-
- News
- Books
Featured Books
- smt007 Magazine
Latest Issues
Current IssueWhat's Your Sweet Spot?
Are you in a niche that’s growing or shrinking? Is it time to reassess and refocus? We spotlight companies thriving by redefining or reinforcing their niche. What are their insights?
Moving Forward With Confidence
In this issue, we focus on sales and quoting, workforce training, new IPC leadership in the U.S. and Canada, the effects of tariffs, CFX standards, and much more—all designed to provide perspective as you move through the cloud bank of today's shifting economic market.
Intelligent Test and Inspection
Are you ready to explore the cutting-edge advancements shaping the electronics manufacturing industry? The May 2025 issue of SMT007 Magazine is packed with insights, innovations, and expert perspectives that you won’t want to miss.
- Articles
- Columns
- Links
- Media kit
||| MENU - smt007 Magazine
Taking Charge of ESD
April 25, 2023 | Barry Matties, I-Connect007Estimated reading time: 11 minutes
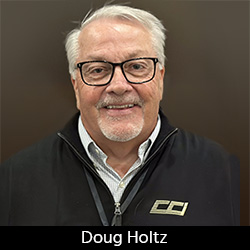
At the recent SMTA Boise Expo & Tech Forum, Barry Matties spoke with Doug Holtz, national sales manager of Conductive Containers, about challenges related to ESD and where manufacturers are most vulnerable. It’s a growing concern, Doug says, and there are important lessons to be learned. Doug also reviews his presentation, and he points out how reducing touchpoints in the supply chain can make a world of difference for both customers and manufacturers.
Barry Matties: Please tell us about your company and what you do.
Doug Holtz: We’re known as the company that invented the black box. In the early days of computers, it was discovered that static electricity was causing catastrophic failure in electronic circuitry. The industry needed some way to control this and, by creating a Faraday cage out of packaging, it led to the inception of our company. We are charter members of the ESD Association.
We've since ventured into different exotic materials, such as thermoforming, plastics, and injection molding. We stay on the cutting edge. As the industry requirements change, as components get more sensitive, and as manufacturing becomes more automated, it creates a need to see things differently. Handling in a manufacturing facility was primarily manual, and now we use robots, pick-and-place machines, and different criteria for clean room manufacturing. It’s a fluid situation. We're a company that ebbs and flows with the industry, and we've created solutions that have become standard practices in the ESD world.
Matties: You gave a presentation here at the SMTA Boise Expo and mentioned that you really need to understand the environment that you’re manufacturing in. Please tell us a little more about that.
Holtz: We covered some basic best practices to control ESD within your environment. There are a lot of different ways to implement it; it's not complicated. We talked about relative humidity within a manufacturing environment, that it's nothing we can control through packaging or handling, but it helps to look at the problem of ESD. In the past, we had to tell customers that ESD was a problem for their procedures. While they now accept that it’s an issue, they still don’t understand where it comes from or how to control it. Just a couple of basic practices will take your ESD program from a baseline to a much higher level.
Understanding humidity is something people can relate to. The ESD Association has guidelines for testing raw materials and how they need to be conditioned. We have to condition that material based on a relative humidity and this sets the stage, ironically. When it's humid, we sweat. So, you condition the material, get it to a certain level, and then you do the testing to see how the product performs.
I was trying to set the stage so they could see how something as simple as increasing the level of humidity reduces static electricity. It puts them in that mindset. Once they open up and accept that, my presentation of best practices helps them to see, "That's pretty simple to do; we do this or we don't do that."
Matties: Where are manufacturers most vulnerable in the manufacturing process?
Holtz: If you're facing an ESD audit, one of the simplest things is to take charge-generating materials out of your manufacturing process. This is where most people fail. They receive product from their suppliers in some sort of packaging in their reception area; then they take that product, move it out into their ESD-sensitive area, and it goes in that same package. That package is not ESD-safe; it can generate a lot of static electricity.
For most companies, there’s a need to identify where ESD is and isn’t required within the manufacturing footprint. Typically, when you go into a manufacturing facility, they tape out an ESD sensitive area and if you step your toe over that line, now we're in the ESD world and you have to behave.
One of the simplest forms of not conforming and getting caught in an ESD audit is by bringing packaging in there that can cause damage. Nobody thinks about that when they’re receiving packaging. Look at your processes. You're in this ESD-safe area and you're not supposed to generate static electricity; however, you're bringing a generator of static electricity into that area. That’s the first thing an auditor will look for.
When we talk about best practices, put your packaging into something that's ESD-safe that can go into that environment. From there, you're covered. If you walk into any manufacturing facility, I don't care who or how good you are, if somebody has brought material into that area, it’s a cardinal sin. It shouldn’t be there.
Matties: Why is it so challenging to convince manufacturers to invest money here?
Holtz: They have to see the return on investment. Every company has a dollar value that they can set as a failure. I always talk about latent damage and catastrophic damage. With ESD, you can damage a product latently—you're damaging it, but the product will still work—or you can have a catastrophic failure. As a manufacturer, I'm looking for catastrophic failure. I can identify bad product before it leaves my factory and I can deal with it. If you're sending latent damage out into the field, and a week later, it breaks, how often will your customer come back to you?
Help them understand the dollar value associated with latent and catastrophic damage. Then you can show them some simple changes in their handling. It’s just tweaking their process with some of our products, and they'll notice their quality increases and reworks are down.
In the seminar, we talk about handling a product in the manufacturing world—we'll call it a widget—and anytime you physically handle a widget you introduce an opportunity for damage. In the ESD world, you introduce an opportunity to damage that widget—electrically zap it with ESD, physically break it, or chemically get something on it that shouldn’t be there.
If you start with the premise that it could be damaged, you can look at your processes for not handling it. If you're manufacturing something and there are 10 touchpoints, meaning someone could physically touch that product 10 times within your manufacturing process, I can show you how to reduce it to two times. You're eliminating eight touchpoints—eight opportunities to damage that widget physically, electrically, or chemically, while streamlining manufacturing at the same time. By doing things right, your manufacturing is faster, you have fewer touchpoints, and less labor is needed to manufacture something.
For example, if your supplier is sending you product and it takes a lot of work to get that product onto the floor, there are more costs and more touchpoints. Then there are touchpoints getting it to shipping and if you send it to your customer improperly, again more touchpoints. We like to see it streamlined from receiving, to the manufacturing floor, back to shipping, and you hardly touch it.
In the ESD world, that's everything. Ship your product, test it, know that it’s good, put it into a package and know that the next time that product comes out is when it's physically put into your customer's product—your problem is solved.
Matties: You mentioned various types of catastrophic failures. When it’s an ESD failure, is it obvious?
Holtz: Hopefully. Yeah, hopefully. Catastrophic means it won’t pass their testing at the end. You could also have catastrophic physical damage. When we look at something, it’s not just ESD; it’s also physical protection, electrical protection, and chemical or FOD (foreign object damage). Ideally, if a part falls off, it won’t work. But there are certain requirements that manufacturers have at the end of their process when they test. I often see this argument between customers and manufacturers: They send the product to the customer and say, "We tested it, the product was great, it worked fine." But the customer then says, "We plugged it in and it doesn't work."
When we get called in, we're not there to mitigate or be an arbiter, but to see what the failure is. Typically, most manufacturers do a really good job in the manufacturing and handling at both ends, but there's a lot of steps to get product to a customer. Maybe it’s somebody in shipping or receiving who is not following best practices. We want to identify where it's happening. Either way, we want to educate the customers, and say, "Here's why it's happening. You have to look at the whole process."
We're working all along the spectrum—OEM, contract, manufacturer, etc. Usually, when we're called into an opportunity, we know there's a supplier on one end and we know there's a customer on the other end. We always ask, “How does your customer want to receive this? While I'm here, can I look at how you are receiving goods?” If everybody does their job well, you have an uninterrupted system.
On my last slide, I always present what we call the “business cycle,” which is the three areas in each manufacturing facility. if you take three companies, then there's nine total. If eight are doing their job and one is not, why bother? Why invest in it? It has to be a perfect business cycle. All nine shipping, handling, manufacturer, storage, and receiving have to be firing on all cylinders. Then the supply chain is absolutely perfect.
Matties: Is there validation for ESD compliance?
Holtz: Yes, the ESD Association is a great association. I'm a member, and I sit on the packaging committee. The governing document for the ESD Association is ANSI/ESD S20.20; the latest version was released in 2021. We review the documentation every five years. A subset of that is S541, which is packaging. The latest revision came out in 2018, so we're reviewing that now. These documents are meant to be a guideline to help manufacturers become compliant with the industry.
It's not an exact document, meaning there are allowances to fit within your manufacturing. In the industry, we allow for tailoring statements, which means it might say within S20.20 that you should do this, but for whatever reason, you can't because of your manufacturing process. Well, you're allowed to tailor out that recommendation or that part of the standards and replace it with your own. There are situations where you can't be 100% compliant with everything. But as you introduce some of the best practices and use these documents, you see they're very simple to follow, and they have a trickle effect. Once you start affecting one area, it becomes a better process all down the line.
So those are the documents that the ESD Association looks at every five years and tweaks; the industry changes so fast that this is required. Companies can use those as a guideline to be in compliance with the industry. If you're bidding, say, government contracts, those contracts must be S20.20-compliant. Some companies, especially smaller ones, might think it will be horrible. It’s really not. We can help with compliance, and if you implement good packaging, handling, shipping, and storage practices, it solves itself.
Matties: It's a sales advantage, as you’re pointing out, when companies can say, " We're committed to quality and here's how we deal with this issue.”
Holtz: Absolutely. We're singly focused on ESD. We work with military, aerospace, and general manufacturing. Technically we’re a packaging company, but we're really an engineering company because we engineer solutions. About 85% of what we do is custom to the application. It’s what the industry demands. When I gave my presentation today, I can guarantee you that none of the companies represented in that audience have the exact same manufacturing system set up.
Matties: Where's your core customer base?
Holtz: On the OEM level, and contract manufacturing. We touch all parts of the industry. Our busiest sector is aerospace and defense, and medical manufacturing. These industries have problems that need to be solved as technology advances so quickly, it creates problems and those problems need to be addressed quickly and with proper solutions. That’s where we get involved. Those are the emerging industries that are seeing that. In optics and aerospace is where we lead the industry. If there's a problem out there, the problem will find us and we find the solution.
Matties: I'm thinking about the EV market space—with all the cars on the road, is there a breakdown risk for the owner driving the car because of this? How do we mitigate that?
Holtz: There have always been ESD issues within cars. If you look at some of the major recalls within the industry, some of them probably went back to some ESD damage along the line. Here’s a consumer example of latent damage: You buy a microwave and you’re so excited because you love microwave popcorn. You make it every night for two weeks. In the third week, you hit the button and it doesn’t work. You call the warranty guy out, he replaces the circuit board, and you’re back in popcorn again. Two weeks later, it’s not working again. The warranty guy comes back out and replaces the board again. Those are latent damages.
The consumer says, "I will never buy that type of appliance again because it had to be fixed five times." When I look at how things are being repaired, I look at how it's packaged and how it’s being handled; that is latent damage. It's the reputation of the company and people can relate. How do we sell a company on what they need to do? You explain latent damage in the way I just explained it with the microwave and popcorn, and people understand, because everyone has gone through it. They bought something brand new and it broke. Nine times out of 10, it's latent ESD damage in the electronics. No matter what it is—automotive, microwaves, refrigerators, washers, dryers, garage door openers, cell phones—it so often goes back to latent ESD damage.
Matties: Doug, I really appreciate this. You're obviously very knowledgeable on this topic.
Holtz: Thank you.
Suggested Items
Kitron Receives EUR 4 Million Contract for Defense Airborne Radar Application
07/02/2025 | KitronKitron has received an order valued at EUR 4 million to produce electronics modules for airborne radar application, destined for the US market.
Zollner Completes Full Acquisition of Bluechips Microhouse
07/01/2025 | Zollner Elektronik AGZollner Elektronik AG has successfully finalized its complete takeover of Bluechips Microhouse Co., Ltd., in Thailand. In the future the company will operate as part of the Zollner Group of companies under the leadership of Thomas Kiefl—strategically networked, technologically focused and internationally oriented.
Inission Acquires the Lithuanian Company Selteka
07/01/2025 | InissionInission AB has signed an agreement to acquire 100% of UAB Selteka. Selteka is a well-respected EMS (electronics manufacturing services) company with operations located in Kaunas, Lithuania.
Kitron Strengthens Order Backlog with EUR 11 Million Contract for Defense Communication
07/01/2025 | KitronKitron has received an order valued at EUR 11 million to produce advanced military communication products destined for the European market.
IMI Wins Gold Award for Best Managed Technology Company at FinanceAsia’s 29th Asia’s Best Companies Awards
07/01/2025 | IMIIntegrated Micro-Electronics Inc. (IMI) has been awarded the prestigious Gold Award for Best Managed Technology Company at the 29th edition of the Asia’s Best Companies Awards, hosted by FinanceAsia.