-
- News
- Books
Featured Books
- pcb007 Magazine
Latest Issues
Current IssueVoices of the Industry
We take the pulse of the PCB industry by sharing insights from leading fabricators and suppliers in this month's issue. We've gathered their thoughts on the new U.S. administration, spending, the war in Ukraine, and their most pressing needs. It’s an eye-opening and enlightening look behind the curtain.
The Essential Guide to Surface Finishes
We go back to basics this month with a recount of a little history, and look forward to addressing the many challenges that high density, high frequency, adhesion, SI, and corrosion concerns for harsh environments bring to the fore. We compare and contrast surface finishes by type and application, take a hard look at the many iterations of gold plating, and address palladium as a surface finish.
It's Show Time!
In this month’s issue of PCB007 Magazine we reimagine the possibilities featuring stories all about IPC APEX EXPO 2025—covering what to look forward to, and what you don’t want to miss.
- Articles
- Columns
Search Console
- Links
- Media kit
||| MENU - pcb007 Magazine
Test and Inspection: Competitive Advantage and Cost of Doing Business
December 8, 2021 | Nolan Johnson, I-Connect007Estimated reading time: 3 minutes
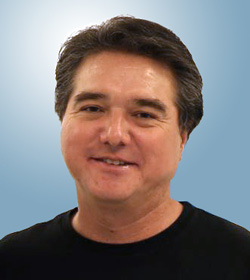
In this interview, Charlie Capers of Zentech breaks down the changing requirements he’s seeing in test and inspection in the industry, and the growing importance of investing in testing for the future growth and success of your company.
Nolan Johnson: Charlie, test strategies seem to be all over the place.
Charlie Capers: Everybody does everything a little differently. It depends on your shop, your processes, the size of your shop, and the volume of the stuff you’re doing.
Johnson: What seems to be emerging is increased activity with the IPC J-standard; the shifts in how you approach ROSE testing, in addition to the customer-driven and OEM-driven demands that are changing for testing inspection regarding finished product. This is especially true for military and medical, which are starting to demand them.
Capers: Yes. Those are the top ones.
Johnson: As you move toward automation, isn’t there an increased need for test and inspection as a part of process control?
Capers: Yes. Maybe in larger shops, I would believe that. They go hand in hand. When you collect statistics on defects, you will start to see a trend that says, for example, we’ve got a lot of shorts and opens, meaning that our solder paste process is not tight. If you’re collecting statistics and really studying them, you will see trends in your processes. It’s part of the AS9100 too; you must collect your statistical data and review it every year.
Johnson: The trick is how to make it meaningful. Turning that not just into data but into intelligence and analysis seems to be where the gap is right now.
Capers: Yes. I would agree with that. You can collect data all day long. You can look at it and see you’re having issues, but unless you dig deep and ask why the issues in this particular area or with this particular defect are there, then all the data collection is kind of useless—but we do it anyway.
Johnson: From where you sit, have you seen any interesting work to turn that into usable intelligence?
Capers: We are currently using it for our internal records, and for our requirement of AS9100. If you dig deep, you could probably say something like, “Operator number 13 is screwing up left and right.” But is it a personnel issue? Is it a process issue? Is it a machine issue? What is it? At our size, we probably have the capability, but not the resources, to dig deep into that type of stuff.
Johnson: How do you get software tools to the smaller firms, which make up the bulk of the active companies in the U.S.?
Capers: The tools are not only the software; it’s capital equipment that helps ensures your processes are good. You could have every certification in the world: plaques, trophies, and all of this, for all the good work you do. But at the end of the day, it comes down to price, and everything else is expected. After putting money into AXI, ICT, AOI, flying probe and all those good things, it would be nice to be able to recoup that money. These days, though, it’s assumed that you will be doing all these processes.
Twenty years ago, maybe you could buy an AOI machine and be able to charge for that service. For ICT and flying probe test, we must charge because there’s a development cost involved with it. For flying probe testing, you must program the machine and debug the program to make sure it runs correctly. For ICT, of course, you must program the machine, but you also must procure a test fixture to put on that machine, a bed-of-nails test fixture. There are costs involved in that. In our little world, we must pass those through. For big production, I’m sure it’s just built into the price of “we’re going to build you a million boards and this is what it’s going to cost, and we’re going to guarantee everything.” It’s a different world.
To read this entire conversation, which appeared in the November 2021 issue of PCB007 Magazine, click here.
Suggested Items
Indium’s Karthik Vijay to Present on Dual Alloy Solder Paste Systems at SMTA’s Electronics in Harsh Environments Conference
05/06/2025 | Indium CorporationIndium Corporation Technical Manager, Europe, Africa, and the Middle East Karthik Vijay will deliver a technical presentation on dual alloy solder paste systems at SMTA’s Electronics in Harsh Environments Conference, May 20-22 in Amsterdam, Netherlands.
SolderKing Achieves the Prestigious King’s Award for Enterprise in International Trade
05/06/2025 | SolderKingSolderKing Assembly Materials Ltd, a leading British manufacturer of high-performance soldering materials and consumables, has been honoured with a King’s Award for Enterprise, one of the UK’s most respected business honours.
Knocking Down the Bone Pile: Gold Mitigation for Class 2 Electronics
05/07/2025 | Nash Bell -- Column: Knocking Down the Bone PileIn electronic assemblies, the integrity of connections between components is paramount for ensuring reliability and performance. Gold embrittlement and dissolution are two critical phenomena that can compromise this integrity. Gold embrittlement occurs when gold diffuses into solder joints or alloys, resulting in mechanical brittleness and an increased susceptibility to cracking. Conversely, gold dissolution involves the melting away of gold into solder or metal matrices, potentially altering the electrical and mechanical properties of the joint.
'Chill Out' with TopLine’s President Martin Hart to Discuss Cold Electronics at SPWG 2025
05/02/2025 | TopLineBraided Solder Columns can withstand the rigors of deep space cold and cryogenic environments, and represent a robust new solution to challenges facing next generation large packages in electronics assembly.
BEST Inc. Reports Record Demand for EZReball BGA Reballing Process
05/01/2025 | BEST Inc.BEST Inc., a leader in electronic component services, is pleased to announce they are experiencing record demand for their EZReball™ BGA reballing process which greatly simplifies the reballing of ball grid array (BGA) and chip scale package (CSP) devices.