-
- News
- Books
Featured Books
- pcb007 Magazine
Latest Issues
Current IssueInventing the Future with SEL
Two years after launching its state-of-the-art PCB facility, SEL shares lessons in vision, execution, and innovation, plus insights from industry icons and technology leaders shaping the future of PCB fabrication.
Sales: From Pitch to PO
From the first cold call to finally receiving that first purchase order, the July PCB007 Magazine breaks down some critical parts of the sales stack. To up your sales game, read on!
The Hole Truth: Via Integrity in an HDI World
From the drilled hole to registration across multiple sequential lamination cycles, to the quality of your copper plating, via reliability in an HDI world is becoming an ever-greater challenge. This month we look at “The Hole Truth,” from creating the “perfect” via to how you can assure via quality and reliability, the first time, every time.
- Articles
- Columns
- Links
- Media kit
||| MENU - pcb007 Magazine
The Pinless Registration System, Explained by DIS’ Bernd Gennat
February 17, 2016 | Pete Starkey, I-Connect007Estimated reading time: 9 minutes
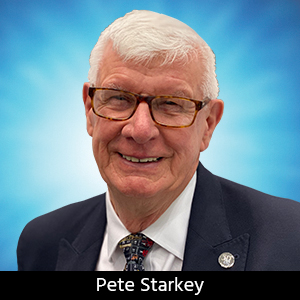
I sat down at productronica recently with Bernd Gennat, VP sales Asia and Europe for Duetto Integrated Systems (DIS Inc), for an overview of the industry, including his company’s technology. Our discussion touched on trends in multilayer registration, market requirements in Europe compared with those in China, and the benefits of pinless over hard-tooled registration systems for current and future rigid, flex and flex-rigid constructions.
Pete Starkey: Bernd, I'm very interested in the equipment and the concept of the equipment that you have explained and demonstrated to me. Basically we're talking about a pinless registration system for multilayer lamination.
It is your responsibility to market this system in Europe and the Far East. Could I first ask your opinion of the market in those two places, and the sort of things that are driving these markets?
Bernd Gennat: About Europe, I can say that since the last productronica a few things have changed for us. Especially now, customers are open for newer technology. They either want to get rid of or they want to change from the pin registration to the pinless process. In Europe in the last two years, we have sold about ten machines, which is a huge amount normally for this small market.
Now we are in negotiation with the key customers in Europe. We also have installations in the UK, where we have global players. They have companies in China, test equipment in China, and install it in China. When they see the benefits of our pinless registration system, they also install it in their European facilities.
Starkey: Looking at the Chinese market, there is now some very high level technology capability there.
Gennat: I wouldn't say overall, but you will find a lot more PCB shops now which are high level PCB shops. Companies like Tripod, Somacis or Multek are using our system, but only for a certain amount of products they're running. They're not running the whole product on a pinless registration system because they believe that the throughput on a pinless registration system is not as fast as the pin process. Normally, at end of the day, when you calculate everything together, the throughput on both processes is almost similar.
Starkey: If we set a particular complex multilayer layup as an example, where the registration tolerances were very tight, and we ran a parallel trial between a DIS system and a hard tool pin system, can you demonstrate a technical advantage in the pinless system?
Gennat: Most of our customers want to have results before they buy or make changes in their processes. They want to test our system, and we do testing in our facility. They can send us the panels, we do the alignment, and they can check the boards before lamination for accuracy. Then they see the results after lamination and they can compare it to their existing process, which is likely the pinning process. We have customers in China that have reduced their tolerances by about 30–35% against a pin process. We have this measurement from different companies already from China when they compare a pin process against a pinless process. After lamination, the result is 30–40%. The tolerance is getting better.
Starkey: If we were to put actual dimensions on those percentage improvements, what would be a typical positional accuracy?
Gennat: I would say now, when you run the old process like the pin process, in good cases you can reach maybe 75 microns, which is 3-mil alignment after lamination. With our process we have customers that already have cut it down to 30 microns, which is a little bit more than a mil in total.
Starkey: What sort of panel size are we talking about?
Gennat: We can have very small panels, but that is more for the European market. They are around 12–14 inches but it can go up to 24 or 30 inches. We also can manufacture machines for back panels up to 54 inches long.
Starkey: And that sort of alignment accuracy would apply equally to the large panels?
Gennat: Yes, also to the large panels. We have customers that normally process panels 530 x 610 mm (21” x 24”) with this accuracy.
Starkey: And any position on that panel?
Gennat: Yes, it of course is not just our system that makes this possible, the customer has to have good control of their scaling, material as well as lamination cycle. The ability to measure panels out of our system and then go through the lamination and re-measure the same panel gives the customer the ability to fine tune their process. This is not physically possible with a pin lamination process.
Starkey: I know from personal experience that the materials we're working with are not particularly good engineering materials from a dimensional stability point of view. I know the manufacturers of innerlayer materials go to a lot of trouble to try to minimize the dimensional changes that occur during the processing of the material. There are several systems available on the market which will build up a statistical model in respect of a particular material, so that compensating factors may be applied at the pre-production stage such that the material, when it is laminated, is going to move slightly, but you know where and to what extent it's going to move.
If the material is going to move in-process, does it have the ability with a pinless system to move with less mechanical stressing built into the laminated panel, which may reveal itself then at a later stage of the PCB manufacture or during some stage of the assembly process?
Gennat: I cannot eliminate material movement due to scaling; that is mission impossible. Like you mentioned, there's measurement software out there where you can check the boards after lamination. This is one benefit of a pinless process. You've got a welded, multi-layer board so you can check the board before lamination. How much has the material moved before lamination? You can take these measurements and then compare them with the data after lamination. The result then is that you can change your scaling, and you get better registration if you compensate your scaling for each core. We also can supply our camera system to measure the exact spread of each core. The customer can use this data as well.
Starkey: What is the future, as you see it, for a supplier of registration equipment in the business of manufacturing multilayers?
Gennat: Based on my experience, I would say the pinless registration will get more and more popular in most of the PCB shops because, like we discussed already, you can reduce your alignment tolerance by 30–40%. DIS is also now developing a new system that we call a measurement system. This can be added to each existing system like a standalone unit. It's not finished yet, but we will introduce it at the next IPC show in the USA.
Starkey: What will be the function of this system?
Gennat: The system will measure each core in the corners where the customer has the most critical points. We'll measure each core from top and bottom. We use the data for our alignment accuracy. Nowadays, we find from our German and Chinese customers that traceability is an issue. We have the opportunity to read for each core a DMC code so the customer cannot make any mistakes with the layup sequence; a mistake for a high-layer board can cost you a lot of money. The data also can be used as compensation data. Let's say you measure one core in the corners from top and bottom and you use this data when you load the core into our machines. Then you can say the machine will be more accurate than it is nowadays. But it is just an upgrade—we find that if most people use our system with the two cameras they will already see a big step up in accuracy. But when they're running higher layer boards in the future—today it’s maybe 20 or 24 layers average in China for some of our customers —when it comes to about 40 layers or tighter lines, then they’ll need a machine like we have in development now.
Starkey: From your point of view in working very closely with your customer, you can satisfy his present requirement very well, but you can also have a good understanding of his future requirement. Therefore, you can develop the equipment for when his future requirement appears—you already have the solution developed and in place.
Gennat: This is also the difference between the European market and the Chinese market. Each market has a different requirement. Regarding future requirements, we developed and introduced the first mutli-camera system at IPC in 2007 and it was too early for the market then, but we believe that the market is ready now for this type of system as we have discussed. So we have always tried to see where the technology is taking us. This is why we are always ahead in registration systems development.
Starkey: You've mentioned a difference; what other differences exist between the European and Chinese markets?
Gennat: Here in Europe you have more prototype shops and high-layer shops. In China it's still more mass production. High-layer jobs exist in China, but it is different there. In Europe, the job is changing every day or every second day. In China they're doing the same product year after year. This is a difference between China and Europe.
Starkey: Your equipment is equally suitable for each?
Gennat: Yes, we have machines for both types of customer. We have machines for low volume and we also have high-volume machines in our product range. Listening to our customers’ future needs, now we are talking about rigid boards, but there are also flex boards and flex-rigid boards and we also have solutions for these applications.
Starkey: I would imagine that flex in its own right, but particularly flex-rigid, and I can speak from personal experience, represents some quite remarkable challenges in registration.
Gennat: When we're talking about flex or flex-rigid boards, we found out that some customers were still doing a lot of jobs by hand. They were doing the alignment and the tack-welding by hand. Three years ago we developed a machine that did a similar job, but using a vision system to align the boards and then do the tack-welding. The process is similar, but we are not doing it by hand. We are doing it with CCD systems. The market for flex, especially flex-rigid boards, is getting higher and higher. We can deliver customer solutions for these, but the main business for us is still the rigid boards because this is still the mass market today. We have partnered with some customers and are now in the process of developing a rigid-flex process, once we have a good system in place, we will then develop a system to use that process.
Starkey: Thanks very much indeed for a very interesting discussion and a very clear explanation. I'm very grateful.
Gennat: Thank you very much.
Testimonial
"In a year when every marketing dollar mattered, I chose to keep I-Connect007 in our 2025 plan. Their commitment to high-quality, insightful content aligns with Koh Young’s values and helps readers navigate a changing industry. "
Brent Fischthal - Koh YoungSuggested Items
Flexible Circuit Technologies to Host Free Flex Heater Webinar
08/18/2025 | Flexible Circuit TechnologiesGlobal Supplier of flexible circuits, flex design services, and assembly/box-build services, Flexible Circuit Technology will host their latest webinar, "Thermal Precision Meets Flexibility: The Technology Behind Heater Circuits" on Tuesday, August 26th, 2025 at 11 AM EDT.
A.R.T. Ltd. Nominated in Four Categories at 2025 Instrumentation and Electronics Industry Awards
08/11/2025 | A.R.T. Ltd.Advanced Rework Technology Ltd. (A.R.T. Ltd.), a leading provider of electronics training and consultancy, has been shortlisted in four categories at the 2025 Instrumentation and Electronics Industry Awards, including Industry Personality, Academic Support, Rising Star, and Best Customer Service.
EMC Taiwan Receives IPC-4101 Qualified Products Listing Certification
08/08/2025 | Global Electronics AssociationIPC’s Validation Services Program has awarded an IPC-4101 Qualified Products Listing (QPL) to Elite Materials Co. (EMC), an electronics base material manufacturing company headquartered in Taoyuan City, Taiwan.
Global Excellence in PCB Design: The Global Electronics Association Expands to Italy
08/07/2025 | Global Electronics AssociationIn today's rapidly evolving electronics industry, printed circuit boards (PCBs) serve as the critical backbone influencing the success, reliability, and time-to-market of countless products. Recognizing this essential role, the Global Electronics Association (formerly IPC), a worldwide leader in electronics standards, certification, and education, is now expanding its internationally acclaimed PCB design training to Italy.
Dana on Data: Best Practices in Interpreting Drawing Notes—‘Use Latest Revision’
08/07/2025 | Dana Korf -- Column: Dana on DataThe global nature of electronics manufacturing requires clear, consistent, and precise communication, particularly in technical documentation. An area where miscommunication often arises is in interpreting drawing notes—small lines of text with the potential to dramatically impact product quality, manufacturing efficiency, and customer satisfaction.