-
-
News
News Highlights
- Books
Featured Books
- pcb007 Magazine
Latest Issues
Current IssueThe Hole Truth: Via Integrity in an HDI World
From the drilled hole to registration across multiple sequential lamination cycles, to the quality of your copper plating, via reliability in an HDI world is becoming an ever-greater challenge. This month we look at “The Hole Truth,” from creating the “perfect” via to how you can assure via quality and reliability, the first time, every time.
In Pursuit of Perfection: Defect Reduction
For bare PCB board fabrication, defect reduction is a critical aspect of a company's bottom line profitability. In this issue, we examine how imaging, etching, and plating processes can provide information and insight into reducing defects and increasing yields.
Voices of the Industry
We take the pulse of the PCB industry by sharing insights from leading fabricators and suppliers in this month's issue. We've gathered their thoughts on the new U.S. administration, spending, the war in Ukraine, and their most pressing needs. It’s an eye-opening and enlightening look behind the curtain.
- Articles
- Columns
- Links
- Media kit
||| MENU - pcb007 Magazine
Ventec: The Flexibility We Need in Standards-driven Manufacturing
February 13, 2024 | Barry Matties, I-Connect007Estimated reading time: 2 minutes
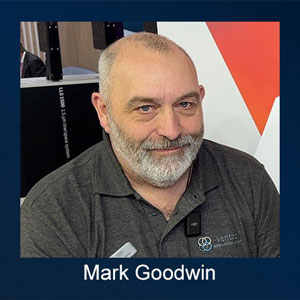
Ventec International COO Mark Goodwin and technology ambassador Alun Morgan had quite a bit to say at productronica 2023 about slash sheets, IPC standards, and how to bring the PCB designer closer to the supplier. As Mark says, what matters to designers, manufacturers, and even consumers, is that the products meet compliance standards, such as REACH. They don’t need to know how something is built. They just want performance and availability.
Barry Matties: Since our last conversation regarding your recommendations with slash sheets, where are you now?
Mark Goodwin: At IPC APEX EXPO 2023, we learned that the whole industry has been misunderstanding the descriptive information at the top of the IPC slash sheet; it actually has no relevance. It is not part of the material specification.
Alun Morgan: The slash sheet structure was good 30 years ago when you could define properties by family groups, with only three or four resin types available. Today, we no longer have resin systems that are only one resin type; we have fillers and mixtures and all kinds of performance enhancements. The future moved on from that framework; it doesn't fit anymore.
That was why we joined in and worked with UL to create a comprehensive list of resin chemistry definitions for designers. If you're a PCB designer, you ask, “What do I need to know to make my decision?” Now, they can look it up and know exactly what it means when you say “primary resin,” “flame retardant,” or “filler.” We have a basis of understanding and some common language.
Goodwin: We worked on those definitions and proposed that they be included in the preamble of the IPC-4101 specs.
Morgan: I'm proud of our work with UL in adding definitions for resin chemistry terms in UL 746E. We all worked hard to ensure we had a base level (of terms and definitions) in place. It's the first step. The next work to be done—which is a lot—is to move into the performance area, which hasn’t been mapped out yet.
Goodwin: Those performance criteria should include physical, mechanical, and electrical properties.
Morgan: We've often argued that we should try and curate these within our industry sectors. That makes sense. If we've learned anything, it’s that the design process is far from materials. Designers don't understand detail about the material side. Why would they? Even for PCB manufacturing, the designers don't have a comprehensive understanding. Now, the designer can say to the engineer, “I'm a designer for automotive cabins,” and the engineer says, “Here’s a set of standards that will be appropriate for your kind of designs,” or “I design ECUs for under the hood.” Now, here are the products that would fit there. It's not the end of the story, but a starting place for these guys. If you can give them a starting place, how much easier the job is.
Goodwin: This happened naturally with thermal management. It was a new thing that came along with thermal modeling so the designers have a much deeper connection to the materials in that sector than they do in any other.
To read this entire conversation, which appeared in the January 2024 issue of PCB007 Magazine, click here.
Suggested Items
Trouble in Your Tank: Causes of Plating Voids, Pre-electroless Copper
05/09/2025 | Michael Carano -- Column: Trouble in Your TankIn the business of printed circuit fabrication, yield-reducing and costly defects can easily catch even the most seasoned engineers and production personnel off guard. In this month’s column, I’ll investigate copper plating voids with their genesis in the pre-plating process steps.
Happy’s Tech Talk #37: New Ultra HDI Materials
02/03/2025 | Happy Holden -- Column: Happy’s Tech TalkSome new materials have been introduced in the past year for ultra high density interconnect (UHDI), a convenient title for developing high density technologies. They have received labels like semiconductor-like PCBs (SLPs), redistribution layers (RDL), flip-chip ball grid array (FCBGA), and interposers. The early 2000s saw the creation of these organic substrates for flip-chip IC packaging. The initial construction was composed of a BT core with build-up layers of the Ajinomoto Build-up Film (ABF)
BOOK EXCERPT: The Printed Circuit Assembler's Guide to... Encapsulating Sustainability for Electronics, Chapter 4
12/31/2024 | I-Connect007Bio-based encapsulation resins have the potential to contribute to sustainability targets by extending product lifetime and improving performance. The author explores the use of recycled materials such as biogenic waste and lightweight expandable polymers to create more efficient and environmentally friendly encapsulation resins.
Book Excerpt: The Printed Circuit Designer’s Guide to... DFM Essentials, Ch. 1
10/25/2024 | I-Connect007The guidelines offered in this book are based on both ASC recommendations and IPC standards with the understanding that some may require adjustment based on the material set, fabricator processes, and other design constraints. This chapter details high-frequency materials, copper foil types, metal core PCBs, and the benefits of embedded capacitance and resistor materials in multilayer PCBs.
Trouble in Your Tank: Materials for PWB Fabrication—Drillability and Metallization
07/16/2024 | Michael Carano -- Column: Trouble in Your TankLaminate materials are the building blocks on which printed circuit boards are manufactured. Circuit board designers rely on the critical electrical properties of the materials to design the interconnects, and with the drive toward IoT (internet of things), autonomous driving, and virtual and augmented reality, material properties take on a very high level of importance.