Estimated reading time: 5 minutes
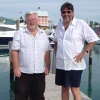
Bleeding Edge: Improved Reliability of PCBs for the Automotive Industry
With today's ever-increasing overload of electronic accessories and control modules installed in a typical family sedan, the demand on cars' wiring and imbedded printed circuits is passing a critical point, resulting in reduced reliability. Manufacturers actively compete over longer warranties to improve market percentages and suffer the associated costs involved in the repair of such long guarantees. The typical printed circuit, by virtue of its construction and manufacturing methods, is hard-pressed to survive 100% for 10 years in the extremely demanding environment of an automobile. This means that the manufacturer will have understood and predicted some expensive electronic-repair costs to absorb in the future.
The North American automobile is required to operate reliably in Northern Canada and Alaska, where it is not uncommon for temperatures to fall to -55*F or lower at night, or in Death Valley, California, where daytime temperatures can reach 120*F. The engine bay and passenger compartment--areas where many of the printed circuits are located--heat up rapidly. Each start-and-run episode is equivalent to a small thermal cycle. With enough exposure to even slight temperature changes, the vias in the printed circuit card can start to fail and open.
The same problem occurs when a car is left sitting in the sun in Phoenix, Arizona. The temperature inside the car can easily exceed 160*F. The car is then started; the A/C runs flat out, cooling the poor, overheated driver and heating the engine bay electronics even further, and another thermal cycle is created.
The mechanicals of a printed circuit board that cause via failures after a series of thermal cycles are related to the coefficient of expansion differences between the laminate and the copper in the holes. As the laminate heats up (or cools down), the expansion rate of approximately 14-20 millions per-degree-F/per inch exceeds the 12 millions per-degree-F/per inch of copper. Over time and numerous thermal cycles, the expansion difference slowly pulls apart the copper hole-to-trace joint, or, in the case of a multilayer, the inner-hole wall to inner trace. The matter becomes even worse when the temperature exceeds the T/G or glass transition temperature of the laminate, at which point the material becomes soft and plastic-like. The normal 20 PPM expansion rate quickly rises to 10 times higher, really stressing the copper plating. Unfortunately, the copper's expansion rate is unchanged by this temperature rise, which greatly increases the difference between the two materials, speeding up the destructive process. The T/G temperature is exceeded during solder reflow, assembly soldering and (sometimes, but hopefully not) during operation. The destructive nature of extreme temperature cycling will tear apart even the best normal-process-built boards on low-cost 130 T/G Fr4 after only 120 to 200 cycles. New materials are appearing, which limit the Z-axis expansion of Fr4 and therefore extend the number of thermal cycles but are too expensive for production automobile use. Printed circuits utilizing higher-temperature materials such as 175 T/G Fr4 have extended the thermal cycles to around 300 to 400 but at an increased cost.
During an experiment with a new method of plating copper, the R&D team at Sierra Proto Express was trying to solve a different printed circuit manufacturing problem when we noticed that the method resulted in a higher strength of the plated copper. The resistance of a 100-via in-series test coupon was 30% less than a normal plated hole.
We were very impressed when the first high-reliability solder float test coupons showed zero damage, even after 20 solder float cycles. Over the year we experimented, we played with and pushed the technology to result in an Fr4 printed circuit board that was virtually indestructible. The new Hi.Rel. board could take 20 to 30 solder cycles without damage and was then able to survive well over 2000 thermal cycles. Because the expansion and T/G of the laminate do not dominate or control the new High Reliability board's ability to survive thermal cycles, it is able to survive very high temperatures without damage, resulting in a new high-reliability manufacturing method for lead-free printed circuits.
During in-house qualifying and testing at Sierra, samples were sent to IRTS (Integrated Reliability Test Systems, Inc.) for thermal cycle testing and evaluation. Samples were manufactured using the HATS test CAD data coupon. The samples were 100 vias in series with four nets per sample. Thirty-six samples of different T/G Fr4 material were made and tested, resulting in 144 nodes of test. Normally processed control boards were inserted in the test system to ensure correlation back to a known cycle ability. The samples were assembly solder float-simulated by six oven cycles for 30 seconds at 260*C. The samples were then cycled in the HATS test chamber, with a low temperature of -40*C and a high temperature of 145*C. The resistance was measured after each cycle and plotted. If the resistance exceeded a change of 10% of its original value, the sample was considered failed and marked as such.
The HATS unit is a controlled-air-temperature cycling machine with a quick cycle that has been receiving great reviews in the market. The improved ability to control the test chambers and sample temperature and cycles makes the HATS tester service in high demand.
The samples were taken off at 2000 cycles because they had been on test for 13 days and the machine was needed for other jobs. All but one of the Hi. E. R. samples survived at least 1800 cycles, and most showed no increase (<2%) over 2000 cycles and, subsequently, were considered not to have changed with continued testing. One failed net on one sample resulted from the assembly of the connector onto that net but not the vias. The samples of the other three nets all survived 2000 cycles with no degradation.
Red line is normal 6-layer printed circuit via. Black lines are Hi. Rel. vias.
During conversations with Tim Estes at IRTS, he stated that he would only expect 120 to 250 thermal cycles for a .062-thick, low 135 T/G Fr4. His new HATS tester certified that Sierra's new Hi. Rel. boards survived close to or exceeded 2000 cycles.
This new technology is perfect for the low-cost automotive and lead-free market. Very-long-life Hi. Rel. printed circuit boards will vastly improve electronic life expectancies in tough environments.
Robert Tarzwell is Director of Technology at Sierra Proto Express.
Ken Bahl is the CEO of Sierra Proto Express.
More Columns from Bob and Me
Controlled Impedance: A Real-World Look at the PCB SideBob and Me: The Key to Increasing Quality - Bribe Your Employees
Bob and Me: Tarzwell's First--and Last--Lean Meeting
Bob and Me: A PCB Potpourri
Bob and Me: Spacing is Irrelevant Below 270 Volts
PCB 101: Coefficient of Thermal Expansion
The Bleeding Edge: Serious as a Heart Attack
PCB101: Fabricating High-Voltage Boards