-
-
News
News Highlights
- Books
Featured Books
- pcb007 Magazine
Latest Issues
Current IssueThe Hole Truth: Via Integrity in an HDI World
From the drilled hole to registration across multiple sequential lamination cycles, to the quality of your copper plating, via reliability in an HDI world is becoming an ever-greater challenge. This month we look at “The Hole Truth,” from creating the “perfect” via to how you can assure via quality and reliability, the first time, every time.
In Pursuit of Perfection: Defect Reduction
For bare PCB board fabrication, defect reduction is a critical aspect of a company's bottom line profitability. In this issue, we examine how imaging, etching, and plating processes can provide information and insight into reducing defects and increasing yields.
Voices of the Industry
We take the pulse of the PCB industry by sharing insights from leading fabricators and suppliers in this month's issue. We've gathered their thoughts on the new U.S. administration, spending, the war in Ukraine, and their most pressing needs. It’s an eye-opening and enlightening look behind the curtain.
- Articles
- Columns
- Links
- Media kit
||| MENU - pcb007 Magazine
Just Ask John Mitchell: Blurring the Lines of Technology
September 30, 2020 | I-Connect007 Editorial TeamEstimated reading time: 2 minutes
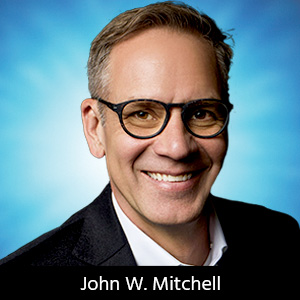
First, we asked you to send in your questions for Happy Holden, Joe Fjelstad, and Eric Camden in our “Just Ask” series. Now, it’s IPC President and CEO John Mitchell’s turn! A regular PCB007 columnist, John focuses on many of the challenges affecting the global electronics industry supply chain. Over the years, he has served as an engineer, manager, and executive at a variety of companies and organizations. We hope you enjoy “Just Ask John.”
Q: Advanced interconnection technology is blurring the distinction between circuit boards and ICs. What is IPC doing to address this trend?
A: This subject has been raised a few times over the past couple of years—the “blurring of the lines” proposal, if you will. Some examples of technical similarity include copper line/space design range overlap, high-speed laminate materials, HDI, vias/stacks, and signal integrity control, to name a few.
Currently, while there are technical similarities shared between (a) IC packaging and (b) printed circuit board assembly and test (PCBA) market segments, at IPC, we do not share this viewpoint. We think that “blurring of the lines” messaging is confusing the industry. At this time, we are not seeing a significant number of reported cases where the lines are blurring between IC packaging and PCBA. Instead, we see IC packaging and PCBA manufacturing operating as two separate, but very complementary, supply chain operation segments. While technologies may be shared, base materials, design rules, equipment sets, assembly, electrical test processes, and quality/reliability assessment requirements can be different.
It appears the driving force may be that some EMS providers are attempting to extend their service offering beyond PCBA/test to also include IC packaging assembly/test. From an EMS perspective, this is attractive because it allows them to benefit from their manufacturing infrastructure economies of scale (EOS) and offer higher value to OEMs with increased margins.
At IPC, we continue to lead and serve the electronics manufacturing industry. Our core consists of standards, education, training and certification, and government advocacy. In the future, if this migration occurs and if EMS providers offer back-end OSAT services, IPC’s network of members and standards development processes is positioned to drive new standards and technology adoption as needs arise. IPC standards can be applied to both PCBA assembly and test and IC packaging assembly. IPC “factory of the future” activities, including the connected factory exchange (CFX), are driving digital factories and modernization across the supply chain.
To submit your questions to John, click here.
Suggested Items
Trouble in Your Tank: Can You Drill the Perfect Hole?
07/07/2025 | Michael Carano -- Column: Trouble in Your TankIn the movie “Friday Night Lights,” the head football coach (played by Billy Bob Thornton) addresses his high school football team on a hot day in August in West Texas. He asks his players one question: “Can you be perfect?” That is an interesting question, in football and the printed circuit board fabrication world, where being perfect is somewhat elusive. When it comes to mechanical drilling and via formation, can you drill the perfect hole time after time?
The Evolution of Picosecond Laser Drilling
06/19/2025 | Marcy LaRont, PCB007 MagazineIs it hard to imagine a single laser pulse reduced not only from nanoseconds to picoseconds in its pulse duration, but even to femtoseconds? Well, buckle up because it seems we are there. In this interview, Dr. Stefan Rung, technical director of laser machines at Schmoll Maschinen GmbH, traces the technology trajectory of the laser drill from the CO2 laser to cutting-edge picosecond and hybrid laser drilling systems, highlighting the benefits and limitations of each method, and demonstrating how laser innovations are shaping the future of PCB fabrication.
Day 2: More Cutting-edge Insights at the EIPC Summer Conference
06/18/2025 | Pete Starkey, I-Connect007The European Institute for the PCB Community (EIPC) summer conference took place this year in Edinburgh, Scotland, June 3-4. This is the third of three articles on the conference. The other two cover Day 1’s sessions and the opening keynote speech. Below is a recap of the second day’s sessions.
Day 1: Cutting Edge Insights at the EIPC Summer Conference
06/17/2025 | Pete Starkey, I-Connect007The European Institute for the PCB Community (EIPC) Summer Conference took place this year in Edinburgh, Scotland, June 3-4. This is the second of three articles on the conference. The other two cover the keynote speeches and Day 2 of the technical conference. Below is a recap of the first day’s sessions.
Preventing Surface Prep Defects and Ensuring Reliability
06/10/2025 | Marcy LaRont, PCB007 MagazineIn printed circuit board (PCB) fabrication, surface preparation is a critical process that ensures strong adhesion, reliable plating, and long-term product performance. Without proper surface treatment, manufacturers may encounter defects such as delamination, poor solder mask adhesion, and plating failures. This article examines key surface preparation techniques, common defects resulting from improper processes, and real-world case studies that illustrate best practices.