-
-
News
News Highlights
- Books
Featured Books
- pcb007 Magazine
Latest Issues
Current IssueSales: From Pitch to PO
From the first cold call to finally receiving that first purchase order, the July PCB007 Magazine breaks down some critical parts of the sales stack. To up your sales game, read on!
The Hole Truth: Via Integrity in an HDI World
From the drilled hole to registration across multiple sequential lamination cycles, to the quality of your copper plating, via reliability in an HDI world is becoming an ever-greater challenge. This month we look at “The Hole Truth,” from creating the “perfect” via to how you can assure via quality and reliability, the first time, every time.
In Pursuit of Perfection: Defect Reduction
For bare PCB board fabrication, defect reduction is a critical aspect of a company's bottom line profitability. In this issue, we examine how imaging, etching, and plating processes can provide information and insight into reducing defects and increasing yields.
- Articles
- Columns
- Links
- Media kit
||| MENU - pcb007 Magazine
IPC Europe Shares Technical Education and Standards Awareness
April 22, 2020 | Pete Starkey, I-Connect007Estimated reading time: 4 minutes
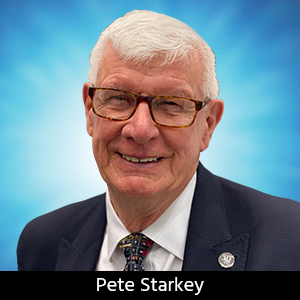
Against a background of COVID-19 uncertainty and unprecedented challenges, but recognising the vital importance of continuing to educate engineers and share the knowledge and skills required to manufacture boards and assemblies of the highest yields and reliability, the IPC Europe team hosted a technical webinar for the European electronics industry, featuring the expertise of two of I-Connect007’s regular columnists: Mike Carano and Jan Pedersen.
Introduced by Sanjay Huprikar, IPC vice president of solutions, and Philippe Léonard, director of operations IPC Europe, Carano shared some keen insights into troubleshooting and defect analysis for PCBs as VP of technology and business development for RBP Chemical Technology.
With more than 40 years in the industry and 34 years of active participation in IPC, Carano is currently co-chair of the IPC Technology Roadmap executive committee and member of the IPC Hall of Fame and recipient of the Dieter Bergman IPC Fellowship Award. He was an accomplished and skilful teacher, generously sharing a slice his encyclopaedic knowledge and experience with no hint of condescension. Carano gave a concise overview of the materials, chemical processes, and equipment parameters that impact PCB quality, focusing on defect analysis and troubleshooting.
Carano stressed that—because PCB fabrication was an integrated process involving a maze of inter-related chemical, mechanical and imaging steps—a defect might not show up in the process that caused it. As an example, a defect or process indicator that manifested itself in nickel-gold plating might have originated in the solder mask or copper plating step, so it was essential to understand the upstream and downstream processes. He explained the mechanism of the troubleshooting procedure, recommended avoiding the “head-in-the-sand syndrome,” and commented: “Troubleshooting is a science. Follow the evidence. Common sense usually applies.”
Carano briefly explained how to identify and correct the control processes that adversely affected circuit board quality, how to establish the root cause of potential defects to minimise and prevent loss of quality; how to recognise the inter-relationships of PCB materials, processes, and equipment; and how those relationships affected the quality of PCBs and assemblies. He discussed root causes and corrective actions for defects such as interconnect separation, delamination, wedge voids, plating folds, microvoids, surface pitting, and hole-wall pull-away, and also considered electrodeposition defects, solderability and assembly-related issues, such as outgassing, black pad, creep corrosion, and blow holes.
Carano covered so much ground in his 25-minute slot and 56 PowerPoint slides that I admit I struggled to take it all in. But he certainly emphasised the principles of effective troubleshooting and gave an indication of the enormity of the topic in the context of PCB fabrication and assembly. Carano’s presentation was a preview of a comprehensive distance-learning course offered by IPC, with six two-hour sessions spread over three weeks, taught by himself and utilising interactive webinars, on-demand recordings, and job-specific exercises. Details can be found on IPC’s website.
Introduced as “The Exemplary IPC Member,” PCB Norseman Jan Pedersen, senior technical advisor at Elmatica and chair of numerous standards development committees, gave an update on IPC standards development activities in Europe directed at the automotive and medical sectors. Specifically, he discussed the Automotive Applications Addendum to IPC-6012D qualification and performance specification for rigid printed boards and the IPC-6012 and 6013 Medical Addendum aimed at strengthening the reliability and consistency of PCB product qualification and acceptance for medical devices.
Pedersen explained the justification for the Automotive Addendum. Automotive electronics represented a unique combination: life-critical systems, produced in high volumes, and operating in harsh environments. The aim was to establish a globally-accepted set of reliability-related requirements. He made it clear that the addendum was intended not to be a standalone document, but to be recognised as automotive-electronics-specific requirements in addition to or in place of IPC-6012E Class 3 requirements. It was planned to launch the addendum as IPC-6012EA in the spring of 2021.
The special requirements in addition to IPC-6012 would relate to: visual examination, lifted lands after thermal stress, hole size, hole pattern and pattern feature accuracy, preconditioning before bow and twist assessment, defects along the edges of rectangular surface mount lands, wicking, hole wall separation after thermal stress, solder mask thickness, cleanliness of the delivered PCB, acceptance testing frequency, and recommended suitability and reliability testing. Pedersen gave examples of limits on lifted lands (3.3.4), AOI requirements (3.5.1 through 3.5.4.8), limits on wicking (3.6.2.1), cleanliness test methods (3.9), and frequency of process control microsections. Several other items were scheduled for discussion at the forthcoming task group web meeting.
Automotive-specific standards had also been developed for electronic assemblies. The J-STD-001/IPC-610 Automotive Addendum launched in February 2020. IPC J-STD-001GA / IPC-A-610GA combined performance requirements and acceptability in one document—a first for IPC. And IPC-9797 was defining characterisation, qualification, and acceptance requirements for compliant press-fit pin technology for the automotive and aerospace industries.
Pedersen also chaired the task group for the Medical Addendum to IPC-6012 and IPC-6013. IPC-6012 EM would be the first-ever standard for PCBs in medical devices and would provide consistency of PCB product qualification and acceptance beyond IPC Class III to demonstrate suitability for medical devices and give a high degree of assurance of the reliability and durability of the PCB. IPC-6012EM was currently at the ballot stage, with its flex and flex-rigid counterpart IPC-6013EM following closely behind it.
Traceability was fundamental to the automotive and medical sectors. A revision of IPC-1782 Standard for Manufacturing and Supply Chain Traceability of Electronic Products was currently at the ballot stage and now included traceability for printed boards in addition to the electronic production. The IPC-6012 Automotive Addendum would be linked to IPC-1782A with a requirement for traceability levels related to reliability requirements.
Pedersen’s presentation demonstrated the power of industry volunteers collaborating to solve technical challenges. And this was echoed by Sanjay Huprikar’s acknowledgement that IPC’s most important asset was its thousands of global volunteers.
It was an informative hour. Many thanks to the IPC Europe team for putting it together and for engaging two leading industry experts to deliver the content.
Testimonial
"We’re proud to call I-Connect007 a trusted partner. Their innovative approach and industry insight made our podcast collaboration a success by connecting us with the right audience and delivering real results."
Julia McCaffrey - NCAB GroupSuggested Items
MacDermid Alpha Electronics Solutions Unveils Unified Global Website to Deepen Customer, Talent, and Stakeholder Engagement
07/31/2025 | MacDermid Alpha Electronics SolutionsMacDermid Alpha Electronics Solutions, the electronics business of Elements Solutions Inc, today launched macdermidalpha.com - a unified global website built to deepen digital engagement. The launch marks a significant milestone in the business’ ongoing commitment to delivering more meaningful, interactive, and impactful experiences for its customers, talent, and stakeholders worldwide.
KOKI to Showcase Analytical Services and New HF1200 Solder Paste at SMTA Guadalajara 2025
07/31/2025 | KOKIKOKI, a global leader in advanced soldering materials and process optimization services, will exhibit at the SMTA Guadalajara Expo & Tech Forum, taking place September 17 & 18, 2025 at Expo Guadalajara, Salón Jalisco Halls D & E in Guadalajara, Mexico.
Weller Tools Supports Future Talent with Exclusive Donation to SMTA Michigan Student Soldering Competition
07/23/2025 | Weller ToolsWeller Tools, the industry leader in hand soldering solutions, is proud to announce its support of the upcoming SMTA Michigan Expo & Tech Forum by donating a limited-edition 80th Anniversary Black Soldering Set to the event’s student soldering competition.
Koh Young Appoints Tom Hattori as President of Koh Young Japan
07/21/2025 | Koh YoungKoh Young Technology, the global leader in True 3D measurement-based inspection solutions, announced the appointment of Tom Hattori as President of Koh Young Japan (JKY).
Silicon Mountain Contract Services Enhances SMT Capabilities with New HELLER Reflow Oven
07/17/2025 | Silicon Mountain Contract ServicesSilicon Mountain Contract Services, a leading provider of custom electronics manufacturing solutions, is proud to announce a significant upgrade to its SMT production capability with the addition of a HELLER 2043 MK5 10‑zone reflow oven to its Nampa facility.