-
-
News
News Highlights
- Books
Featured Books
- pcb007 Magazine
Latest Issues
Current IssueSales: From Pitch to PO
From the first cold call to finally receiving that first purchase order, the July PCB007 Magazine breaks down some critical parts of the sales stack. To up your sales game, read on!
The Hole Truth: Via Integrity in an HDI World
From the drilled hole to registration across multiple sequential lamination cycles, to the quality of your copper plating, via reliability in an HDI world is becoming an ever-greater challenge. This month we look at “The Hole Truth,” from creating the “perfect” via to how you can assure via quality and reliability, the first time, every time.
In Pursuit of Perfection: Defect Reduction
For bare PCB board fabrication, defect reduction is a critical aspect of a company's bottom line profitability. In this issue, we examine how imaging, etching, and plating processes can provide information and insight into reducing defects and increasing yields.
- Articles
- Columns
- Links
- Media kit
||| MENU - pcb007 Magazine
Taiyo: Reopening Europe for Solder Mask
December 19, 2022 | Nolan Johnson, I-Connect007Estimated reading time: 10 minutes
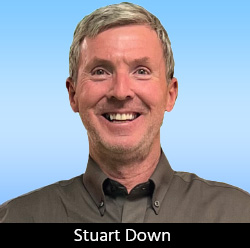
Nolan Johnson and Stuart Down discuss Taiyo’s partnership with Ventec and how both companies are leveraging their expertise to blaze a trail into the European PCB market. Down shares his outlook on the market and the unique challenges posed by global political instability and supply chain constraints, as well as how Europe’s evolving chemical regulations have impacted solder mask formulation. With their sights set on ramping up manufacturing capabilities, Taiyo sees a secure path forward to establishing a sizeable market presence in this promising region.
Nolan Johnson: Stuart, you’ve been in the industry for quite some time, but you’ve got a new role.
Stuart Down: Yes, it’s hard to leave this industry. I started in the UK PCB industry back in the 1980s, believe it or not. That’s where I grew up. And then in the mid-1990s I moved more into the supply chain side, specifically the solder mask side of the business—functional fluids, some people would call it. I’ve been very lucky in my career and traveled and worked all over the world; I’ve lived in Europe, Asia, North America selling and supporting ink technologies. Then the stars aligned last year for my return to the UK. Taiyo were looking for someone to support both their team and their growing business in Europe and I wanted to move home after being away for 20 plus years, so we came to an agreement which I hope is a win-win for both sides.
Johnson: You’re back in Europe on your home turf. What’s happening in Europe right now?
Down: There’s a lot going on with Taiyo; we have a new partner in Ventec. Taiyo has never exhibited at electronica before. It was through our new partnership with Ventec that we’re here today on this spectacular joint branded booth. Our collaboration with Ventec follows the ethos of Taiyo as a company in both Asia and North America, where we have very strong market positions. We all know that OEM drawings/specification dictate what materials goes into a PCB; if your name is on the drawing, it defaults to the PCB supplier. Leveraging that fact as a marketing strategy has been successful for Taiyo Inc all over the world, which is why we’re here now in Europe at electronica, the largest OEM exhibition in Europe.
Johnson: Your goal is to ramp up that specification and its adoption?
Down: Yes, Taiyo have always had a presence in Europe. It’s an important market for everybody, but I think this is more of a pioneering effort now. I’m here; I have a history here. We have Bernhard Schmuki who heads up our technical support in Europe. Bernhard came to us from Dyconex so has a very strong PCB background. We’ve got another well-known industry guy starting in February next year. By Q1 2023, we’ll have three direct Taiyo people in Europe; we’re building our team to support our growth here. This is a growing market for us now. I think that Taiyo’s stronger regional support has allowed us to be more successful. When I was working in the UK trying to support North America, making that happen was very difficult with time zones and physical distance. The emphasis, time, and energy Taiyo is putting into supporting Europe will help us build on the success we’ve already had.
Johnson: Talking to an OEM often means including technical details for specification and the like—that’s essential to overall business development. What dynamics are you seeing from the business development perspective in Europe as you’re reengaging with the region?
Down: Adjusting to new European regulations has taken some time. Having lived and worked in North America for so long REACH wasn’t on my day-to-day radar so coming back to the UK has meant refamiliarizing myself with REACH regulations. Taiyo has REACH-compliant products, but the SVHC part of REACH is very difficult for ink suppliers. Some of the raw materials that are about to be restricted in Europe are base materials used in inks for decades so sourcing alternatives was a challenge.
All the competitors and ink guys are trying to figure out a way around this challenge. Conveying that to the OEMs has been tricky. A PCB manufacturer will present us with a drawing that uses ink from Taiyo Asia, which you can’t sell into Europe—it doesn’t comply with regulations. In a situation like that, you have to say to the OEM, "I’m sorry, we can’t use this ink in Europe, but you can use these alternatives—which, of course, aren’t on the drawing." Getting that sorted out means going through the whole reapproval process, which can be a challenge.
Johnson: Can you specify which chemicals are problematic?
Down: I can, keep in mind I’m not a chemist but one is TGIC ion adhesion promotor, and other key one is I-907 which is a photo-initiator. TGIC has been restricted for many, many years. But the photo-initiator is a key base material found in a lot of inks and from what we understand is going to be restricted very soon. Trying to re-engineer the products around that has been a challenge. We have to explain to the OEMs that even though they’ve already approved an ink that’s been available for the past 20 years, they can’t use it now. They’ll say, “We want this ink,” and we have to come back and say, “I’m sorry, it doesn’t comply. These are your options”
Johnson: How do you do the kind of outreach necessary to educate OEMs on this issue?
Down: Well, that comes from the technical department at Taiyo—they’re on speed dial to all these OEMs. We have a global technical group that meets every month to analyze what each separate OEM wants, as well as the different requirements for different regions. There are regulations, as we just discussed, but there are also different colors of green, and finishes for each region—believe it or not it’s not the Henry Ford model. There are shades of green and finishes of green, and each area likes a different color green. Europe tends to like a matte finish, while Asia tends to like a glossier finish. North America is somewhere in between. These are the kinds of considerations we have to make. People think solder mask is just a green coating, but there is a lot of technology that goes into it.
Johnson: That’s a lot of different product flavors. What did you bring to the electronica show floor?
Down: There’s three products that we wanted to promote here at the show. First, we have a new thermal dissipation product called ThermoCool, which removes heat from both the inner layers and the surface of the circuit board. This is both a via fill product and a gap fill product, and it sucks heat away from the board. It’s very good for automotive and high heat environment circuit boards. This will be a family of products in 2023 to address different requirements and applications.
The other one is inkjet, which is a massive thing at Taiyo. Now, it may not necessarily have the heat capabilities of a standard solder mask, but Taiyo is very invested in digital application. I think inkjet is up and coming; it has the potential to be a part of all our futures. There’s been some improvements in technology and in application; I think we’ll be in a place soon where inkjet is widely considered to be a viable option. And we have solder mask inkjet in the market in production every day in Europe. We’re anticipating that by Q1 next year, the first digital factory will open in North America, and Taiyo inks will be supporting that factory from day one.
We see inkjet as the next big thing, but adaptation has been very slow. I’ve been in and around manufacturing circuit boards for many years, so I can understand why the industry is slow to move. For example, we don’t yet have colored inkjet. Customers always ask, “What we are going to do about colors?” We will get there; it’s not IF anymore, it’s when.
Johnson: Are the inks up to the task?
Down: Yes, for a circuit board’s fundamentals—like IPC-SM840-E spec, these inks will pass that spec. We’re working with one customer whose spec is way up there; we can’t get close to it yet. But they’ve given us that target because that’s where they want to be, and Taiyo wants to get them there. As far as IPC is concerned, it passes IPC-SM840E. But additive is the future. We’ve seen it in printed electronics—additive is the future now. You’ve got this huge piece of copper and you’re throwing 99% of it away? Honestly, how antiquated is that? In this day and age, digital is the new frontier.
Johnson: How has it been working with Ventec?
Down: It’s been great. When we started the partnership with Ventec, it was a baptism by fire, to be honest with you. Not the relationship itself, of course, but we started our partnership during COVID. When we started with Ventec, the world was on fire. Ventec’s logistics expertise has been an incredible help; it’s the expertise we needed then and now. The inks are coming from Japan, Korea, and North America, and these guys are used to that, so they’ve been a massive help to us. And they’ve got a similar business ethos to us, too. They’re really good—a great partner.
Johnson: What’s Taiyo bringing to the Ventec side?
Down: Well, of course a globally recognized leading brand name helps and the products we have this year have more to do with high heat capability and removal of heat from PCB’s. We have a new product called ThermoCool as we mentioned before, which has been designed to remove heat from both inner layers and build up layers, either through via fill or on the surface as a gap fill. This will actually draw heat from the circuit board and dissipate it into the environment. Ventec have a very good range of laminates aimed at the automotive market so dealing with these stresses is day to day for them.
Johnson: So, whenever Ventec is working with a challenging customer to get heat removed…
Down: Yes, this is where the synergies align. They have substrates that can do that, but we have a functional paste in ThermoCool that can do it or can help emphasize their substrate—whatever they need. So yes, it doesn’t entirely address the issue, but it’s helping because heat is going to be a big problem as we move forward with EVs and hybrids.
Johnson: And there are so many requirements to synchronize the performance characteristics for all the components that make up the board itself; each component—including solder mask—is now a functional part of how everything performs.
Down: We all know the technology in cars is incredible and how many circuit boards are required per car. And we’re all hearing about the chip shortage—that’s why we can’t go out and buy a new car anymore. It’s all interrelated. One of our big things this week is promoting our ThermoCool and high heat tolerant solder masks like our PSR-4000 HH01XR and CC01SE ranges as a solution to try and tolerate and dissipate some heat from circuit boards.
Johnson: Where do you expect to be in the European region in 12 to 18 months?
Down: I think the Taiyo team will continue to grow. I like to think that we’ll have some sort of manufacturing capability in Europe in the next 12-18 months. In my experience on the supply side, you have to manufacture in a region if you want to be successful there. It’s part of how Taiyo Inc have become the global leader in solder mask technology and supply. Up to a certain level, you can be successful importing, but these days you have to manufacture in the region. I think the shorter supply chain is key; a lot of people are running into issues getting products in from Asia plus the additional costs of course. The issues we’re dealing with right now with the global politics and the conflict in Europe are real problems on many levels, of course, a short supply chain within the region is key, so I think Taiyo have to think about that and keep our focus on local manufacturing capability in the near future
Johnson: Thanks for talking with us.
Down: Thank you for the time. I’m glad we finally got the chance to meet.
Testimonial
"Our marketing partnership with I-Connect007 is already delivering. Just a day after our press release went live, we received a direct inquiry about our updated products!"
Rachael Temple - AlltematedSuggested Items
MacDermid Alpha Electronics Solutions Unveils Unified Global Website to Deepen Customer, Talent, and Stakeholder Engagement
07/31/2025 | MacDermid Alpha Electronics SolutionsMacDermid Alpha Electronics Solutions, the electronics business of Elements Solutions Inc, today launched macdermidalpha.com - a unified global website built to deepen digital engagement. The launch marks a significant milestone in the business’ ongoing commitment to delivering more meaningful, interactive, and impactful experiences for its customers, talent, and stakeholders worldwide.
KOKI to Showcase Analytical Services and New HF1200 Solder Paste at SMTA Guadalajara 2025
07/31/2025 | KOKIKOKI, a global leader in advanced soldering materials and process optimization services, will exhibit at the SMTA Guadalajara Expo & Tech Forum, taking place September 17 & 18, 2025 at Expo Guadalajara, Salón Jalisco Halls D & E in Guadalajara, Mexico.
Weller Tools Supports Future Talent with Exclusive Donation to SMTA Michigan Student Soldering Competition
07/23/2025 | Weller ToolsWeller Tools, the industry leader in hand soldering solutions, is proud to announce its support of the upcoming SMTA Michigan Expo & Tech Forum by donating a limited-edition 80th Anniversary Black Soldering Set to the event’s student soldering competition.
Koh Young Appoints Tom Hattori as President of Koh Young Japan
07/21/2025 | Koh YoungKoh Young Technology, the global leader in True 3D measurement-based inspection solutions, announced the appointment of Tom Hattori as President of Koh Young Japan (JKY).
Silicon Mountain Contract Services Enhances SMT Capabilities with New HELLER Reflow Oven
07/17/2025 | Silicon Mountain Contract ServicesSilicon Mountain Contract Services, a leading provider of custom electronics manufacturing solutions, is proud to announce a significant upgrade to its SMT production capability with the addition of a HELLER 2043 MK5 10‑zone reflow oven to its Nampa facility.