-
- News
- Books
Featured Books
- pcb007 Magazine
Latest Issues
Current IssueInventing the Future with SEL
Two years after launching its state-of-the-art PCB facility, SEL shares lessons in vision, execution, and innovation, plus insights from industry icons and technology leaders shaping the future of PCB fabrication.
Sales: From Pitch to PO
From the first cold call to finally receiving that first purchase order, the July PCB007 Magazine breaks down some critical parts of the sales stack. To up your sales game, read on!
The Hole Truth: Via Integrity in an HDI World
From the drilled hole to registration across multiple sequential lamination cycles, to the quality of your copper plating, via reliability in an HDI world is becoming an ever-greater challenge. This month we look at “The Hole Truth,” from creating the “perfect” via to how you can assure via quality and reliability, the first time, every time.
- Articles
- Columns
- Links
- Media kit
||| MENU - pcb007 Magazine
Beyond FR-4: High-Performance Materials for Advanced Designs, Part 1
May 3, 2016 | Advanced CircuitsEstimated reading time: 4 minutes
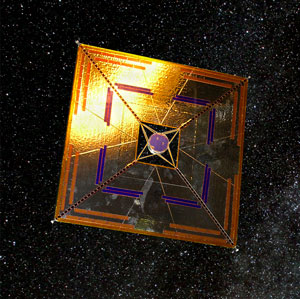
The Evolution of FR-4
In the past 40-plus years of PCB manufacturing, the primary material of choice has overwhelmingly been e-glass supported FR-4 resin laminates. This is due to the excellent dimensional stability and reasonably acceptable thermal performance (based on glass transition temperature [Tg] and decomposition temperature [Td]). In general, these materials exhibit impressive performance and excellent cost for a wide range of applications.
Cheaper and lower performance materials such as the CEM class and earlier G10 and FR-5 formulations have largely disappeared and are no longer used in mainstream products. There are still very low-cost foreign die-cut low-tech laminates used for very inexpensive and simple circuits but again have largely been replaced by the competitive price and superior performance of modern FR-4 materials.
Now, as the circuit board has become an integral part of the signal path with controlled impedance and specific transmission line performance specifications necessary for the design, higher performance materials have emerged in the FR-4 category to meet the need. High-speed designs requiring lower dielectric constant (Dk) and lower loss tangent have driven materials R&D to provide advanced FR-4 laminates such as Panasonic Megtron 6, Isola FR408, Nelco N4000-13, and even e-glass engineered to lower the Dk such as Nelco’s SI (for signal integrity) cloth. More and more modern designs are moving to these higher speed FR-4 offerings.
But there are applications that demand even greater thermal performance and severe environment reliability that requires materials with specific qualities not present in these modern FR-4 laminates. And some of these materials have been with the industry for decades but never found a wider audience due to limited supply and/or higher cost.
Polyimide
This legacy material has been with us for decades and continues to provide a solution for designs requiring increased thermal performance, higher operating temperatures, and severe environment capability. Compared to FR-4’s glass transition temperature typically in the 170–180°C range (typical FR-4 chosen for medium to advanced designs), polyimide’s Tg is in the 260°C area. The decomposition temperature is well over 400°C (lead-free assembly requires a typical 340°C or greater), and the maximum operating temperature (MOT) as tested/certified by Underwriters Laboratories (UL) is in the 140– 210°C range (short and long term testing qualification). This is much greater than the MOT of FR-4 which is typically 130°C.
There are a couple of technical issues to be aware of when selecting polyimide—the first being which chemistry formulation to use. Most polyimide laminates and prepregs are available in brominated and non-brominated blends (the flame retardant which is also used in FR-4). Non-MDA (methylenedianiline) formulations also tend to be less brittle. One issue to watch is the moisture absorption characteristics as polyimide can exhibit higher leakage as compared to FR-4 resin systems. Overall, it is best to compare your design requirements carefully in all areas to be sure that polyimide will provide the necessary benefits without undue negative performance issues.
PPO/PPE
For many years, Getek has been a choice for designers requiring a material with superior characteristics for higher speed designs. Polyphenylene oxide (PPO) epoxy resin is the closest to FR-4, but exhibits a lower Dk (3.60) and Df (0.009) in an affordable material that is supported by most PCB fabrication shops due to standard manufacturing specifications. However, in recent years the supply has been reduced as it remains a material not quite in the mainstream, so suppliers now manufacture it on an as-ordered basis resulting in typically longer lead times.
A newer material to excite the industry in the past few years, and one that is rapidly increasing its market share is Panasonic’s Megtron 6, which comes in a PPO (as well as PPE) blend. The superior performance is due to very low Dk and Df so it is a natural candidate for high-speed designs. The tradeoff is that it is a Japanese-manufactured material so domestic USA stocking and local availability can vary accordingly.
High-frequency/RF Materials (hydrocarbon/ceramic, PTFE, etc.)
Both Rogers Corporation and Taconic offer several flavors of materials engineered to address the needs of the high-frequency, microwave & RF world. These are specific laminates, often requiring different types of b-stage/prepreg or bonding sheets to laminate them for multilayer designs.
By far the most commonly used is the Rogers RO4000 series of high-frequency materials. RO4350B laminate is a hydrocarbon/ceramic base, which can be manufactured using standard FR-4 type multilayer processes, making it not only popular but economical to manufacture. Low dielectric loss is the major appealing characteristic of this material. Multilayers can be constructed of a “pure package” using Rogers 4450 prepreg, or by using standard FR-4 prepreg. Popular constructions limit the Rogers material to the caps of the stackup thereby managing overall cost by using the material only where it is required, and filling the remainder of the board with standard FR-4 cores/prepreg.
PTFE, commonly known as Teflon®, is another fairly common callout for this genre’s material requirements. There are many different formulations and laminates such as Rogers 3000 series ceramic-filled PTFE composites, R/T Duroid 5870 and 5880 glass microfiber reinforced PTFE, etc. They can be very difficult in multilayer configurations however, as some require the use of high-temperature bonding films or adhesives. The old saying that “nothing likes to stick to Teflon” sometimes holds true! But their extremely low loss characteristics make them ideal for exacting stripline and microstrip circuit designs.
Next Generation Laminates and Materials
There are a multitude of materials and laminates that are used in today’s modern PCB designs. We will continue our examination of these materials in Part 2, to be published within the next two weeks.
For more information about printed circuit board materials available for manufacturing advanced PCB designs, click here.
Testimonial
"We’re proud to call I-Connect007 a trusted partner. Their innovative approach and industry insight made our podcast collaboration a success by connecting us with the right audience and delivering real results."
Julia McCaffrey - NCAB GroupSuggested Items
Happy’s Tech Talk #41: Sustainability and Circularity for Electronics Manufacturing
08/13/2025 | Happy Holden -- Column: Happy’s Tech TalkI attended INEMI’s June 12 online seminar, “Sustainable Electronics Tech Topic Series: PCBs and Sustainability.” Dr. Maarten Cauwe of imec spoke on “Life Cycle Inventory (LCI) Models for Assessing and Improving the Environmental Impact of PCB Assemblies,” and Jack Herring of Jiva Materials Ltd. spoke on “Transforming Electronics with Recyclable PCB Technology.” This column will review information and provide analysis from both presentations.
EMC-Taiwan Announces Further Investment in North America
08/11/2025 | Elite Material Co. LtdElite Material Company (EMC)-Taiwan announced that it has made a commitment to invest $80 million dollars in the Arlon EMD factory in Rancho Cucamonga, CA it acquired at the end of 2020.
EMC Taiwan Receives IPC-4101 Qualified Products Listing Certification
08/08/2025 | Global Electronics AssociationIPC’s Validation Services Program has awarded an IPC-4101 Qualified Products Listing (QPL) to Elite Materials Co. (EMC), an electronics base material manufacturing company headquartered in Taoyuan City, Taiwan.
DuPont Reports Second Quarter 2025 Results
08/06/2025 | PRNewswireNet sales increased 3% led by organic sales growth of 2% which consisted of a 4% increase in volume partially offset by a 2% decrease in price. Currency was a 1% benefit.
Insulectro Promotes Mitchell Benson to Product Manager for Laminates
07/29/2025 | InsulectroInsulectro, the largest distributor of materials used in the manufacturing of printed circuit boards and printed electronics, announces the promotion of Mitchell Benson to Product Manager for its rigid laminate portfolio.