Mini Laser for Real-time Quality Control
June 2, 2015 | Fraunhofer IBMTEstimated reading time: 3 minutes
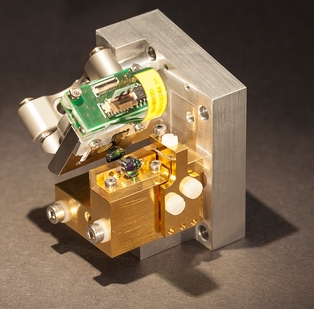
Good quality and precision are essential – a dictum that also applies to products from the pharmaceutical and chemical industry. While the quality of chemical products is often still being monitored manually during the production process, a laser-based system could take over this task in future, allowing for a continuous monitoring in real time.
Pharmaceutical industry, food production or industrial manufacturing: new products are constantly being brought to market, with improved active ingredients or less negative side-effects. One important point in the development of material compositions, such as pills or capsules: their quality has to be impeccable. To verify if the chemical reaction proceeded as desired, samples are taken from the reaction vessels and examined in the laboratory, applying chromatography or spectroscopy. A costly and tedious endeavor that however only allows an investigation based on random samples.
Continuous analysis in real time
This process might soon be simplified with the help of a novel infrared laser developed by researchers at the Fraunhofer Institutes for Applied Solid State Physics IAF in Freiburg and for Photonic Microsystems IPMS in Dresden. “Our quantum cascade lasers facilitate a new kind of spectroscopy,” explains Dr. Ralf Ostendorf, project manager at Fraunhofer IAF. “The process of chemical reactions – as, for example, in the development of new pharmaceuticals – could soon be continuously monitored in real time, rather than analyzing random samples, as done in current monitoring processes.” The key principle is as follows: The laser sends infrared light into the reaction vessel. The substances it contains absorb a portion of the light; the rest is scattered back and analyzed by a detector. Each substance “swallows” the light at different specific wavelengths. The result is an absorption spectrum which allows to precisely identify each substance – similar to the identification of a human being based on his finger print. With this kind of spectrometer, it will soon be possible to precisely determine the concentration of the reactant materials in the reaction vessel as well as the quantities already transformed into the end product – at any point of time during the reaction process.
Thousand spectra per second
For this, the laser needs to meet several requirements: the emitted laser light should consist of one specific wavelength only and, moreover, has to be constantly adjustable over a vast spectral range. Thus, the laser light initially has a short wavelength which is gradually increased up to a designated value – before the procedure restarts from the beginning. The detector then determines for each wavelength, how much light is scattered back by the respective sample. A further challenge: the process of switching the laser’s emission wavelength has to be as fast as possible. Up to now, the laser needed a few seconds to tune through every wavelength and to determine the actual state of the chemical reaction being analyzed. Researchers from Fraunhofer IPMS were now able to increase this speed by a factor of 1,000 by applying a micromechanical scanning mirror. Instead of one spectrum per second, they now succeed in recording 1,000 spectra per second.
Hardly any bigger than a matchbox
The laser is just barely larger than a matchbox. Thus, it is not only suitable for the reaction vessels used in the pharmaceutical and chemical industry, it also facilitates other applications. Conceivable for the future, for instance, could be a hand-held device that would allow a police officer or customs officer to inspect suspicious substances both quickly and easily. Are we dealing with something insignificant, like flour or harmless powder – or illicit drugs? To answer this question, the agents merely would have to direct the laser beam at the substance. The detector analyzes the recorded spectrum, an underlying software compares it to numerous stored comparison spectra – and in a matter of seconds, the officers have clarity about the investigated substance.
A laboratory demonstrator model of the quantum cascade laser has already been realized. The researchers from the two Fraunhofer Institutes aim at developing a prototype of the laser by the end of 2015. On the trade fair ‘Laser – World of Photonics’ from June 22 – 25 in Munich, the scientists will present the novel infrared laser and will demonstrate its potential for spectroscopy applications. (Hall A3, Booth 121 and Hall B3, Booth 341).
Suggested Items
SMT007 Magazine July—What’s Your Competitive Sweet Spot?
07/01/2025 | I-Connect007 Editorial TeamAre you in a niche that’s growing or shrinking? Is it time to reassess and refocus? We spotlight companies thriving by redefining or reinforcing their niche—what are their insights? In the July 2025 issue of SMT007 Magazine, we spotlight companies thriving by redefining or reinforcing their niche and offer insights to help you evaluate your own.
Smarter Machines Use AOI to Transform PCB Inspections
06/30/2025 | Marcy LaRont, PCB007 MagazineAs automated optical inspection (AOI) evolves from traditional end-of-process inspections to proactive, in-line solutions, the integration of AI and machine learning is revolutionizing defect reduction and enhancing yields, marking a pivotal shift in how quality is managed in manufacturing.
Magnalytix and Foresite to Host Technical Webinar on SIR Testing and Functional Reliability
06/26/2025 | MAGNALYTIXMagnalytix, in collaboration with Foresite Inc., is pleased to announce an upcoming one-hour Webinar Workshop titled “Comparing SIR IPC B-52 to Umpire 41 Functional & SIR Test Method.” This session will be held on July 24, 2025, and is open to professionals in electronics manufacturing, reliability engineering, and process development seeking insights into new testing standards for climatic reliability.
The Death of the Microsection
06/26/2025 | Bob Neves, Reliability Assessment Solutions, Inc.I got my start out of college grinding and polishing PCB microsections. My thumbs are a bit arthritic today because of the experience (microsection grinders know what I mean). Back then, via structures were rather large, and getting to the center in six steps of grinding and polishing was easy compared to what my team has been doing recently at the lab.
Specially Developed for Laser Plastic Welding from LPKF
06/25/2025 | LPKFLPKF introduces TherMoPro, a thermographic analysis system specifically developed for laser plastic welding that transforms thermal data into concrete actionable insights. Through automated capture, evaluation, and interpretation of surface temperature patterns immediately after welding, the system provides unprecedented process transparency that correlates with product joining quality and long-term product stability.