Estimated reading time: 6 minutes
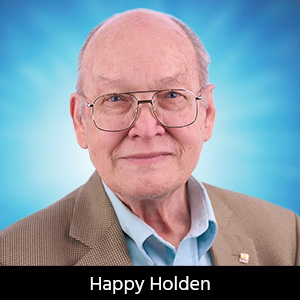
Contact Columnist Form
Happy’s Tech Talk #15: Printed Electronics Using Flex
Introduction
The printed electronics sector is presently an area of great interest to many in the electronics manufacturing industry. Because of their incredible utility, printed electronics (PE) are poised to generate tens of billions of dollars in the coming years. Recent research indicates that the total market for printed, flexible and organic electronics will grow from $41.2 billion in 2020 to $74 billion in 20301.
The term “printed electronics,” with its relatively recent appearance in the industry’s lexicon, may seem to refer to electronic circuits comprised of conductors and various active and passive components (i.e., transistors, resistors, capacitors) printed directly onto a substrate of some type. According to this definition, printed electronics are clearly a significant departure from traditional approaches to electronics manufacturing. However, marketers are trying to position a host of manufacturing solutions under the “printed electronics” umbrella to take advantage of the growing buzz surrounding the technology, which has created confusion around the term.
This confusion may be a factor in the sector’s slow growth rate. While there is presently a market for these devices, the growth rate predicted by exuberant market forecasters has not yet been realized. Barriers to exponential growth seem to be related to the current inability of suppliers to reduce costs to enable large-scale manufacturing of printed electronics. Every disruptive technology that has sought to surpass existing, highly competitive, and/or traditional technologies has faced this challenge. So far, printed electronics have replaced some existing applications but have made little progress in creating new applications outside of radio-frequency identification (RFID) and organic light-emitting diodes (OLEDs). The latter is a true printed electronics solution that has successfully established a solid market presence. Other than that, no real “killer” app or paradigm shift technology has emerged from the current fray. The simple reality is that it’s especially challenging to displace incumbent products with entirely new design solutions that must first be developed, understood, and implemented.
Applications
Disposable electronics that can compete with paper are a compelling and intriguing prospect to marketers. However, before fully adopting this technology, we must consider the environmental impact of throw-away electronics and adequately prepare for end-of-life matters. Assuming that these factors are taken into consideration, there are a variety of intriguing prospects and processes being suggested for the next generation of printed electronics.
Further, thanks to its ability to rapidly print multiple conductive, insulating, and semiconductor layers to form electronic circuits, printed electronics technology offers the ability to produce a simpler and larger integrated circuit (IC) at a much lower cost than using conventional fabrication methods, albeit with less functionality per unit area.
The number of potential applications for printed electronics technology is growing:
- RFID/tags
- Appliances/keyboards
- Photovoltaic
- Display
- Memory
- Sensors
- Lighting
- Product packaging
- Wearables
- Interconnects
- Security
Printing Methods
Deciding which printing method to use is determined by both the requirements of the printed layers and the properties of the printed materials, as well as the product’s economic and technical considerations. Presently, printing technologies are divided between sheet-based and roll-to-roll-based approaches. Sheet-based techniques, such as inkjet and screen printing, are best for low-volume, high-precision work. Gravure, offset, and flexographic printing are more common for high-volume production, such as for solar cells, reaching 10,000 square meters per hour (m²/h). While offset and flexographic printing are mainly used for inorganic and organic conductors (the latter also for dielectrics), gravure printing is especially suitable for quality-sensitive layers, like organic semiconductors and semiconductor/dielectric-interfaces in transistors, due to its high layer image registration quality. Gravure printing is also suitable for inorganic and organic conductors in terms of high resolution. Organic field-effect transistors and integrated circuits can be wholly prepared using mass-printing methods.
Altogether, there are presently eight key manufacturing image transfer technologies that are either being employed or are proposed for printed electronics production (Figure 2).
Traditional printing technologies:
- Screen printing
- Rotogravure printing
- Flexographic printing
- Offset printing
New wave printing technologies:
- Inkjet printing
- R2R photolithographic
- Plasma printing
- Direct laser imaging or ablation
Of these enabling technologies, screen printing has been around the longest and is still widely used in production today. Membrane switch technology, part of the printed electronics family, heavily relies on screen printing to make products. Technical details are shown in Table 1 for speed, resolution, film thickness, and ink viscosity.
Base Materials and Inks
Printed electronics uses flexible substrates, which lowers production cost and allows fabrication of mechanically flexible circuits. While inkjet and screen printing typically imprint rigid substrates like glass and silicon, mass printing methods almost exclusively use flexible foil and paper. Additional substrate alternatives include polyethylene terephthalate (PET), a common choice due to its low cost and higher temperature stability; polyethylene naphthalate (PEN); polyether ether ketone (PEEK), a colorless organic polymer thermoplastic used in engineering applications; and polyimide (PI) foil. Paper’s low cost and manifold applications make it an attractive substrate, but its roughness and absorbency make it problematic for electronics. Low roughness and suitable wettability, which can be tuned pre-treatment (coating, corona), are important criteria for substrates (Table 2).
Organic and inorganic materials are both used for printed electronics. Ink materials must be available in liquid form for solution, dispersion, or suspension. They must function as conductors, semiconductors, dielectrics, or insulators. Material costs must be appropriate for the application.
Most of the attention given to materials has appropriately centered on conductive inks, especially silver. Silver is the most conductive commonly used metal for making circuit conductors. Membrane switch circuits, which operate at relatively high voltages and low currents, have been printed onto polyester base materials using silver inks for more than a few decades. The challenge has been getting these circuits to have the bulk conductivity associated with copper. Common inks have conductivities that hover around 10% of copper and are not generally suitable for higher performance applications that operate at lower voltages or may require more power. Several suppliers have attempted to address this problem by using a combination of new formulations of binders in the ink and nanoparticle silver; so far, results are promising. Table 3 shows materials and inks used in printed electronics.
Conclusions
Flexible materials are a key characteristic of printed electronics. Many products traditionally utilize glass to protect the active layers. To replace glass, the flexible substrates need to be an effective barrier against oxygen and water vapor, be sufficiently strong not to rip or tear and, if a cover, transparent to visible light. Many plastics, such as such as Mylar, polyimide, PET, and ORMOCER have these characteristics. Substrates can even be papers and paper hybrids.
Table 4 shows the suitability of various base materials to printed electronics applications. Important to the growing ranks of suitable substrate materials is “photonic soldering,” a new technology pioneered by NovaCentrix in their PulseForge product line, which allows standard lead-free solder pastes to be soldered without heating the flexible base materials; this unique ability enables metallic inks to be sintered/cured without damaging the substrates2.
References
- “Flexible, Printed and Organic Electronics 2020–2030: Forecasts, Technologies, Markets,” IDTechEx.com.
- “Chapter 11: Printed Electronics,” by Joe Fjelstad, Flexible Circuit Technology, 4th Edition.
- “Photonic Soldering,” by Happy Holden, PCB007 Magazine, Dec. 20, 2021.
Resources
See “A Review of the Opportunities and Processes for Printed Electronics (Part 1),” by Happy Holden, a white paper originally published for SMTA International
Happy Holden has worked in printed circuit technology since 1970 with Hewlett-Packard,?NanYa?Westwood, Merix, Foxconn, and Gentex. He is currently a contributing technical editor with I-Connect007, and the author?of?Automation and Advanced Procedures in PCB Fabrication, and?24 Essential Skills for Engineers.?To read past columns, click here.
This column originally appeared in the December 2022 issue of Design007 Magazine.
More Columns from Happy’s Tech Talk
Happy’s Tech Talk #42: Applying Density Equations to UHDI DesignHappy’s Tech Talk #41: Sustainability and Circularity for Electronics Manufacturing
Happy’s Tech Talk #40: Factors in PTH Reliability—Hole Voids
Happy’s Tech Talk #39: PCBs Replace Motor Windings
Happy’s Tech Talk #38: Novel Metallization for UHDI
Happy’s Tech Talk #37: New Ultra HDI Materials
Happy’s Tech Talk #36: The LEGO Principle of Optical Assembly
Happy’s Tech Talk #35: Yields March to Design Rules