-
- News
- Books
Featured Books
- pcb007 Magazine
Latest Issues
Current IssueSales: From Pitch to PO
From the first cold call to finally receiving that first purchase order, the July PCB007 Magazine breaks down some critical parts of the sales stack. To up your sales game, read on!
The Hole Truth: Via Integrity in an HDI World
From the drilled hole to registration across multiple sequential lamination cycles, to the quality of your copper plating, via reliability in an HDI world is becoming an ever-greater challenge. This month we look at “The Hole Truth,” from creating the “perfect” via to how you can assure via quality and reliability, the first time, every time.
In Pursuit of Perfection: Defect Reduction
For bare PCB board fabrication, defect reduction is a critical aspect of a company's bottom line profitability. In this issue, we examine how imaging, etching, and plating processes can provide information and insight into reducing defects and increasing yields.
- Articles
- Columns
- Links
- Media kit
||| MENU - pcb007 Magazine
Estimated reading time: 1 minute
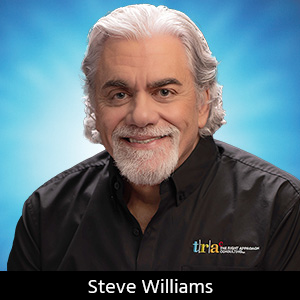
Best Practices 101, Part 4
Looking back through the annals of the U.S. PCB industry, when it comes to quality, we have evolved from a reactive, to a proactive mindset. This evolution has led to what is loosely called the zero-defects methodology (ZDM). The old gold standard of three sigma is no longer acceptable and has gone the way of the dinosaur.
Pipe Dream?
Are zero defects an achievable, sustainable goal 100% of the time? Of course not, but with six sigma levels we can come pretty close. Recognizing that we will occasionally fall short of any goal mandates that the goal be set at zero defects. The reasons why a zero defect mentality is required can be condensed down to the singular, bottom line principle of reducing costs, and as we all know, it’s always about the dollars. Costs are always attached to defective product in the form of inspection/test, rework/repair, scrap, and warranty (customer returns). Reducing these costs results in increased customer satisfaction, and quite simply, happy customers mean higher revenue.
It is always an interesting study to compare the advertised capability of a company to its actual capability. The sales force touts world-class quality, which implies that they are operating at a six sigma level. However, an objective on-site assessment of their processes quickly separates the bluster from the facts, typically revealing that most organizations are operating at a true yield somewhere between 93 and 99%--the old three sigma complacency. Statistics are a wonderful tool, but like most things in life, you will only get out of them what you put in. It all boils down to what the organizational objective is; superficial window dressing or honest-to-goodness improvement. Inflating process yields by excluding things like rework, customer waivers, or returns does nothing but mask problems and will not result in true improvement. If window dressing is indeed your goal, then I would suggest tossing this article and immediately picking up a copy of Extinction for Dummies, by Peter T. Platypus.Read the full column here.Editor's Note: This column originally appeared in the November 2014 issue of The PCB Magazine.
More Columns from The Right Approach
The Right Approach: ‘Twas the Night Before Christmas (Harley-style)The Right Approach: I Hear the Train A Comin'
The Right Approach: Culture Change is Key to a QMS
The Right Approach: Leadership 101—Be a Heretic, Not a Sheep
The Right Approach: Leadership 101—The Law of Legacy
The Right Approach: Leadership 101: The Law of Explosive Growth
The Right Approach: Leadership 101—The Law of Timing
The Right Approach: The Law of Sacrifice