-
- News
- Books
Featured Books
- pcb007 Magazine
Latest Issues
Current IssueInventing the Future with SEL
Two years after launching its state-of-the-art PCB facility, SEL shares lessons in vision, execution, and innovation, plus insights from industry icons and technology leaders shaping the future of PCB fabrication.
Sales: From Pitch to PO
From the first cold call to finally receiving that first purchase order, the July PCB007 Magazine breaks down some critical parts of the sales stack. To up your sales game, read on!
The Hole Truth: Via Integrity in an HDI World
From the drilled hole to registration across multiple sequential lamination cycles, to the quality of your copper plating, via reliability in an HDI world is becoming an ever-greater challenge. This month we look at “The Hole Truth,” from creating the “perfect” via to how you can assure via quality and reliability, the first time, every time.
- Articles
- Columns
- Links
- Media kit
||| MENU - pcb007 Magazine
Avishtech Introduces Latest Generation of Its Revolutionary Gauss Stack PCB Stack-up Tool
March 1, 2021 | Avishtech, Inc.Estimated reading time: 5 minutes
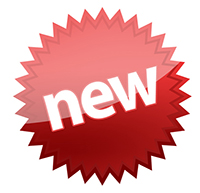
Avishtech, the leading provider of innovative EDA stack-up and 2D field solver solutions, has announced the availability of the latest version of its Gauss Stack PCB stack-up design and simulation solution. This version includes an extensive dielectric materials library that enables rapid specification and implementation of a complete stackup design that includes both electromagnetic and thermomechanical simulations, fully integrated, with no additional user input of material data required. Gauss Stack accurately predicts resin starvation and glass stop issues and provides board level thermomechanical properties including coefficients of thermal expansion in all directions—X, Y and Z axis (both above and below Tg).
Keshav Amla, Founder and CEO of Avishtech, notes, “Today’s high data rate products including 112 Gbps/channel and 5G/mmWave applications have very little ‘wiggle room.’ A slight mistake in one area can quickly render a design inoperable or unmanufacturable. Prior to this point in time, there was no EDA product that enabled a real Multiphysics approach, where product developers can carry out electromagnetic and thermomechanical simulations, manufacturability checks and reliability predictions. The process consisted of ‘best guess’ estimations that had to be verified through the building of a test vehicle board. And, if there were problems detected at the test-board level, the only solution was to go back to square one and start the process all over again. This led to time-intensive and expensive rework that could then impact critical time-to-market windows, competitive advantages and overall profitability of a product line.”
“What we have done with Gauss Stack is to effectively bridge the gap between the design and manufacturing processes,” continues Amla. “Now, instead of just applying ‘best practices’ and hoping that the PCB you design will sync up with the characteristics of the dielectric material you have selected, with Gauss Stack, you can move forward with a right-the-first-time design that meets your performance characteristics but is also manufacturable, reliable and profitable.”
The specific features of Gauss Stack include: the ability to accurately model insertion loss by accounting for ground plane losses; the accurate prediction of resin starvation and glass stops that includes the effect of dielectric filler and conductor roughness; the ability to accurately simulate the PCB thermomechanical properties that are critical for reliability predictions; the further simulation, based on these board level thermomechanical properties, of plated though-hole reliability, microvia reliability and solder joint reliability; the ability to perform simulations for the impedance and frequency and roughness dependent losses associated with dielectric materials, for the full stackup with one click; and the additional ability to perform synthesis to simulate line widths required to achieve a target impedance, again for the full stackup with one click.
Amla continues, “At the higher level, Gauss Stack enables you to predict failure modes at the stackup design stage. Prior to now, product designers weren’t able to predict how resin content, glass weave, retained copper %, and other aspects of their designs would impact the board level properties or the manufacturability and reliability of their boards. And, with today’s high-frequency, high-date rate designs, these are often the hidden ‘gotchas’ that determine whether your product will work as designed or even if the product can be successfully manufactured. Gone are the days when designing for just one attribute was sufficient.”
While numerous EDA toolsets contain massive amounts of information in the form of libraries, the ability to quantify and qualify that data in a meaningful way is not always possible. Amla explains, “But, we haven’t just built another iteration of the same mouse trap—a broad-based laminate database. Instead, we have incorporated into Gauss Stack a level of intelligence in the form of a proprietary algorithm that is able to extract detailed mechanical properties at the polymer level that are critical for the afore-mentioned thermomechanical simulations that Gauss Stack conducts. Based on these simulations it’s possible to determine how these properties will impact the design, manufacturability, long-term operability and reliability of the end product. We have done extensive validation of our predictions on several built test vehicle boards and all of our results have been within experimental error.”
Lee Ritchey, Founder and President of Speeding Edge who is widely regarded as one of the leading industry experts in PCB design, states, “Extensive and meaningful innovation in EDA toolsets is a rarity in this industry. Toolset developers might offer tweaks of their products here and there that are of some value but it’s rare that a new toolset comes on the scene that can be a real game changer. Avishtech’s Gauss Stack is such a tool. It provides insight into those material characteristics and performance metrics that can make or break a design in terms of their predictability and reliability once the product is manufactured.”
Marc Licciardi, Founder of DfX Engineering, is an early adopter of Avishtech’s Gauss Stack. He notes, “What Avishtech has built with Gauss Stack is not just an incremental change, but, rather, a fundamental shift in how I can design PCB stacks. It allows me to catch manufacturability issues like resin starvation and glass lock/glass stop, which can also cause CAF and other related issues, as well as predict the reliability of the solder joints and vias, on top of impedance and loss modeling, all at the design stage, rather than learning of these issues many months into the development process. Gauss Stack empowers me to virtually prototype several different stackups to compare them in terms of manufacturability, reliability, and signal integrity and help identify which stackup fits the right balance of requirements to take products to market faster, without having to build test vehicle after test vehicle.”
Product Availability and Delivery
Gauss Stack is available now. Instead of the traditional pricing methodologies of a toolset license per seat, Avishtech utilizes a subscription-based customer fulfillment model. Each year, an Avishtech customer buys an annual subscription, based on their design needs criteria, and all the enhancements, additions and technology advancements made to the product during that subscription period are included in the subscription price. System software requirements include: OS Microsoft Windows 10 (64 bit); Recommended CPU—64-bit Intel i7 Quad Core processor running at 4.0 GHz or better (Requirement: 64-bit Intel Dual core processor running at 3.0 GHz); Recommended memory—16 GB or higher (Requirement 8 GB or higher).
Testimonial
"The I-Connect007 team is outstanding—kind, responsive, and a true marketing partner. Their design team created fresh, eye-catching ads, and their editorial support polished our content to let our brand shine. Thank you all! "
Sweeney Ng - CEE PCBSuggested Items
Pick and Place Machine Innovator - NECTEC Launches Next-Gen SMT Line Solution With LED and X-ray Technology
08/26/2025 | Globe NewswireNECTEC PTE. LTD., a leading provider of SMT electronics manufacturing equipment, announced the official launch of its next-generation SMT solutions, featuring newly upgraded pick and place machine, specialized LED pick and place machines, enhanced Reflow Oven technology, advanced X-ray Inspection, high-speed X-ray Counter, and premium Solder Paste
MS2 Technologies, LLC/P. Kay Focuses on Central America with First Installation in Honduras
08/24/2025 | P. Kay Metal, Inc.This year MS2 Technologies has turned their focused to the growing electronics market in Central America. With that focus came the adaptation of MS2 and the Akila System from a Honduras-based corporation with manufacturing plants in both Honduras and Mexico.
BEST Inc. Provides High-Reliability BGA Reballing and Component Rework Services
08/22/2025 | BEST Inc.BEST Inc., a leader in electronic component services, is pleased to announce its component rework services are available for all types of area array devices including ball grid array, land grid array and quad flat no-lead SMT packages.
Indium Corporation Promotes Two Leaders in EMEA (Europe, Middle East, and Africa) Markets
08/05/2025 | Indium CorporationWith its commitment to innovation and growth through employee development, Indium Corporation today announced the promotions of Andy Seager to Associate Director, Continental Sales (EMEA), and Karthik Vijay to Senior Technical Manager (EMEA). These advancements reflect their contributions to the company’s continued innovative efforts with customers across Europe, the Middle East, and Africa (EMEA).
MacDermid Alpha Electronics Solutions Unveils Unified Global Website to Deepen Customer, Talent, and Stakeholder Engagement
07/31/2025 | MacDermid Alpha Electronics SolutionsMacDermid Alpha Electronics Solutions, the electronics business of Elements Solutions Inc, today launched macdermidalpha.com - a unified global website built to deepen digital engagement. The launch marks a significant milestone in the business’ ongoing commitment to delivering more meaningful, interactive, and impactful experiences for its customers, talent, and stakeholders worldwide.