Estimated reading time: 4 minutes
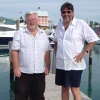
A New Third Dimension Now Possible for PCBs with 3-D Copper Structures
New Ideas need some reason to be created. In printed circuits, as in most businesses, it's usually the customer who wants a particularly strange product done in a different way.
Many times your best source of new requirements is the one customer who gives you the most grief. We all know the type: head in the clouds, a dreamer engineer who frequents your shop with drawings on a napkin or with a small handmade prototype, asking, "Can you do this?" You look at his idea wishing you were somewhere else, far, far away. But as he describes his requirement with enthusiasm slowly your mind starts percolating, "Maybe if we did it this way or if we plated it that way?"
That same scenario happened to us a while back. One manager passing by even sneered when he saw the guy, as he had bugged him many times before with his harebrained ideas. I have been and, continue to be, one of those harebrained engineers, so I tend to spend time with the very customers many shops dismiss as being not worthy of their time. This particular episode would prove very profitable, as out of this single meeting the idea for 3-D copper structures on PCBs was invented.
Most PCBs are very two-dimensional with flat laminate copper plated traces and drilled and plated through-holes plated for conductivity. The circuit's two jobs are: support for the components and electrical connections. A new third dimension is now possible for PCBs with 3-D copper structures on the PCB surface.
Three dimensional copper structures can be made to contact or align optics, position chip dies for testing, create locating pins for sockets or align bumps for components. Our first application for 3-D circuits was to plate four different heights of pins for contact to a die as well as create corner locators for the die. The 3-D structures are placed and plated at the same time with the same method so the 3-D structures and the circuitry are exactly aligned in relationship to each other--which is difficult to do using other methods such as aluminum/plastic locators that are bolted in place.
The first 3-D circuit we made had four different levels of copper, nickel and gold in steps to make a chip die alignment post and contact system.The 3-D alignment post has a slightly elevated flat base to properly support the die at the correct height and two higher corner sections to provide alignment between the die to be tested and the gold bump pads. To improve the contact between the die and the test point, we serrated the top of the gold contact bumps with a laser to create a diamond point pattern.
Our next project was making a multi-dimensional pin projecting from the sides of a flex circuit. The pin will have a lower section to fit into a test jig; the top of the pin will feature small points to touch the ball on the BGA. This design required six different plating setups with multi-resist layers to produce the 3-D effect. The maximum height of a feature at this stage is about 15 mils; the resolution is 3-mil features. The top features must be smaller then the bottom stage, which are built up like a pyramid. The stages can be interconnected electrically as well.
With the new technology we can manufacture and create almost any shape in three dimensions on the top or on the bottom of a circuit board. It is possible to build raised contacts, small alignment points for LEDs, dies or sockets. The top surface can be gold over nickel as well as nickel that can be shaped with a laser and then gold plated to provide gas-tight interconnect puncture-type contacts.
An additional use for the 3D-shaped circuits is to add direct contact heat sinking to an LED or chip. At present we use aluminum or copper base with FR-4 laminated onto it; the LED or chip is mounted to the FR-4. However, the FR-4 is still a heat insulator between the heat sink and the LED or chip, which greatly limits the amount of heat transferred. To increase the heat transferred we make a puck, or raised copper pad, protruding directly from the copper heat sink to the base of the LED or chip. The direct thermal contact improves the heat transfer from the LED or chip to the base heat sink by a significant factor (up to100 times more). The thermal puck can also be produced in aluminum. Of course new technology always carries a price, but if it overcomes a significant problem the cost increase can be worth its weight in gold. About the Authors
Ken Bahl, President of Sierra Proto Express (San Jose, CA) started in the PCB business in 1965 as a process engineer with Honeywell in New Hampshire. In 1986 Ken founded Sierra Proto Express, the PCB industry's leader in innovative bleeding edge technologies -- dedicated to producing Tomorrow's Technology Today.
Bob Tarzwell is presently working with Ken to introduce new bleeding edge, advanced circuit technology like lead-free, high reliable electronics, heat sinking technology and ultra fine lines to the world. Since selling his company in 2000, Bob has disseminated PCB high-tech to many companies as a consultant, and has written ten books on PCBs and car racing. He has three patent pending applications in fine lines, high reliability and outer space PCBs. He is currently semi-retired in the Bahamas, spending his free time writing books, working on antique cars and deep sea fishing.
More Columns from Bob and Me
Controlled Impedance: A Real-World Look at the PCB SideBob and Me: The Key to Increasing Quality - Bribe Your Employees
Bob and Me: Tarzwell's First--and Last--Lean Meeting
Bob and Me: A PCB Potpourri
Bob and Me: Spacing is Irrelevant Below 270 Volts
PCB 101: Coefficient of Thermal Expansion
The Bleeding Edge: Serious as a Heart Attack
PCB101: Fabricating High-Voltage Boards