Estimated reading time: 5 minutes
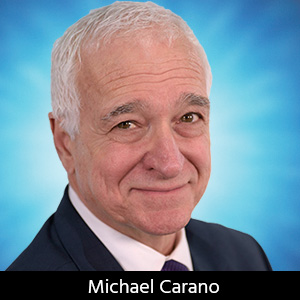
Contact Columnist Form
Trouble in Your Tank: Pesky Peeling & Lifting Soldermask Issues
Editor's Note: This article originally appeared in the November 2012 issue of The PCB Magazine.
Introduction
The liquid photoimageable soldermask is an important permanent part of the finished circuit board. Due to the many chemical and thermal excursions that the circuit board sees over its lifetime, the quality of the soldermask is critical to preventing defects. First and foremost, one has to achieve excellent mask adhesion to the copper traces and laminate material. Often, the issue of peeling and lifting of the mask may be due to mechanical as well as chemical process parameters. Obviously, this is frustrating.
It is essential that the troubleshooter understands the possible origins of the defect. And as is painfully obvious to the reader, there are multiple causes for PCB fabrication defects. Here is something to consider: Is peeling soldermask due to poor surface preparation, or an overcured mask? What role does the thickness of the soldermask play in its ability to resist peeling and lifting from the copper and laminate surfaces? Certainly, one must consider the final finishing and assembly processes that the circuit board is subject to. In future TIYT columns, the effects of surface finishes will be discussed. Trust me, there are more.
As my favorite philosopher, Yogi Berra, once said, “You got to be careful if you don't know where you're going, because you might not get there.” This definitely applies to troubleshooting.
Importance of Metal Etch Resist Stripping
As a reminder, one of the most important steps to ensuring soldermask adhesion is to start with a clean, virgin copper surface. Preferably, the surface must be devoid of any remaining etch resist residues. Here, one must be sure that the tin stripper is doing its job of providing a thoroughly clean copper surface. Closely monitor the etch resist stripping operation. As the etch-resist process chemistry begins to lose its useful working life, the ability to completely remove the tin or other metal etch resists from the surface become more difficult. These remaining residues often are not readily visible to the naked eye. If not removed completely, the residues will interfere with soldermask adhesion. Ensuring that one has a copper surface devoid of metal etch residues allows one to focus on the pre-soldermask surface preparation.
However, before surface prep is discussed, it is critical to at least review in general terms some of the other potential causes of mask peeling and lifting.
Figure 1 depicts a good example of soldermask peeling from the copper surface. Significant blistering and peeling of the mask either from traces or ground plane areas are quite evident. Possible causes are:
- Insufficient mask thickness;
- Insufficient cure temperature or time;
- Poor surface preparation;
- Insufficient tack dry; and
- Mask overcuring.
With respect to cure temperature, follow the mask supplier’s recommendations. As an example, if cure cycle is called out to be 150°C for 60 minutes, this means 60 minutes, at that temperature, give or take five minutes. It is always ideal to observe the operators and their procedures when troubleshooting this type of a technical issue. Problems with insufficient cure are often due to operators opening and closing the oven doors, allowing heat to escape. Tunnel ovens must be profiled on a regular basis to ensure the proper temperature is met and for the optimum time. (Other causes will be reviewed in a future column of Trouble in Your Tank.)
A Word about Mask Hardness
Despite the potential causes cited above, overcuring of the mask should not be ignored as a possible cause. Overcuring embrittles the mask and makes the mask less flexible. When polymeric materials are overcured, it is quite easy to make these materials less flexible. It is the curing step that completes the cross-linking of the epoxy groups with the amine groups, further enhancing the physical, electrical and chemical resistance properties of the mask. However, if one measures the pencil hardness of the mask using the Wolff-Wilborn method, the indication of a pencil hardness of 8H or greater is an indication that the mask lacks the flexibility to stand up to subsequent aggressive final finishes such as electroless nickel-immersion gold (ENIG).
Figure 1: Soldermask peeling from surface.
Thus, for better chemical resistance , choose a mask with more flexibility and less hardness. It is simply a trade-off. It is difficult to achieve very high pencil hardness and retain excellent chemical resistance of the soldermask. The question then becomes, what is that hardness and how is it measured? More on this in a future column.
Surface Preparation
Poor surface preparation (prior to coating the circuit boards with the ink) or a contaminated surface leads to mask lifting.
I am indifferent to the choice of using chemical clean only prior to soldermask application or utilizing a high-quality pumice technique.
The chemical clean process should consist of a mild acidic cleaner followed by a micro-etch capable of removing 25-40 µ. Imparting surface roughness to the copper is also helpful to ensure good soldermask adhesion. Keep in mind that the copper surface one is cleaning is electroplated copper from the pattern plating process in PCB fabrication. So the copper grain structure is fine-grained compared to the columnar grain seen with copper foil. Thus, the grain topography and roughening of a fine-grained structure is more of a challenge. A surface representing persulfate micro-etch is shown in Figure 2.
Figure 2: Sodium persulfate micro-etched surface prior to mask application.
Another tried-and-true method is pumice surface preparation. There are two general pumice application methods: Spray and brush.
Figure 3: Pumice brush surface preparation.
There are pros and cons to both of these techniques. With spray pumice, the surface topography is somewhat non-uniform and one risks embedding pumice particles within the copper. The surface thus becomes hammered by the “shot-peening” effect of the pumice hitting the surface. Brush pumice on the other hand has the advantage of providing a tangential effect on the surface due to the action of the brushes and pumice. The surface is truly sandblasted, creating a rough, but homogeneous surface. One disadvantage of brush pumice is that it may be too aggressive on thin materials, leading to stretching. However, for a standard rigid circuit board, this is not an issue.
Again, weigh the options for surface preparation carefully. Under proper operating conditions, chemical cleaning or pumice will work. It is a matter of ensuring that the proper controls are in place to enhance a quality, pre-clean surface preparation operation.
Michael Carano is with OMG Electronic Chemicals (formerly Electrochemicals), a developer and provider of processes and materials for the electronics industry supply chain. He has been involved in the PWB, general metal finishing photovoltaic industries for nearly 30 years. Carano holds nine U.S. patents in topics including plating, metallization processes and PWB fabrication techniques.
More Columns from Trouble in Your Tank
Trouble in Your Tank: Metallizing Flexible Circuit Materials—Mitigating Deposit StressTrouble in Your Tank: Can You Drill the Perfect Hole?
Trouble in Your Tank: Yield Improvement and Reliability
Trouble in Your Tank: Causes of Plating Voids, Pre-electroless Copper
Trouble in Your Tank: Organic Addition Agents in Electrolytic Copper Plating
Trouble in Your Tank: Interconnect Defect—The Three Degrees of Separation
Trouble in Your Tank: Things You Can Do for Better Wet Process Control
Trouble in Your Tank: Processes to Support IC Substrates and Advanced Packaging, Part 5