the PCB fabrication process all the way to coatings used to protect the finished assembly and many in between. This resulted in a program with widely varied topics that bred lively discussions between silos.
The conference chairs, Dennis Fritz and Don Dupriest, developed this idea over the years of hosting conferences focused on HDI and flex circuits. Once I started at IPC, we connected, and I thought the idea of bringing materials developers and users together in one place was different than any of the conferences I’d previously attended and a great opportunity to share strategies. In my previous jobs, I had been very specialized in one type of material (e.g., solder alloys), but the developments in other areas of the industry were quite inspirational because of their approach and influential based on their goals. When it comes to design/development, there is a lot to be said about learning by watching other products in their development process.
There were about 20 presentations over the three-day conference and lively conversation over the panel discussion and breaks. While every presenter had intriguing insights, I would like to mention just a few that inspired me. First, our keynote speaker Lenora Clark, MacDermid Alpha, addressed advancements in automotive technologies that are driving advancements in electronics due to the unique challenges posed by the high requirements and critical nature of auto safety systems. She pulled on the audience’s heartstrings, talking about that personal connection we all seem to develop with our cars over the years. These aren’t just vehicles that get us from place to place; many of us do grow attached (I know I can’t bring myself to part with my old car right now).
From this idea, Lenora connected to some of the futuristic concepts related to autonomous vehicles that are becoming a reality in our lifetimes. Living room inspired interiors and infotainment systems that elevate the radios and eight-track players of the past to full navigational and informational powerhouses. The connectivity needed and the heightened requirements for these systems that operate all the time is a high bar to meet.
One example I remember really illustrated the point. Picture backup cameras or auto cameras that give any other view; they need to stay live all the time. The camera on your iPhone, for instance, could not do that because it would overheat. Also, there must be strategies to keep the lens clear, defogged, and focused. It’s not as easy as using devices from existing technologies, each one needs to be improved, and the use expanded. Lenora truly captured our hearts and minds and inspired us toward these goals, which require advancements in all facets of the materials we use in electronics.
The conference started with an overview from Dave Pinsky, leader of the Pb-free Electronics Risk Management (PERM) Council, which also met at this conference. This is a team of primarily defense and aerospace engineers who typically have not made the Pb-free transition along with the rest of the industry. It was interesting to hear the history of this group and the reasons they have continued to use tin-lead solder (and it’s not just because of tin whiskers).
The reliability required for a satellite, or some secret missile technology is so different than what is needed for any other application. This led into a discussion of the regulations that impact our material choices, presented by Kelly Scanlon, director of environment, health, and safety from IPC. Some of the drivers for change now come from material restrictions rather than new technological requirements.
There were also a couple of presentations about semi-additive processes. This is a different approach to building circuits that builds up the circuit instead of etching copper away to create the features. This enables much finer features and achieves better HDI designs. Thanks to Mike Vinson, Averatek Corporation, and Audra Thurston, Calumet Electronics Corporation, for illuminating the material advancements that made this possible as well as the details of early implementation of this concept. This is an emerging technology in its early adoption that could have real benefits and wide adoption soon.
Another presentation I’ve continued to think about was from Dr. Kunal Shah, LiloTree, who talked about a new surface finish without nickel. His approach to developing surface finishes that cooperate with the soldering process with the goal of improved solder joint reliability was eye-opening. I’m certainly no expert on surface finishes, but I always thought they were primarily focused on protecting the copper surfaces and promoting solderability. It’s awesome to think about what could be achieved with cooperation between the soldering process and surface finish development.
Lastly, I was very inspired by Topher Anderson’s, ZSK Research and Training Center, discussion of how embroidery techniques can be used to create novel flexible circuits and wearable devices. This concept reaches outside of conventional electronics design to open a world of possibilities for how to integrate electronics into any surface that is not flat. Even better, he brought along lots of prototypes to experience hands-on. It’s techniques like this that expand the way we think about circuits and tap into our creativity.
Overall, the IPC Electronics Materials Forum 2019 was a fun, welcoming, and insightful experience that expanded my understanding of the materials available to us today. The common thread throughout the forum was the value of collaboration when facing the challenges of future technologies. I want to thank all those mentioned as well as the other speakers and attendees for being so engaged and engaging. Events like this are the highlight of my year. There are such exciting advancements happening in materials, and I hope you join us to expand the horizons next year!
Brook Sandy-Smith is the technical conference program manager at IPC–Association Connecting Electronics Industries.
Testimonial
"The I-Connect007 team is outstanding—kind, responsive, and a true marketing partner. Their design team created fresh, eye-catching ads, and their editorial support polished our content to let our brand shine. Thank you all! "
Sweeney Ng - CEE PCBSuggested Items
Altus Supports Datalink Electronics with Advanced Selective Soldering Solution to Boost Manufacturing Efficiency
09/02/2025 | Altus GroupDatalink Electronics has partnered with Altus Group to integrate a cutting-edge automated soldering solution, enhancing its production capabilities and reinforcing its strategic focus on quality, automation, and scalability.
Connect the Dots: How to Avoid Five Common Causes of Board Failure
09/03/2025 | Matt Stevenson -- Column: Connect the DotsBoards fail for various reasons, and because I’ve been part of the PCB industry for a long time, I’ve seen most of the reasons for failure. As part of my ongoing crusade to help designers design for the reality of manufacturing, here are five common causes for board failure and how to avoid them.
More Than a Competition: Instilling a Champion's Skill in IPC Masters China 2025
09/01/2025 | Evelyn Cui, Global Electronics Association—East AsiaNearly 500 elite professionals from the electronics industry, representing 18 provinces and municipalities across China, competed in the 2025 IPC Masters Competition China, March 26–28, in Pudong, Shanghai. A total of 114 contestants advanced to the practical competition after passing the IPC Standards Knowledge Competition. Sixty people competed in the Hand Soldering and Rework Competition (HSRC), 30 in the Cable and Wire Harness Assembly Competition (CWAC), and 24 in the Ball Grid Array/Bottom Termination Components (BGA/BTC) Rework Competition.
Indium Promotes Huang to Senior Manager, Marketing Communications
08/28/2025 | Indium CorporationWith its commitment to innovation and growth through employee development, Indium Corporation announces the promotion of Jingya Huang to Senior Manager, Marketing Communications, to continue to lead the company’s branding and promotional efforts.
Rehm Academy Expands Its Training Program
08/28/2025 | Rehm Thermal SystemsThe demands on modern industrial companies and employees continue to rise, and therefore, the topic of further education is becoming increasingly important today.