-
- News
- Books
Featured Books
- pcb007 Magazine
Latest Issues
Current IssueInventing the Future with SEL
Two years after launching its state-of-the-art PCB facility, SEL shares lessons in vision, execution, and innovation, plus insights from industry icons and technology leaders shaping the future of PCB fabrication.
Sales: From Pitch to PO
From the first cold call to finally receiving that first purchase order, the July PCB007 Magazine breaks down some critical parts of the sales stack. To up your sales game, read on!
The Hole Truth: Via Integrity in an HDI World
From the drilled hole to registration across multiple sequential lamination cycles, to the quality of your copper plating, via reliability in an HDI world is becoming an ever-greater challenge. This month we look at “The Hole Truth,” from creating the “perfect” via to how you can assure via quality and reliability, the first time, every time.
- Articles
- Columns
- Links
- Media kit
||| MENU - pcb007 Magazine
Estimated reading time: 2 minutes
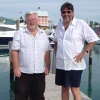
PCB101: Fabricating High-Voltage Boards
You're sitting at your desk when the phone rings. It's a customer who needs a PCB that can take 20,000 volts. Would you know how to build such a board?
First things first: You cannot just say, "Well, I think FR-4 will work." It won't, and the board will fail. Boom!
For high-voltage boards like this, special attention must be paid to the material and its specifications. FR-4 has an initial dielectric rating of 800-900 volts per mil, but due to aging effects, a more realistic value is only 300 volts. The volts-per-mil rating describes a breakdown condition in volts for each mil, or one thousandth of an inch.
If your design calls for a spacing of 10 mils between layers, then the aged voltage rating would mean the FR-4 could withstand 10 times 300, or 3,000 volts. So your 20,000 volt circuit would arc over and blow up.
There's that boom again!
The manufacturing process used in high-voltage circuits is essentially the same as that for a normal printed circuit. There are, however, differences in the materials used and the properties of those materials. First, you need to pick a material that will have a high enough voltage rating. High-voltage polyimide film (HVPF) has a 3,000 volt-per-mil rating, so a PCB layer 10 mils thick could withstand 30,000 volts. This is more than high enough to successfully build your 20,000 volt circuit.
Medium-voltage boards are typically 600 to 3,000 volts. Great care must be taken when selecting FR-4 types or a BT epoxy base materials, along with the subsequent processing, as this voltage can easily support arcs and corona.
An arc-over occurs when voltage jumps from one conductor to another. Boom! The corona is the blue glow emitting from high-voltage systems; when you walk under a high-voltage power line, the corona is the crackling, hissing sound you hear. Corona is a destructive force that destroys epoxy by ripping apart the bonds between epoxy particles, thus destroying the circuit's insulating value. Boom!
High-voltage boards of 3,000 volts to a maximum limit of about 100 kilovolts are limited to HVPF, Teflon and in some cases BT epoxy. These require a serious effort by the designer to test and finesse the design to eliminate corona, field strengths and arc-overs.
Customers need higher-voltage PCBs for many reasons. When a circuit board is used in outer space or high-altitude airplanes, the low air pressure cause the voltage to arc over at four times the "normal" voltage. So, a PCB design that requires a 2,000 volt rating at sea level would need at least an 8,000 volt rating in outer space. Many lasers use power supplies in the 5,000-10,000 volt range, which requires a very special PCB. And universities and R&D facilities use very high-voltage power supplies for experimenting with particle colliders.
Outer space brings its own issues; PCBs that outgas in this vacuum will contaminate the other critical components of the spacecraft. There are special manufacturing techniques used to make low-outgassing PCBs specifically for use in PCBs in space. We'll cover that in a future column.
Bob Tarzwell is CEO and founder of DMR Ltd. He can be reached at rtarzwell@megadawn.com. HVPF is a DMR Ltd. technology.
More Columns from Bob and Me
Controlled Impedance: A Real-World Look at the PCB SideBob and Me: The Key to Increasing Quality - Bribe Your Employees
Bob and Me: Tarzwell's First--and Last--Lean Meeting
Bob and Me: A PCB Potpourri
Bob and Me: Spacing is Irrelevant Below 270 Volts
PCB 101: Coefficient of Thermal Expansion
The Bleeding Edge: Serious as a Heart Attack
New Column: PCB 101