Estimated reading time: 4 minutes
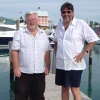
The Bleeding Edge: High Resistance Circuits
By Robert Tarzwell with Ken Bahl - Sierra Proto Express
It seems that we always have at least one super-bright, doctor-type engineer hidden away in some remote laboratory who needs to record one tiny little electron emitted from some futuristic plasma cyclotron. Worst of all, they know what they want to do, but have zero knowledge of a printed circuit board. The call usually goes something like this:
Mad Scientist: I understand you are familiar with both electronics and printed circuits.
Doc PCB: To a point, yes.
Mad Scientist: I need to measure a Pico volt signal of a few electrons and need a very high impedance of greater than 100 gig ohm.
Doc PCB: Okay, no problem. We have many different solutions--depending on your application.
Mad Scientist: Great! I called three different board shops and no one knew what I was talking about. Tell me what you have.
Doc PCB: We have five different laminate choices that feature the most important factor for your circuit--high surface resistance. Many are at least ten times greater than your circuit input requirements. Does your input resistor connect to an op amp?
Mad Scientist: Yes, we have a 100 gig ohm resistor.
Doc PCB: Okay. Sierra's VTF (very thin film) has the highest surface restively of 4 x 1016 with low moisture absorption. Typically, we start with a double sided or multilayer of FR4 and lay a dielectric layer of the high resistance film on top.
Mad Scientist: How do we limit electrical noise in the signal layer?
Doc PCB: Most designs have an analog ground as the top layer on the four-layer FR4 PCB. Then, the VTF layer and either metal can be soldered on; or, an additional layer of VTF with a ground plane and micro vias can be added around the edge to create a faraday shield.
Mad Scientist: Good, that means we can put the digital amplifier on the back side of the multilayer and leave only the Pico signal parts in the top layer. This is good--I will have the designer get in touch with you.
Doc PCB: Glad we could help.
This is exactly how the phone call would go, well, except for the "mad scientist" part. Selecting the correct laminate is not really that difficult, but one must remember to account for all requirements and then try and balance cost and electrical and mechanical properties--all must agree with each other. The reason high input resistance circuits are needed is to measure very diminutive signals, sometimes signals of only a few electrons. The surface resistance (ohms /sq) of the laminate has a direct effect on the signal; effectively adding parallel resistors to the signal input lowers its signal strength. The other problem is one of electrical noise. All resistors have some electrical noise generated by the junctions of the resistor molecules touching each other. When the molecules rub together, they release electrons as electrical noise. To build a very high resistance circuit board, resistance and electrical noise must be limited.
In the "mad scientist" design, we chose a polyimide dielectric film--the polyimide film version has a slightly higher surface resistance than the epoxy version. The surface resistance difference between FR4 and a polyimide film is typically 100,000 times larger--a significant difference. Typically FR4 has a surface resistivity of 3 x 1010 ohms; where as a dielectric film has surface resistivity of 4 x 1015 ohms.
One must also be concerned with the absorbance of moisture. Many glass type FR4 laminates absorb moisture because of gaps around the glass fibers. If glass fibers are eliminated, the source of the moisture problem is greatly reduced. The dielectric films feature very high voltage dielectrics--well over 4,000 volts per mil compared to 650 volts per mil for FR4. Typical FR4 moisture absorbance is 0.05 to 0.07, while dielectric films are in the 0.02 to 0.03 range.
In high-frequency, small-signal boards, the Dielectric Constant, or Dk, must also be considered and the lower the number, the better. Teflon is a laminate of choice when higher frequencies are required. This laminate offers high surface resistance and a low dielectric constant, as well as a low loss factor. Teflon's big drawback is its high cost, which often limits use.
Solder mask typically has 1 x 1013 resistivity, which often presents problems with very high resistance circuits. To eliminate the solder mask, a laser cut dielectric film layer is used as a replacement high resistance solder mask.
The basic equations are:FR4: 3 x 1010 = 30,000 meg ohms. Dielectric films: 4 x 1015 = 4,000,000,000 meg ohms.
Bleeding edge circuits need to use, and take advantage of, the little known physical and electrical properties of laminates--look outside the normal FR4 world.
Bob Tarzwell, Director of Technology at Sierra Proto Express, is working with Ken Bahl to introduce new bleeding edge, advanced circuit technology like lead-free, high reliable electronics, heat sinking technology and ultra fine lines to the world. Since selling his company in 2000, Bob has disseminated PCB high-tech to many companies as a consultant, and has written ten books on PCBs and car racing. He has three patent-pending applications in fine lines, high reliability and outer space PCBs. He is currently semi-retired in the Bahamas, spending his free time writing books, working on antique cars and deep sea fishing.
Ken Bahl, President of Sierra Proto Express (San Jose, CA), started in the PCB business in 1965 as a process engineer with Honeywell in New Hampshire. In 1986, Ken founded Sierra Proto Express, the PCB industry's leader in innovative bleeding edge technologies--dedicated to producing Tomorrow's Technology Today.
For more information, visit www.protoexpress.com.
More Columns from Bob and Me
Controlled Impedance: A Real-World Look at the PCB SideBob and Me: The Key to Increasing Quality - Bribe Your Employees
Bob and Me: Tarzwell's First--and Last--Lean Meeting
Bob and Me: A PCB Potpourri
Bob and Me: Spacing is Irrelevant Below 270 Volts
PCB 101: Coefficient of Thermal Expansion
The Bleeding Edge: Serious as a Heart Attack
PCB101: Fabricating High-Voltage Boards