-
- News
- Books
Featured Books
- smt007 Magazine
Latest Issues
Current IssueWhat's Your Sweet Spot?
Are you in a niche that’s growing or shrinking? Is it time to reassess and refocus? We spotlight companies thriving by redefining or reinforcing their niche. What are their insights?
Moving Forward With Confidence
In this issue, we focus on sales and quoting, workforce training, new IPC leadership in the U.S. and Canada, the effects of tariffs, CFX standards, and much more—all designed to provide perspective as you move through the cloud bank of today's shifting economic market.
Intelligent Test and Inspection
Are you ready to explore the cutting-edge advancements shaping the electronics manufacturing industry? The May 2025 issue of SMT007 Magazine is packed with insights, innovations, and expert perspectives that you won’t want to miss.
- Articles
- Columns
- Links
- Media kit
||| MENU - smt007 Magazine
Cleanliness Behind Many Assembly Challenges
July 2, 2021 | I-Connect007 Editorial TeamEstimated reading time: 3 minutes
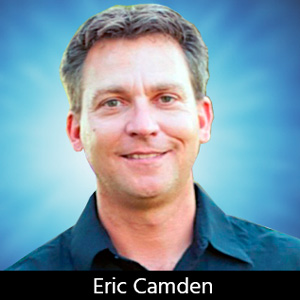
Eric Camden says nobody knows your board like you do, so it’s time for assemblers to start doing their own cleanliness testing and due diligence, and stop relying on outside organizations to determine how clean their boards need to be.
Nolan Johnson: Could you launch us into this conversation with a quick recap on yourself, your background, and a little about the company you work for?
Eric Camden: Officially I’m a lead investigator at Foresite in Kokomo, Indiana. We’re a failure analysis and reliability testing laboratory. I’ve been here 21 years, and I’ve spent the majority of my time going through other people’s processes. I’ll see a failure, or they’re trying to optimize a process in some sort of way on the assembly side of things; we will analyze that as well as going onsite to look at the equipment and processing parameters, and then determine where optimizations can be made. I’ve spent a lot of my time on improving reliability for our customers in that way, as well as failure analysis. We are an in-depth failure analysis lab with experience from all corners of the industry, from component packaging to assembly.
Johnson: What seems to be the most urgent or highest visibility issue right now?
Camden: For the past few years, miniaturization has been creeping up and overtaking reliability issues when it comes to chemistries, residues, and similar kinds of failure analysis projects. Cleanliness is still a big problem; it drives a lot of what we do around here, and when we’re looking at the changes in the IPC, what they’ve done with J-STD-001 cleanliness (where they’ve taken out the 1.56 target number for acceptability on the ROSE testing), it’s been replaced with creating your own objective evidence now. WP-019 explains how the Rhino Group came to these conclusions, and what to put in place instead of accepting that historical number. Cleanliness and reliability go hand in hand, and I don’t see it changing any time soon. And when you put miniaturization on top of that you’re just compounding your own problems.
Johnson: You were mentioning work with IPC standards to change ROSE testing and so forth. From your perspective, what’s going on there?
Camden: When you think about it on the surface, it seems pretty simple. The ROSE tester, developed by the DoD in the 1970s, was never meant to be acceptance criteria. And when you think about the material sets and the components that were being used at that time, when this go/no-go number was put together and generally accepted by a lot of the manufacturing sector—the boards were full rosin, they were being cleaned. If they were being cleaned, they were being cleaned with Freon. None of the technology has really survived as-is from the 1970s, when that criterion came out.
Over time, regarding miniaturization, as we see less ionics being allowed on the board to function properly in the field, there had to be a better way to determine what test was required for your particular board. The industry is starting to realize that all boards are not made the same. We’ve all known that, but we’ve got the failure data to tell everybody that your board is very unique. Once they decided that 1.56 number really was no longer applicable, then it was just taken out. A lot of companies were moving in that direction on their own, as they saw their left hand was holding a report that said they had met certain criteria, and in the right hand was their failure analysis report.
When you see enough of those, you can conclude that maybe this isn’t working. That Rhino Team from IPC really gives a lot of power back to the assembler: “If this is my end-use environment, I should probably do this kind of testing.” Now, it’s more of a guideline: “This is how you come to the conclusion that your boards are clean enough.” It’s the old question nobody can answer: How clean is clean enough? It depends on your end-use environment, and people are coming to accept that they must stop relying on outside organizations to determine how clean their boards need to be. Now the IPC is backing up that thought by saying, “You need to figure out how clean your boards are.” And I think that was the impetus for completely changing section 8 of J-STD-001.
To read this entire interview, which appeared in the July 2021 issue of SMT007 Magazine, click here.