An Overview of Rigid-flex Design
September 13, 2023 | I-Connect007 Editorial TeamEstimated reading time: 1 minute
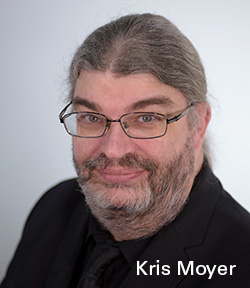
For this month’s issue on rigid-flex design, we spoke with instructor Kris Moyer, who teaches the IPC class “PCB Design for Flex and Rigid-Flex Boards.” In this wide-ranging interview, Kris breaks down the hurdles facing rigid-flex designers and offers a variety of solutions for rigid board designers taking on their first rigid-flex circuits. He also provides a few horror stories to illustrate what happens if you don’t follow sound design practices, rules, and standards. And, as Kris points out, “Your fabricator is your friend.”
Andy Shaughnessy: What are you trying to get across to the students when you’re teaching rigid-flex design? What are the biggest challenges?
Kris Moyer: One of the biggest concepts I want to get across to students is that there are a lot of untapped, unforeseen, intangible benefits to rigid-flex, both from a design point of view and a total cost of ownership point of view. Rigid boards are usually connected with wire harnesses or cables, and we know that wire harnesses and cables are the largest point of failure in the system. Wires and cables tend to break, especially at the solder joints or pins. If we can remove all those harnesses and integrate all of that into the structure of the board, we can vastly reduce the failure rate of our designs.
If you choose to go rigid-flex, there is an initial cost expenditure: added processes, time, complexity, and all of that. But let's say I have a design with three circuit boards that would need two cable harnesses, one from board one to board two, and one from board two to board three. That's a grand total of five different item numbers I would need for each board. I would have three drawing numbers: a number for the schematic, a number for the board, and a number for the assembly. For three boards, that's nine drawings I must maintain, and then another two drawings per cable, and let's assume two cables. That's a total of 13 separate drawings and part numbers I have to maintain in my system.
To read this entire conversation, which appeared in the September 2023 issue of Design007 Magazine, click here.
Suggested Items
SolderKing’s Successful Approach to Modern Soldering Needs
06/18/2025 | Nolan Johnson, I-Connect007Chris Ward, co-founder of the family-owned SolderKing, discusses his company's rapid growth and recent recognition with the King’s Award for Enterprise. Chris shares how SolderKing has achieved these award-winning levels of service in such a short timeframe. Their secret? Being flexible in a changing market, technical prowess, and strong customer support.
Preventing Surface Prep Defects and Ensuring Reliability
06/10/2025 | Marcy LaRont, PCB007 MagazineIn printed circuit board (PCB) fabrication, surface preparation is a critical process that ensures strong adhesion, reliable plating, and long-term product performance. Without proper surface treatment, manufacturers may encounter defects such as delamination, poor solder mask adhesion, and plating failures. This article examines key surface preparation techniques, common defects resulting from improper processes, and real-world case studies that illustrate best practices.
Breaking Silos with Intelligence: Connectivity of Component-level Data Across the SMT Line
06/09/2025 | Dr. Eyal Weiss, CybordAs the complexity and demands of electronics manufacturing continue to rise, the smart factory is no longer a distant vision; it has become a necessity. While machine connectivity and line-level data integration have gained traction in recent years, one of the most overlooked opportunities lies in the component itself. Specifically, in the data captured just milliseconds before a component is placed onto the PCB, which often goes unexamined and is permanently lost once reflow begins.
BEST Inc. Introduces StikNPeel Rework Stencil for Fast, Simple and Reliable Solder Paste Printing
06/02/2025 | BEST Inc.BEST Inc., a leader in electronic component rework services, training, and products is pleased to introduce StikNPeel™ rework stencils. This innovative product is designed for printing solder paste for placement of gull wing devices such as quad flat packs (QFPs) or bottom terminated components.
See TopLine’s Next Gen Braided Solder Column Technology at SPACE TECH EXPO 2025
05/28/2025 | TopLineAerospace and Defense applications in demanding environments have a solution now in TopLine’s Braided Solder Columns, which can withstand the rigors of deep space cold and cryogenic environments.