-
- News
- Books
Featured Books
- pcb007 Magazine
Latest Issues
Current IssueThe Hole Truth: Via Integrity in an HDI World
From the drilled hole to registration across multiple sequential lamination cycles, to the quality of your copper plating, via reliability in an HDI world is becoming an ever-greater challenge. This month we look at “The Hole Truth,” from creating the “perfect” via to how you can assure via quality and reliability, the first time, every time.
In Pursuit of Perfection: Defect Reduction
For bare PCB board fabrication, defect reduction is a critical aspect of a company's bottom line profitability. In this issue, we examine how imaging, etching, and plating processes can provide information and insight into reducing defects and increasing yields.
Voices of the Industry
We take the pulse of the PCB industry by sharing insights from leading fabricators and suppliers in this month's issue. We've gathered their thoughts on the new U.S. administration, spending, the war in Ukraine, and their most pressing needs. It’s an eye-opening and enlightening look behind the curtain.
- Articles
- Columns
- Links
- Media kit
||| MENU - pcb007 Magazine
Fresh Thinking on the Logistics of Laminate Distribution
January 28, 2020 | Barry Matties, I-Connect007Estimated reading time: 19 minutes
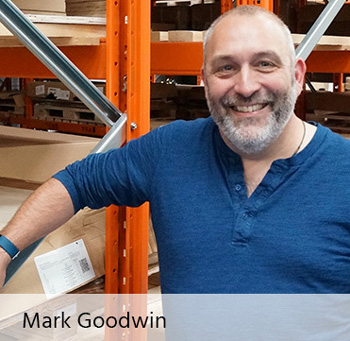
Mark Goodwin, COO of Europe and the Americas for Ventec International Group, sits down with Barry Matties to explain his approach to supply chain management, efficient distribution, and maintaining definitive product identity at every stage.
Barry Matties: Mark, I recently visited your plant in Kirchheimbolanden (“KiBo”), Germany and was very impressed with the operation from the point of view of logistics. I also had some very interesting conversations with Frank Lorentz, general manager at the facility. There’s a lot of opportunity for the whole concept of logistics in the operation that you’re running.
Mark Goodwin: In terms of logistics, this is a question of systems for us and links into traceability. There’s the physical movement of material and customer service, of course, but just as important are all of those additional benefits relating to service levels and the ability to provide detailed traceability. We have a lot of ongoing investment in our ERP system. For us, it’s a logistics management system that is all about material control. We are already barcoding all of our materials packaging on the way into our stock and on deliveries to our customers in terms of labeling, and we’re now looking at ways of physically marking the material. We already have the capability to etch a QR code onto copper and read it on a scanner or a mobile phone. And we’re going to have QR selection of material and QR control along the whole process inside Ventec with the potential for customers to use it in their own process and gain the benefits as well.
Everybody thinks the laminate business is straightforward. You have copper-clad plastic, and it gets cut up. What could be simpler? But one piece of copper-clad plastic looks much like another piece of copper-clad plastic; it could be 0.2 millimeters, 0.25, or 0.3 And when you’re handling a lot of materials, things could easily go wrong unless you have systems in place. Our objective is to move this control away from reliance on people, who are fallible, to a computer system-driven approach to ensure accuracy even when operating at a fast pace. Getting system control of material identification is key for this, but then there’s also the wider concept of product substitution and counterfeiting that goes on in the world, and controlling and proving provenance of materials throughout the supply chain into our customers warehouse, and even beyond to their customers; we’re thinking about that, too.
There have been instances where materials and components have proven to have been subject to unauthorized material substitutions or even suspected as counterfeits. With the Certificate of Conformance (C of C) paperwork, and with our records of sales and deliveries, we have full traceability, ensuring our customers can be sure when the material is delivered that it is what they requested, but this is not in anything like real-time. By the time it’s identified, it’s already a problem; we are looking at ways to change that.
Matties: I would also think that, depending on the critical nature of the end product, there has to be a thorough front-end inspection if it’s going into a high-reliability situation, for example, because you can’t have this failing.
Goodwin: Ventec works entirely with its own distribution channel. I’m sure at the point of shipping the material that we’re shipping Ventec material because we don’t have anybody else’s material.
Matties: And that’s one of the advantages of Ventec.
Goodwin: Yes, it is a huge advantage. What happens from there on, either accidentally or deliberately, we can’t control; however, we can trace back today to the point of shipment. I have that level of traceability already, without too much difficulty, but after the event. We know what we delivered, where to, and in what quantity. We need feedback on certain information to confirm this, but we can demonstrate traceability to this point with current paper-based systems. There’s work going on in IPC about material counterfeiting, but we have to be careful with that terminology in the laminate business. What does counterfeiting mean? I’m not convinced people are out there making a Ventec lookalike laminate.
Some PCB shops may say laminates are basically the same and interchange them—using IPC slash sheet numbers, for example—because they don’t have the Ventec or other manufacturers’ material in stock. I am sure this has happened historically in the FR-4 business for years, because in that business, it mostly doesn’t matter, and without using something like an FTIR scan, the OEM could not tell which manufacturers’ material was used. And if you’re dealing with one of the more professional manufacturers of FR-4, frankly speaking, everybody makes a good product.
Most of the differentiation comes down to service, logistics, price, etc. However, in the newer materials, such as IMS for thermal management and our tec-speed, high-speed, low-loss, and high-frequency product ranges, the material is a component in the system. They’re not just a physical carrier of the interconnect anymore; they are a component that delivers critical performance in the end product, and that’s where it’s becoming critical to both avoid and catch any material substitution.
We have to think about this topic and how to give people confidence. One thing you can be confident about with Ventec is if you talk to Ventec in Europe, it’s connected back to manufacturing sites in Asia with nobody in between; they’re all Ventec people. It’s a secure pipeline to market; if mistakes happen after that, it’s mostly down to process or human error. When one piece of laminate looks very much like another piece of laminate, you need to have solutions in place to help differentiate and ensure correct selection. This could be a human-readable inkjet marking at its simplest, but I am more interested in a computer-readable solution that is less easy to implement and much harder to remove than ink, so a robust, system-readable solution.
My plan is to give the customer a way of checking the physical material when they pick the stock from their inventory with computer verification, potentially including a feedback loop to our lot number database as it goes into and through their process. By removing the reliance on a paper trail, we remove reliance on operator accuracy. And for laminate, I already have a small-scale solution, which we are working to scale up.
We’re taking it one step at a time. We can do it on copper-clad material, and even unclad laminate. However, prepreg is another challenge, and the result on laminate is readable on a mobile phone, so it can be quickly checked in the field without any special equipment and is small enough not to take up too much real estate, which is a cost, of course.
Matties: That’s important.
Page 1 of 2
Suggested Items
Copper Price Surge Raises Alarms for Electronics
07/15/2025 | Global Electronics Association Advocacy and Government Relations TeamThe copper market is experiencing major turbulence in the wake of U.S. President Donald Trump’s announcement of a 50% tariff on imported copper effective Aug. 1. Recent news reports, including from the New York Times, sent U.S. copper futures soaring to record highs, climbing nearly 13% in a single day as manufacturers braced for supply shocks and surging costs.
I-Connect007 Editor’s Choice: Five Must-Reads for the Week
07/11/2025 | Andy Shaughnessy, Design007 MagazineThis week, we have quite a variety of news items and articles for you. News continues to stream out of Washington, D.C., with tariffs rearing their controversial head again. Because these tariffs are targeted at overseas copper manufacturers, this news has a direct effect on our industry.I-Connect007 Editor’s Choice: Five Must-Reads for the Week
Digital Twin Concept in Copper Electroplating Process Performance
07/11/2025 | Aga Franczak, Robrecht Belis, Elsyca N.V.PCB manufacturing involves transforming a design into a physical board while meeting specific requirements. Understanding these design specifications is crucial, as they directly impact the PCB's fabrication process, performance, and yield rate. One key design specification is copper thieving—the addition of “dummy” pads across the surface that are plated along with the features designed on the outer layers. The purpose of the process is to provide a uniform distribution of copper across the outer layers to make the plating current density and plating in the holes more uniform.
Trump Copper Tariffs Spark Concern
07/10/2025 | I-Connect007 Editorial TeamPresident Donald Trump stated on July 8 that he plans to impose a 50% tariff on copper imports, sparking concern in a global industry whose output is critical to electric vehicles, military hardware, semiconductors, and a wide range of consumer goods. According to Yahoo Finance, copper futures climbed over 2% following tariff confirmation.
Happy’s Tech Talk #40: Factors in PTH Reliability—Hole Voids
07/09/2025 | Happy Holden -- Column: Happy’s Tech TalkWhen we consider via reliability, the major contributing factors are typically processing deviations. These can be subtle and not always visible. One particularly insightful column was by Mike Carano, “Causes of Plating Voids, Pre-electroless Copper,” where he outlined some of the possible causes of hole defects for both plated through-hole (PTH) and blind vias.