-
- News
- Books
Featured Books
- pcb007 Magazine
Latest Issues
Current IssueInventing the Future with SEL
Two years after launching its state-of-the-art PCB facility, SEL shares lessons in vision, execution, and innovation, plus insights from industry icons and technology leaders shaping the future of PCB fabrication.
Sales: From Pitch to PO
From the first cold call to finally receiving that first purchase order, the July PCB007 Magazine breaks down some critical parts of the sales stack. To up your sales game, read on!
The Hole Truth: Via Integrity in an HDI World
From the drilled hole to registration across multiple sequential lamination cycles, to the quality of your copper plating, via reliability in an HDI world is becoming an ever-greater challenge. This month we look at “The Hole Truth,” from creating the “perfect” via to how you can assure via quality and reliability, the first time, every time.
- Articles
- Columns
- Links
- Media kit
||| MENU - pcb007 Magazine
Book Excerpt: The Printed Circuit Designer’s Guide to... DFM Essentials, Ch. 1
October 25, 2024 | I-Connect007Estimated reading time: 1 minute
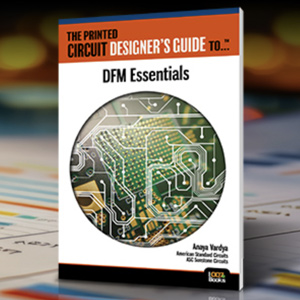
Excerpt from: The Printed Circuit Designer’s Guide to... DFM Essentials
By Anaya Vardya, American Standard Circuits / ASC Sunstone Circuits
Chapter 1: Materials
Standard Multilayer Materials
Most PCBs are manufactured using three basic materials: glass-reinforced epoxy laminate, prepreg, and copper foil. PCBs are constructed from three basic material types: copper foil, prepreg, and cores.
Copper foil: Sheets of copper foil are incorporated into the outer layer of the PCB, laminating it onto the prepreg to create the outer layers. Outer layers are generally constructed using ½-ounce copper or thicker depending on the design requirements. Internal layers are constructed with copper that is specified on the fabrication print. Half-ounce copper foil is commonly used for signal layers; 1 ounce for plane layers, and 2 ounce or greater for power planes where there is a high DC current. Other thicknesses may be used based on the design requirements.
Prepreg: This is a semi-cured glass resin material. The resin used for the FR-4 type materials is epoxy-based. There is no copper attached to this material.
Core: This is fully cured glass-resin material with copper laminated to both sides. This is typically used for internal layers. It is occasionally used for outer layers, but that is not a preferred construction method. A core is constructed from either one sheet of prepreg (single ply) or two or more sheets of prepreg, and two layers of copper foil. Single ply is considered the preferred core construction and has better dimensional stability.
High-frequency (RF/Microwave) Materials
High-frequency designs (1 GHz and up) require materials with closely controlled dielectric constants and dissipation factors. The FR-4 materials normally used for PCBs don’t have the desired controlled characteristics. The substrate materials used for high-frequency applications were originally based upon PTFE resin formulations that have the desired properties, i.e. dielectric constant (Dk) controlled to +/- 0.04 and dissipation factor (Df) to 0.0004. These values may vary somewhat depending on the material type and supplier. Today, there are a number of materials on the market that do not contain PTFE resin but still have controlled values that can be used for high-frequency applications.
Visit the I-Connect007 library to continue reading The Printed Circuit Designer’s Guide to... DFM Essentials.
Testimonial
"Our marketing partnership with I-Connect007 is already delivering. Just a day after our press release went live, we received a direct inquiry about our updated products!"
Rachael Temple - AlltematedSuggested Items
50% Copper Tariffs, 100% Chip Uncertainty, and a Truce
08/19/2025 | Andy Shaughnessy, I-Connect007If you’re like me, tariffs were not on your radar screen until a few months ago, but now political rhetoric has turned to presidential action. Tariffs are front-page news with major developments coming directly from the Oval Office. These are not typical times. President Donald Trump campaigned on tariff reform, and he’s now busy revamping America’s tariff policy.
Global PCB Connections: Understanding the General Fabrication Process—A Designer’s Hidden Advantage
08/14/2025 | Markus Voeltz -- Column: Global PCB ConnectionsDesigners don’t need to become fabricators, but understanding the basics of PCB fabrication can save you time, money, and frustration. The more you understand what’s happening on the shop floor, the better you’ll be able to prevent downstream issues. As you move into more advanced designs like HDI, flex circuits, stacked vias, and embedded components, this foundational knowledge becomes even more critical. Remember: the fabricator is your partner.
MKS’ Atotech to Participate in IPCA Electronics Expo 2025
08/11/2025 | AtotechMKS Inc., a global provider of enabling technologies that transform our world, announced that its strategic brands ESI® (laser systems) and Atotech® (process chemicals, equipment, software, and services) will showcase their latest range of leading manufacturing solutions for printed circuit board (PCB) and package substrate manufacturing at the upcoming 17th IPCA Show to be held at Pragati Maidan, New Delhi from August 21-23, 2025.
MKS Showcases Next-generation PCB Manufacturing Solutions at the Thailand Electronics Circuit Asia 2025
08/06/2025 | MKS Instruments, Inc.MKS Inc, a global provider of enabling technologies that transform our world, today announced its participation in Thailand Electronics Circuit Asia 2025 (THECA 2025), taking place August 20–22 at BITEC in Bangkok.
Point2 Technology, Foxconn Interconnect Technology Partner to Revolutionize AI Cluster Scalability with Terabit-Speed Interconnect
08/06/2025 | BUSINESS WIREPoint2 Technology, a leading provider of ultra-low-power, low-latency mixed-signal SoC solutions for multi-terabit interconnect, and Foxconn Interconnect Technology (FIT), a global leader in precision interconnect solutions, have signed a Memorandum of Understanding (MOU) to accelerate the commercialization of next-generation Active RF Cable (ARC) and Near Pluggable e-Tube (NPE) solutions.